Vue d'ensemble : Conçus pour répondre à vos besoins exacts
Dans un monde qui exige précision et durabilité, personnalisé carbure solutions de boutons apparaissent comme la réponse aux défis spécifiques de l'industrie. Il ne s'agit pas de composants standard, mais de chefs-d'œuvre méticuleusement conçus pour résister à l'usure unique rencontrée dans votre application spécifique. Des environnements miniers les plus difficiles aux exigences de précision de la fabrication, les boutons en carbure personnalisés offrent des performances et une longévité inégalées.
Ce guide explore le monde des solutions personnalisées pour les boutons en carbureNous vous invitons à découvrir leur processus de création, les avantages qu'ils offrent et la manière dont un partenariat avec le bon fournisseur peut révolutionner votre approche de la résistance à l'usure et optimiser vos opérations.
Que sont les solutions personnalisées en matière de boutons en carbure ?
Au-delà de la norme : Adapter les performances à votre application
Solutions personnalisées pour les boutons en carbure représentent une rupture par rapport aux limites des composants standard, prêts à l'emploi. Ils sont méticuleusement conçus et fabriqués pour répondre aux exigences uniques de votre application spécifique :
- Sélection des matériaux : Choix de la nuance de carbure optimale, de la teneur en cobalt du liant et de tout élément d'alliage supplémentaire pour obtenir la dureté, la ténacité et la résistance à l'usure souhaitées pour vos conditions d'exploitation spécifiques.
- Optimisation de la forme : Conception de la forme idéale du bouton, en tenant compte de facteurs tels que la surface de contact, la répartition des motifs d'usure et les points de contrainte, afin de maximiser les performances et la longévité de votre application.
- Précision dimensionnelle : Fabrication selon vos spécifications dimensionnelles exactes, garantissant une adaptation précise à votre équipement et optimisant les performances, qu'il s'agisse d'un diamètre unique, d'un pas de vis spécifique ou d'une géométrie complexe.
- Méthode de fixation : Incorporer la méthode de fixation idéale, qu'il s'agisse de brasage, de soudage, de filetage ou d'une solution personnalisée, afin de garantir une intégration sûre et fiable dans vos outils ou équipements.
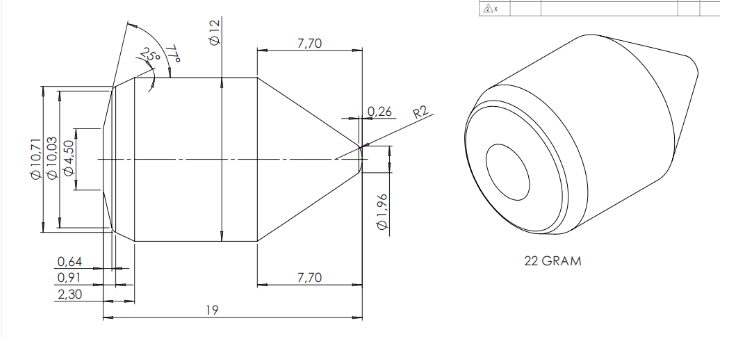
Le processus de personnalisation : Du concept à la réalité
Collaborer pour réussir : Donner vie à votre vision
Développement solutions personnalisées pour les boutons en carbure est une collaboration entre vous et le fournisseur que vous avez choisi :
- Évaluation des besoins : Une compréhension approfondie de votre application, de vos conditions de fonctionnement, de vos problèmes d'usure et de vos objectifs de performance constitue la base du processus de personnalisation.
- Conception et ingénierie : Des ingénieurs expérimentés traduisent vos exigences en une conception de bouton personnalisée, en utilisant des logiciels et des outils de simulation avancés pour optimiser la forme, la sélection des matériaux et les caractéristiques de performance.
- Prototypage et essais : Des prototypes sont souvent créés et rigoureusement testés dans des conditions simulées ou réelles afin de valider la conception, de s'assurer qu'elle répond à vos attentes en matière de performances et de permettre toutes les améliorations nécessaires.
- Production et contrôle de la qualité : Une fois la conception approuvée, les boutons personnalisés sont fabriqués à l'aide de techniques d'usinage de précision et soumis à des mesures strictes de contrôle de la qualité tout au long du processus de production, ce qui garantit une qualité et des performances constantes.
