Introduction: When Precision Reigns Supreme
In the world of machining, achieving a flawless surface finish is often the hallmark of exceptional craftsmanship. Whether it’s the gleaming surface of a precision component or the intricate details of a delicate part, the quest for perfection drives the pursuit of ever-finer finishes. At the forefront of this pursuit stand Type C carbure brasé conseils, meticulously engineered to deliver the ultimate in surface quality and dimensional accuracy.
This article delves into the realm of Type C carbide brazed tips, unveiling their unique attributes, advantages, and the reasons why they’re the top choice for machinists seeking to achieve impeccable results.
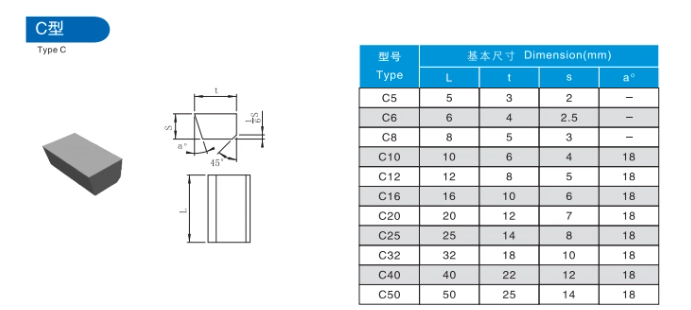
The Essence of Finishing: A Symphony of Precision and Finesse
Beyond Roughing and Shaping
While roughing operations focus on removing large amounts of material quickly, and semi-finishing operations bridge the gap, finishing is where the true artistry of machining shines. It’s about achieving:
- Exceptional Surface Smoothness: Minimizing surface roughness to create a mirror-like finish or meet stringent surface finish requirements.
- Precise Dimensional Accuracy: Holding tight tolerances to ensure that parts conform to exact specifications.
- Enhanced Aesthetics and Functionality: A superior surface finish not only enhances a part’s visual appeal but can also improve its functionality by reducing friction, wear, and corrosion.
Type C Carbide Brazed Tips: Architects of Exquisite Surfaces
A Fusion of Sharpness and Finesse
Type C carbide brazed tips are purpose-built for finishing operations, distinguished by their:
- Sharp Positive Rake Angles: The rake face slopes downwards towards the cutting edge, creating a sharp cutting action that shears material cleanly, leaving a smooth surface behind. This geometry minimizes cutting forces and reduces the tendency for material to build up on the cutting edge, both of which contribute to a finer finish.
- Petits rayons de nez : The nose radius, the rounded portion at the tip’s cutting edge, is kept small in Type C tips. This allows for:
- Finer Surface Finishes: A smaller nose radius leaves behind finer surface irregularities, resulting in a smoother surface.
- Tighter Tolerance Control: The precise cutting action of a small nose radius enables the machining of intricate features and the holding of tight dimensional tolerances.
- Grades de carbure à grain fin : Type C tips often utilize fine-grained carbide grades with high hardness and wear resistance. These grades:
- Maintenir des bords de coupe aiguisés : Essential for achieving and maintaining fine surface finishes over extended machining periods.
- Minimiser l'usure des arêtes de coupe : Reducing the need for frequent tool changes and ensuring consistent surface quality throughout the machining process.
Advantages of Type C Carbide Brazed Tips in Finishing
Elevating Surface Quality and Precision
The specialized characteristics of Type C carbide brazed tips translate into several key advantages for finishing operations:
- Finitions de surface supérieures : Their sharp cutting edges and small nose radii enable the achievement of exceptionally smooth surfaces, often eliminating the need for subsequent grinding or polishing operations.
- Tight Tolerance Control: The precise cutting action of Type C tips allows for the machining of intricate features and the holding of tight dimensional tolerances, ensuring that parts meet exacting specifications.
- Durée de vie prolongée de l'outil : While not subjected to the same impact loads as roughing tips, Type C tips still benefit from wear-resistant carbide grades, providing extended tool life, especially in finishing operations where cutting parameters are typically lower.
- Polyvalence dans la sélection des matériaux : Type C tips are well-suited for finishing a wide range of materials, including aluminum, brass, plastics, and even some steels, depending on the specific grade and coating.
Applications of Type C Carbide Brazed Tips
Where Precision Takes Center Stage
Type C carbide brazed tips are the preferred choice for finishing operations where surface quality and dimensional accuracy are paramount:
- Precision Turning: Creating smooth, accurate diameters on cylindrical workpieces.
- Face : Producing flat, perpendicular surfaces.
- Ennuyeux : Enlarging and finishing existing holes.
- Rainurage : Machining precise grooves for seals, O-rings, or retaining rings.
- Finishing Cuts in Milling: While not typically used for heavy milling, Type C tips can be employed for light finishing cuts in milling operations where surface finish is critical.
Choosing the Right Type C Carbide Brazed Tip: Factors to Consider
Fine-Tuning Your Tooling Selection
Selecting the optimal Type C carbide brazed tip involves careful consideration of several factors:
- Matériau de la pièce : La dureté, l'abrasivité et les propriétés thermiques du matériau influencent le choix de la nuance de carbure et du revêtement.
- Finishing Operation: The specific finishing operation, such as turning, facing, or boring, dictates the required tip geometry and size.
- Exigences en matière de finition de surface : L'état de surface souhaité, souvent spécifié en termes de Ra (rugosité moyenne) ou de Rz (rugosité moyenne de la crête à la vallée), est un facteur primordial dans le choix de la pointe.
- Exigences de tolérance : Les tolérances dimensionnelles requises influencent le choix de la géométrie de la pointe et la préparation de l'arête de coupe.
- Capacité des machines-outils : The rigidity and precision of the machine tool can influence the achievable surface finish and tolerances.
Type C Carbide Brazed Tip Selection: A Simplified Guide
To aid in the selection process, here’s a table summarizing typical applications and considerations for different Type C tip geometries:
Type C Tip Geometry | Applications typiques | Principales considérations |
---|---|---|
Insert rond | General-purpose finishing, turning, facing | Provides a good balance of sharpness and strength |
Diamond Insert | Precision turning, boring, grooving | Offers a sharper cutting edge for finer finishes |
Triangle Insert | Turning, facing, grooving | Provides three cutting edges for increased versatility |
Frequently Asked Questions about Type C Carbide Brazed Tips
Q1 : Peut-on Type C carbide brazed tips pour les opérations d'ébauche ?
A1 : While possible in some limited cases with very light cuts, Type C tips are not designed for roughing and their use in such applications is not recommended due to the risk of edge chipping or breakage.
Q2: What are the signs of wear on a Type C carbide brazed tip?
A2 : Common wear signs include rounding of the cutting edge, wear on the rake or flank face, and built-up edge (BUE) formation on the cutting edge.
Q3: How can I achieve the best possible surface finish with a Type C carbide brazed tip?
A3 : Les facteurs clés comprennent la sélection de la géométrie et de la qualité de pointe appropriées à l'application, l'optimisation des paramètres de coupe (en utilisant des avances et des profondeurs de coupe plus faibles), l'application correcte du liquide de coupe et le maintien d'un réglage rigide de la machine.
Q4: What is the difference between a round insert and a diamond insert Type C tip?
A4 : Round inserts provide a good balance of sharpness and strength for general-purpose finishing, while diamond inserts offer a sharper cutting edge for achieving even finer surface finishes.
Q5: When would I choose a triangle insert Type C tip?
A5 : Triangle inserts are a versatile choice for turning, facing, and grooving, offering three cutting edges for increased tool life and cost-effectiveness.