Introduction: The Foundation of Precision Tooling
In the realm of high-precision manufacturing, where tolerances are tight and performance expectations are paramount, precision carbide rod blanks reign supreme. These cylindrical rods, meticulously crafted from cemented carbide, serve as the foundational building blocks for a diverse array of cutting tools, wear parts, and other critical components.
This comprehensive guide delves into the world of precision carbide rod blank machining services, exploring their significance, the intricacies of the machining process, and the advantages of partnering with a trusted provider like TRUER.
Precision Carbide Rod Blanks: What Are They?
Understanding the Essence of Precision
Precision carbide rod blanks are precisely machined cylindrical rods composed of cemented carbide, a composite material renowned for its exceptional hardness, wear resistance, and ability to withstand extreme temperatures and pressures. These blanks serve as the starting point for manufacturing a wide range of tools and components that demand unwavering accuracy and durability.
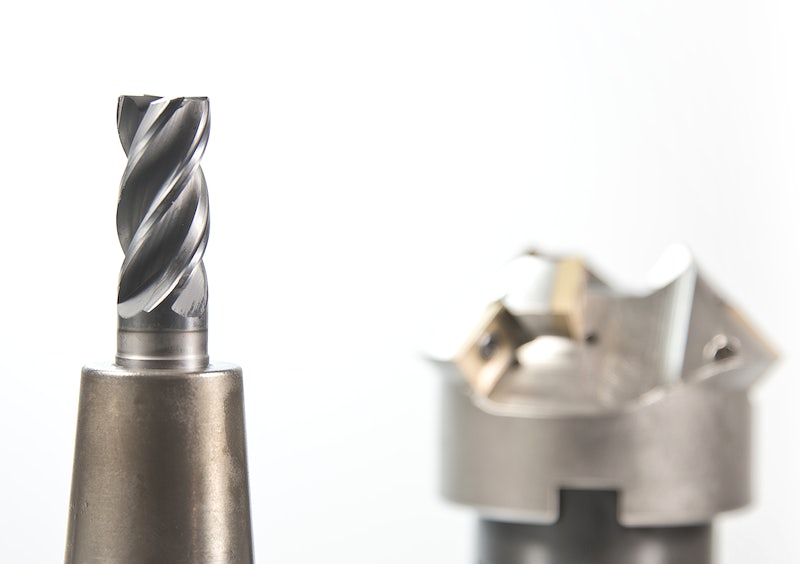
The Art of Precision Carbide Rod Blank Machining
Transforming Raw Material into Precision Components
The journey from raw carbide blank to a finished precision component is a testament to engineering expertise and advanced machining capabilities. The process typically involves the following key steps:
- Sélection des matériaux : The first crucial step is selecting the appropriate carbide grade based on the intended application’s specific requirements. Factors such as hardness, toughness, wear resistance, and heat resistance dictate the ideal grade for optimal performance.
- Découpage : Utilizing specialized diamond-tipped cutting tools, the carbide rod is cut to the desired length with exceptional precision. This step demands meticulous control to ensure dimensional accuracy and prevent any damage to the carbide material.
- Broyage : Grinding operations, often performed on CNC grinding machines equipped with diamond grinding wheels, shape the carbide rod into its final cylindrical form. This process removes excess material and achieves the desired diameter and surface finish with micron-level precision.
- Lapping and Polishing: For applications demanding the highest levels of surface finish and dimensional accuracy, lapping and polishing operations may be employed. Lapping utilizes fine abrasive particles to remove microscopic imperfections, while polishing creates a mirror-like surface finish.
- Inspection : Throughout the machining process, rigorous quality control measures are implemented to ensure that each precision carbide rod blank meets the stringent tolerances and specifications outlined by the customer.
Precision Carbide Rod Blank Properties: A Closer Look
Unveiling the Characteristics that Matter
The exceptional performance of precision carbide rod blanks stems from the unique properties of cemented carbide.
Table 1: Typical Properties of Cemented Carbide Rod Blanks
Propriété | Description | Valeurs typiques |
---|---|---|
Dureté (HRA) | Résistance à l'indentation et à la rayure | 88-95 |
Résistance à la rupture transversale (TRS) | Capacité à résister aux forces de flexion | 1500-2500 MPa |
Densité | Masse par unité de volume | 13,5-15,0 g/cm³ |
Coefficient of Thermal Expansion (CTE) | Rate of expansion with temperature changes | 4.5-6.5 x 10⁻⁶/°C |
Conductivité thermique | Capacité à conduire la chaleur | 50-120 W/mK |
Applications of Precision Carbide Rod Blanks
Fueling Innovation Across Industries
The versatility and exceptional properties of precision carbide rod blanks have led to their widespread adoption across a multitude of industries:
- Travail des métaux et usinage : Precision carbide rod blanks form the foundation for cutting tools such as drills, end mills, reamers, and boring bars, enabling the high-speed, high-precision machining of metals.
- Le travail du bois : Carbide’s ability to maintain a sharp edge for extended periods makes it ideal for woodworking tools. Precision carbide rod blanks are used to manufacture saw blades, router bits, and other cutting tools that deliver exceptional results in wood processing.