Avantages des solutions personnalisées de boutons en carbure : Une coupe au-dessus du lot
Débloquer des performances inégalées : Les avantages des solutions sur mesure
- Prolongation de la durée de vie des outils et des équipements : Les boutons personnalisés, conçus pour vos conditions d'usure spécifiques, prolongent considérablement la durée de vie de vos outils et équipements, réduisant ainsi les temps d'arrêt et les coûts de maintenance.
- Amélioration de la productivité : L'optimisation de la conception des boutons et de la sélection des matériaux permet d'améliorer l'efficacité de la coupe, du concassage ou du broyage, ce qui stimule la productivité et maximise le rendement.
- Réduction des temps d'arrêt : Des boutons qui durent plus longtemps se traduisent par moins de remplacements et une maintenance moins fréquente, ce qui minimise les temps d'arrêt coûteux et assure le bon fonctionnement de vos opérations.
- Économies de coûts : Si les solutions personnalisées peuvent avoir un coût initial plus élevé, les avantages à long terme que sont la prolongation de la durée de vie des outils, l'augmentation de la productivité et la réduction des temps d'arrêt se traduisent souvent par des économies significatives au fil du temps.
- Avantage concurrentiel : Gagnez une longueur d'avance dans votre industrie en relevant des défis d'usure spécifiques et en obtenant des performances supérieures grâce à des solutions de boutons en carbure sur mesure.
Applications dans tous les secteurs d'activité : Quand la personnalisation fait la différence
Des solutions sur mesure pour des défis variés : Un aperçu des applications industrielles
- Exploitation minière : Les boutons personnalisés pour les trépans, les outils de forage et les équipements de broyage résistent aux forces abrasives les plus dures, maximisant l'efficacité du forage et prolongeant la durée de vie des équipements dans les opérations minières souterraines et à ciel ouvert exigeantes.
- Construction et infrastructure : Des solutions sur mesure pour les fraiseuses routières, les tunneliers et d'autres équipements lourds garantissent des performances optimales et la longévité des projets de construction exigeants, du resurfaçage des routes à l'excavation des tunnels.
- Pétrole et gaz : Les boutons personnalisés pour les trépans, les stabilisateurs et autres outils de fond de puits résistent à des températures, des pressions et des formations abrasives extrêmes, maximisant ainsi l'efficacité du forage et réduisant les temps d'arrêt dans les environnements difficiles de l'exploration et de la production de pétrole et de gaz.
- L'agriculture : Les boutons spécialisés pour les outils de travail du sol, les semoirs et le matériel de récolte améliorent la résistance à l'usure et les performances dans les sols abrasifs, améliorant ainsi l'efficacité et réduisant les besoins de maintenance dans les applications agricoles exigeantes.
- Fabrication : Des boutons conçus sur mesure pour les matrices, les poinçons, les outils de coupe et les pièces d'usure optimisent les performances et prolongent la durée de vie des outils dans divers processus de fabrication, du formage des métaux à la transformation des matières plastiques.
Comparaison des fournisseurs : Prendre des décisions éclairées pour des solutions personnalisées
Trouver le bon partenaire : Naviguer dans le paysage de l'expertise et de la valeur
Fournisseur | Localisation | Fourchette de prix (par pièce) | Spécialités |
---|---|---|---|
TRUER | Chine | $3.00 – $50+ | Options de personnalisation étendues, prix compétitifs, prototypage rapide, forte orientation client |
Sandvik Coromant | Mondial | $5.00 – $75+ | Leader du secteur, large gamme de solutions standard et personnalisées, présence mondiale, forte expertise technique |
Kennametal | Mondial | $4.00 – $60+ | Fournisseur établi, large portefeuille de produits, priorité à l'innovation et au soutien des applications, portée mondiale |
Remarque : Les prix sont approximatifs et dépendent fortement des facteurs de personnalisation. Il est recommandé de contacter directement les fournisseurs pour obtenir des devis détaillés.
