Vue d'ensemble
Carbure solide fraises en bout are essential tools in the machining industry, known for their precision, durability, and efficiency. This comprehensive guide explores everything you need to know about solid carbide end mills, from what they are and how they work to their applications and market trends. Whether you’re a seasoned machinist or a newcomer to the world of machining, this article will provide valuable insights into the benefits and uses of solid carbide end mills.
Introduction détaillée
What is a Solid Carbide End Mill?
A solid carbide end mill is a cutting tool used in industrial milling applications. Made from tungsten carbide, these tools are known for their hardness, wear resistance, and ability to maintain a sharp edge. They are designed for precision machining and are often used in CNC (Computer Numerical Control) machines to create complex shapes and profiles.
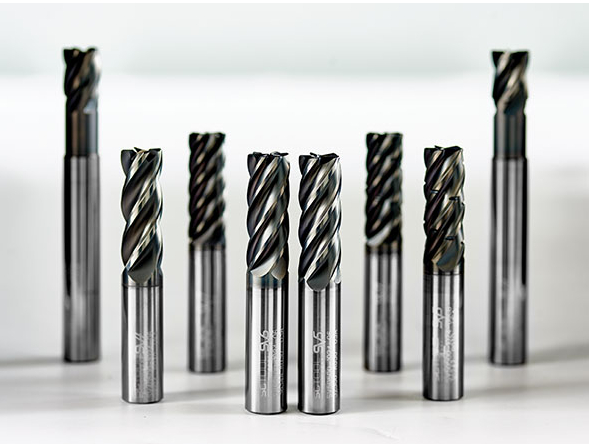
How Solid Carbide End Mills Work
Solid carbide end mills work by rotating at high speeds and cutting through materials using their sharp edges. The design of the flutes (the grooves on the cutting surface) allows for efficient removal of material, reducing heat buildup and extending the tool’s life. The rigidity and toughness of carbide allow these end mills to cut through hard materials with ease, providing a smooth and precise finish.
How to Use Solid Carbide End Mills
Using solid carbide end mills requires proper setup and operation to maximize their efficiency and lifespan. Here are some general steps to follow:
- Select the Right End Mill: Choose the appropriate type and size based on the material you’re working with and the desired finish.
- Set Up the CNC Machine: Ensure the machine is properly calibrated and the end mill is securely mounted.
- Determine Cutting Parameters: Set the correct speed, feed rate, and depth of cut to match the material and end mill specifications.
- Monitor the Process: Keep an eye on the machining process to ensure smooth operation and adjust parameters as needed.
- Entretien régulier: Sharpen and replace end mills as necessary to maintain optimal performance.
How Solid Carbide End Mills are Manufactured
The manufacturing process of solid carbide end mills involves several steps:
- Mixing Raw Materials: Tungsten carbide powder is mixed with cobalt to form a composite material.
- Appuyer sur: The mixture is pressed into the desired shape under high pressure.
- Frittage: The pressed material is heated to a high temperature to bond the particles together.
- Broyage: The sintered blanks are ground to precise dimensions and shapes.
- Revêtement (optional): Some end mills are coated with materials like titanium nitride to enhance performance.
Tendances du marché
The market for solid carbide end mills is growing, driven by advancements in manufacturing technology and increased demand for precision machining. Key trends include:
- Utilisation accrue dans les secteurs de l'aérospatiale et de l'automobile: The need for high-precision parts in these industries drives demand for solid carbide end mills.
- Advancements in Coating Technology: New coatings improve tool life and performance, making carbide end mills more efficient.
- Adoption of High-Speed Machining: As industries adopt high-speed machining, the demand for durable and precise end mills increases.
Spécifications des produits
Solid Carbide End Mills: Features and Specifications
Catégorie | Détails |
---|---|
Type | Square End Mills, Ball End Mills, Corner Radius End Mills, Roughing End Mills, etc. |
Matériau | Tungsten Carbide with Cobalt Binder |
Propriétés | High Hardness, Wear Resistance, Heat Resistance, Toughness |
Caractéristiques | Multiple Flute Designs (2, 3, 4, 5+), Coated/Uncoated, Various Helix Angles |
Spécifications | Diameter: 1mm to 25mm, Length: Up to 150mm, Flute Length: Varies |
Notes | Micro-grain, Sub-micron, Ultra-fine |
Normes | ISO, ANSI, DIN, JIS |
Similar Products for Comparison
Produit | Matériau | Propriétés | Applications |
---|---|---|---|
Acier rapide (HSS) | High-Speed Steel | Good Toughness, Moderate Hardness | General Machining, Low-Speed Cutting |
Cobalt End Mills | HSS with Cobalt | Enhanced Hardness, Good Wear Resistance | Stainless Steel, High-Temperature Alloys |
Ceramic End Mills | Céramique | Extreme Hardness, Brittle | Hard Materials, High-Precision Tasks |
Applications of Solid Carbide End Mills
Solid carbide end mills are used in various industries due to their versatility and precision. Here are some common applications:
- Industrie automobile: Machining engine components, transmission parts, and other precision parts.