- Pétrole et gaz : The demanding environments of oil and gas exploration and production require tools with exceptional durability. Precision carbide rod blanks are used to create drill bits, wear parts, and other components that can withstand the harsh conditions encountered deep underground.
- Dispositifs médicaux : The medical device industry relies on precision carbide rod blanks for their biocompatibility and ability to be machined to extremely tight tolerances. Surgical instruments, implants, and other medical devices benefit from the precision and durability of carbide.
- Aérospatiale : The aerospace industry demands lightweight yet incredibly strong materials. Precision carbide rod blanks are used to manufacture components for jet engines, landing gear, and other critical aerospace applications.
Comparing Carbide Rod Blank Suppliers
Navigating the Landscape of Suppliers
Selecting the right supplier for precision carbide rod blank machining services is crucial for ensuring product quality, timely delivery, and competitive pricing.
Table 2: Comparison of Carbide Rod Blank Machining Service Providers
Fournisseur | Localisation | Fourchette de prix (par pièce, USD) | Spécialités |
---|---|---|---|
Kennametal | ÉTATS-UNIS | $50 – $1000+ | Wide range of carbide grades, complex geometries, precision grinding capabilities |
Sandvik Coromant | Suède | $60 – $1200+ | Advanced carbide grades, specialized coatings, technical support for tooling optimization |
CERATIZIT | Luxembourg | $40 – $800+ | Solutions rentables, nuances de carbure standard et sur mesure, présence industrielle mondiale |
ISCAR | Israël | $55 – $1100+ | Innovative tool geometries, expertise in specialized coatings for challenging applications |
Matériaux Mitsubishi | Japon | $65 – $1300+ | High-performance carbide grades, tight tolerances, reliable supply chain for consistent quality |
TRUER | Chine | $45 – $900+ | High-quality, cost-effective carbide rod blank machining; Expertise in geological mining products; Vertically integrated manufacturing with advanced pressing and grinding technology for superior precision and stability |
Remarque : Prices are approximate and can vary significantly based on blank size, grade, quantity, tolerances, surface finish requirements, and other factors.
Advantages and Limitations of Precision Carbide Rod Blanks
Weighing the Pros and Cons
Table 3: Advantages and Limitations of Precision Carbide Rod Blanks
Avantages | Limites |
---|---|
Dureté et résistance à l'usure exceptionnelles : Enables tools and components to withstand extreme wear and tear, extending service life and reducing downtime | Nature fragile : Carbide’s high hardness also makes it inherently brittle, making it susceptible to chipping or fracturing under impact or high stress |
High-Temperature Stability: Maintains its properties at elevated temperatures, making it suitable for high-speed machining and other demanding applications | Higher Cost Compared to Other Materials: The exceptional properties of carbide come at a higher initial cost compared to materials like high-speed steel (HSS) |
Precision Machinability: Can be machined to extremely tight tolerances, enabling the creation of high-precision tools and components | Specialized Machining Expertise Required: L'usinage du carbure nécessite un équipement, un outillage et une expertise spécialisés en raison de sa dureté et de sa nature abrasive. |
L'avantage TRUER : Pourquoi nous choisir ?
Your Trusted Partner in Precision Carbide Rod Blank Machining
- Un engagement inébranlable en faveur de la qualité : At TRUER, quality is paramount. We maintain stringent quality control measures throughout our manufacturing process to ensure that every precision carbide rod blank meets or exceeds your expectations.
- Advanced Manufacturing Capabilities: Our state-of-the-art facility is equipped with the latest CNC machining centers, grinding machines, and inspection equipment, enabling us to produce precision carbide rod blanks with exceptional accuracy and repeatability.
- Experienced Engineering Team: Our team of skilled engineers possesses extensive experience in carbide machining and can work closely with you to develop custom solutions tailored to your specific application requirements.
- Prix compétitifs et livraison dans les délais : We understand the importance of cost-effectiveness and on-time delivery. Our vertically integrated manufacturing process and efficient supply chain allow us to offer competitive pricing and reliable lead times.
Foire aux questions (FAQ)
Addressing Your Key Concerns
1. What is the typical lead time for precision carbide rod blank machining services?
Lead times vary depending on factors such as order volume, blank complexity, and current production capacity. However, we strive to provide lead times of 2-4 weeks for most orders.
2. What is the smallest diameter carbide rod that you can machine?
Our advanced grinding capabilities allow us to machine carbide rods with diameters as small as 0.5 mm with exceptional precision.
3. Can you apply coatings to precision carbide rod blanks?
Yes, we offer a range of coating services, including titanium nitride (TiN), titanium aluminum nitride (TiAlN), and diamond-like carbon (DLC) coatings, to enhance wear resistance, reduce friction, and extend tool life.
4. What types of carbide grades do you offer for precision rod blank machining?
We offer a comprehensive selection of carbide grades, including those suitable for general-purpose machining, high-speed cutting, impact resistance, and high-temperature applications. Our engineering team can assist you in selecting the optimal grade for your specific needs.
5. What information do I need to provide to request a quote for precision carbide rod blank machining?
To provide an accurate quote, we require information such as the desired carbide grade, rod diameter, length, tolerances, surface finish requirements, and order quantity. Drawings or sketches of the desired blank geometry are also helpful.