Avantages et limites de la personnalisation : Une perspective équilibrée
Peser le pour et le contre : prendre des décisions éclairées pour votre application
Avantages | Limites |
---|---|
Performance optimale : Adaptés à vos besoins spécifiques, ils maximisent l'efficacité et la longévité de votre application. | Coût initial plus élevé : La personnalisation implique souvent des coûts initiaux plus élevés que les solutions standard. |
Durée de vie prolongée de l'outil : Conçus pour résister à vos défis uniques en matière d'usure, ils réduisent considérablement la fréquence de remplacement. | Des délais d'exécution plus longs : La conception, le prototypage et la fabrication de solutions personnalisées nécessitent généralement des délais plus longs. |
Augmentation de la productivité : La conception optimisée et la sélection des matériaux améliorent l'efficacité de la coupe, du concassage ou du broyage. | Quantités minimales de commande : Les fournisseurs imposent souvent des quantités minimales de commande pour les solutions personnalisées, ce qui peut ne pas convenir aux besoins de petits volumes. |
Réduction des temps d'arrêt : Les boutons plus durables minimisent les temps d'arrêt liés aux changements d'outils et à la maintenance. | Complexité de la conception : Les conceptions très complexes peuvent poser des problèmes ou des limites de fabrication, nécessitant des ajustements ou des compromis. |
Au-delà des boutons : L'avenir de la résistance à l'usure
Innovation et progrès : Repousser les limites de la performance
Le domaine des solutions personnalisées en matière de boutons en carbure est en constante évolution, sous l'impulsion de.. :
- Matériaux avancés : La recherche de nouvelles nuances de carbure, de technologies de liants et de traitements de surface repousse sans cesse les limites de la résistance à l'usure, de la dureté et de la ténacité.
- Fabrication additive : Les technologies d'impression 3D ouvrent de nouvelles possibilités pour créer des géométries et des structures internes complexes de boutons en carbure, ce qui permet d'optimiser davantage les performances.
- Conception fondée sur les données : L'utilisation de logiciels de simulation, l'analyse des données et l'apprentissage automatique permettent une prédiction plus précise de l'usure, ce qui conduit à des conceptions de boutons personnalisés encore plus efficaces.
Pourquoi choisir TRUER pour vos besoins en boutons en carbure personnalisés ?
TRUER se distingue en tant que premier fournisseur de personnalisé bouton en carbure solutions, offrant :
- Un engagement inébranlable en faveur de la personnalisation : Nous nous efforçons de relever des défis uniques et de fournir des solutions sur mesure qui répondent précisément à vos besoins spécifiques.
- Approche collaborative : Nous considérons nos clients comme des partenaires, travaillant en étroite collaboration tout au long des processus de conception, de prototypage et de production afin de garantir votre entière satisfaction.
- Capacités de prototypage rapide : Notre processus de prototypage efficace nous permet d'itérer rapidement les conceptions et de valider les performances, ce qui accélère la mise sur le marché.
- Des prix compétitifs et des solutions flexibles : Nous proposons des prix compétitifs et nous nous efforçons de répondre aux différents volumes de commande, rendant la personnalisation accessible à un large éventail d'entreprises.
- Un service à la clientèle exceptionnel : Nous mettons l'accent sur l'établissement de relations durables avec nos clients, en leur offrant une communication réactive, une expertise technique et un soutien continu.
Foire aux questions : Répondre à vos questions sur la personnalisation
- Q1 : Quelles informations dois-je fournir pour obtenir une solution personnalisée pour les boutons en carbure ?
- A1 : Pour lancer le processus, nous avons besoin d'une compréhension claire de votre application, des conditions de fonctionnement (par exemple, les matériaux traités, les températures, les pressions), des problèmes d'usure, de la durée de vie souhaitée du bouton et de toutes les spécifications existantes du bouton que vous pourriez avoir.
- Q2 : Combien de temps faut-il généralement pour développer et recevoir une solution personnalisée de boutons en carbure ?
- A2 : Le délai varie en fonction de la complexité de la conception et de la nécessité de réaliser des prototypes et des essais. En général, le processus prend de 4 à 8 semaines. Nous fournissons d'emblée des estimations transparentes des délais et maintenons une communication ouverte tout au long du processus.
- Q3 : Existe-t-il des limites aux formes et aux tailles des boutons en carbure personnalisés que vous pouvez produire ?
- A3 : Bien que nous disposions de capacités étendues, des géométries très complexes ou des tailles extrêmement réduites peuvent poser des problèmes de fabrication. Nos ingénieurs travailleront en étroite collaboration avec vous pour explorer les possibilités de conception et trouver la solution optimale en tenant compte des limites éventuelles.
- Q4 : Quelle est la fourchette de prix habituelle pour les boutons en carbure personnalisés et quels sont les facteurs qui influencent le coût ?
- A4 : Les prix varient considérablement en fonction de facteurs tels que la qualité du carbure, la taille et la complexité du bouton, la quantité commandée et l'outillage spécialisé nécessaire. Nous fournissons des devis détaillés indiquant tous les coûts impliqués.