- Industrie aérospatiale: Manufacturing turbine blades, aircraft components, and other high-precision parts.
- Industrie médicale: Creating surgical instruments, implants, and other medical devices.
- Mold and Die Industry: Producing molds and dies for plastic injection molding and metal stamping.
- Usinage général: Milling, contouring, and profiling in various materials like steel, aluminum, and composites.
Comparaison des fournisseurs
Comparison of TRUER with Other Suppliers
Fournisseur | Localisation | Fourchette de prix | Par pièce | Spécialités |
---|---|---|---|---|
TRUER | Chine | $30 – $100 | $45 | High-Precision, Advanced Coatings, Durable |
MSC Industrial | ÉTATS-UNIS | $35 – $110 | $50 | Wide Range, Fast Shipping, Custom Orders |
Matériaux Mitsubishi | Japon | $40 – $120 | $55 | Innovative Designs, High Performance |
Outils Seco | Suède | $45 – $130 | $60 | Premium Quality, Extensive Support |
Pros and Cons of Solid Carbide End Mills
Avantages et limites
Aspect | Avantages | Limites |
---|---|---|
Durabilité | High wear resistance, long tool life | Coût initial plus élevé |
Précision | Maintains sharp edge, high accuracy | Requires precise setup and operation |
Efficacité | Fast material removal, reduces machining time | Can be brittle if not handled correctly |
Polyvalence | Suitable for various materials and applications | Limited to specific machining environments |
Description of Pros and Cons
Solid carbide end mills offer numerous advantages, including high durability, precision, efficiency, and versatility. They are ideal for high-speed machining and can handle a wide range of materials, making them a popular choice in industries requiring high-precision parts. However, they come at a higher initial cost and require precise handling and operation to avoid brittleness.
Related Topics: Expanding Your Knowledge
Technologies avancées de revêtement
Coatings like titanium nitride (TiN), titanium carbonitride (TiCN), and diamond-like carbon (DLC) extend the life of carbide end mills and enhance their performance. These coatings provide additional hardness, reduce friction, and improve heat resistance, making the tools more efficient and durable.
High-Speed Machining Techniques
High-speed machining (HSM) involves cutting at significantly higher speeds and feed rates than traditional methods. Solid carbide end mills are particularly suited for HSM due to their hardness and wear resistance. Understanding HSM techniques can help you maximize the performance of your carbide end mills.
Tool Holding and Fixturing
Proper tool holding and fixturing are crucial for the performance of solid carbide end mills. Using high-quality tool holders and ensuring secure fixturing can reduce runout, improve accuracy, and extend tool life.
Why Choose TRUER Solid Carbide End Mills
TRUER solid carbide end mills stand out in the market due to their exceptional quality, precision, and advanced technology. Here are some reasons to choose TRUER:
- High-Precision Manufacturing: TRUER uses state-of-the-art manufacturing processes to produce end mills with tight tolerances and excellent surface finishes.
- Revêtements avancés: TRUER offers a range of advanced coatings that enhance tool life and performance.
- Global Availability: With a global distribution network, TRUER ensures timely delivery and support for customers worldwide.
- Soutien à la clientèle: TRUER provides extensive technical support and customer service to help you achieve the best results with their products.
FAQ: Frequently Asked Questions
Q1: What materials can solid carbide end mills cut?
A1 : Solid carbide end mills can cut a wide range of materials, including steel, stainless steel, aluminum, titanium, and composites. Their hardness and wear resistance make them suitable for both soft and hard materials.
Q2: How do I choose the right solid carbide end mill for my application?
A2 : Consider the material you’re machining, the type of cut required, and the desired finish. Factors like flute design, coating, and tool geometry also play a role in selecting the right end mill.
Q3: How can I extend the life of my solid carbide end mills?
A3 : To extend tool life, use the correct cutting parameters, ensure proper tool holding and fixturing, and perform regular maintenance. Using coated end mills and employing high-speed machining techniques can also help.
Q4: What is the difference between coated and uncoated carbide end mills?
A4 : Coated end mills have a thin layer of material, such as titanium nitride, that enhances their performance by reducing friction, improving heat resistance, and extending tool life. Uncoated end mills are suitable for general-purpose machining but may wear out faster.Want to know more? Please cliquer.
Q5: Can solid carbide end mills be resharpened?
A5 : Yes, solid carbide end mills can be resharpened to extend their life. However, resharpening should be done by a professional to maintain the tool’s geometry and performance.