Introduction : Libérer la puissance du carbure de tungstène
Dans le domaine de la fabrication industrielle et de l'usinage, la précision, la durabilité et l'efficacité sont primordiales. Entrer ébauches en carbure cémentéLes carbures de tungstène sont les héros méconnus d'un grand nombre d'outils de pointe et de composants résistants à l'usure. Ces matériaux d'ingénierie, principalement composés de particules de carbure de tungstène liées par un liant métallique, offrent une dureté, une résistance à l'usure et une dureté à chaud exceptionnelles, ce qui les rend idéaux pour les applications exigeantes.
Ce guide complet plonge dans le monde des ébauches en carbure cémenté fabriquées sur mesure, en explorant leurs propriétés, leurs processus de fabrication, leurs applications et les avantages d'un partenariat avec un fabricant spécialisé.
Que sont les ébauches en carbure cémenté fabriquées sur mesure ?
Les ébauches en carbure cémenté sont des formes pré-frittées ou entièrement frittées de matériaux à base de carbure de tungstène, généralement de forme cylindrique ou rectangulaire, qui servent de base à divers outils de coupe, pièces d'usure et autres composants. Le terme "sur mesure" signifie que ces ébauches sont adaptées à des dimensions, des géométries, des qualités et des propriétés spécifiques, en fonction des exigences d'application uniques du client.
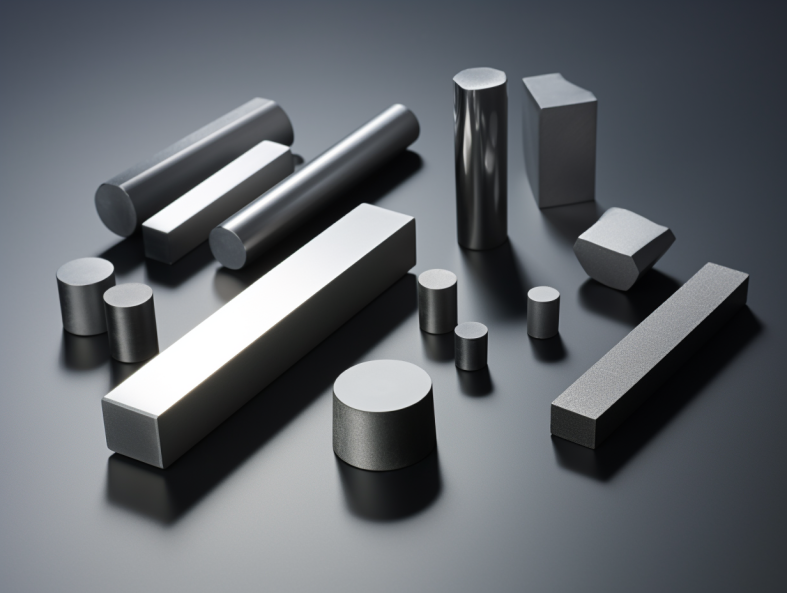
Comprendre le processus de fabrication
La production d'ébauches en carbure cémenté sur mesure implique un processus méticuleux en plusieurs étapes :
- Préparation de la poudre : La poudre de carbure de tungstène (WC) et la poudre de métal liant, généralement du cobalt (Co), sont mélangées avec précision dans les proportions souhaitées pour obtenir des propriétés spécifiques du matériau.
- Pressage : Le mélange de poudres est pressé dans la forme souhaitée à l'aide de matrices à haute pression.
- Pré-interprétation : Les ébauches pressées subissent un processus de chauffage contrôlé pour leur conférer une résistance à l'état vert et les préparer au frittage final.
- Frittage : Les ébauches pré-frittées sont soumises à des températures élevées dans un four à atmosphère contrôlée. Ce processus fusionne les particules de WC par frittage en phase liquide, ce qui donne un matériau dense et dur.
- Finition : Après le frittage, les ébauches peuvent subir diverses opérations de finition telles que le meulage, le rodage ou le polissage afin d'obtenir des dimensions et des états de surface précis.
La polyvalence des ébauches en carbure fabriquées sur mesure
Les ébauches en carbure cémenté fabriquées sur mesure offrent une polyvalence inégalée, permettant aux fabricants d'optimiser les performances des outils pour des opérations d'usinage et des types de matériaux spécifiques. En adaptant la taille des grains de WC, la teneur en cobalt et d'autres ajouts d'alliage, les fabricants peuvent affiner la dureté, la ténacité et la résistance à l'usure de l'ébauche.
Naviguer dans le monde des nuances de carbure
Les ébauches en carbure cémenté sont classées en différentes catégories en fonction de leur composition et de leurs propriétés. Le choix de la nuance appropriée est crucial pour une performance et une longévité optimales de l'outil.
Tableau 1 : Nuances courantes de carbure cémenté et leurs caractéristiques
Grade | Contenu du WC (%) | Contenu en Co (%) | Applications typiques | Propriétés principales |
---|---|---|---|---|
K01 | 94 | 6 | Finition de l'acier, de la fonte et des métaux non ferreux | Dureté élevée, excellente résistance à l'usure |
K10 | 90 | 10 | Usinage général de l'acier, de la fonte et des métaux non ferreux | Bon équilibre entre dureté et résistance |
K20 | 85 | 15 | Ebauche et coupe interrompue de l'acier et de la fonte | Ténacité élevée, bonne résistance à l'usure |
M10 | 88 | 12 | Usinage de l'acier inoxydable, des alliages à haute température et des alliages de titane | Dureté à chaud élevée, bonne résistance à l'usure |
Applications dans tous les secteurs d'activité
Les propriétés exceptionnelles des ébauches en carbure cémenté fabriquées sur mesure ont conduit à leur adoption généralisée dans de nombreuses industries :
- Travail des métaux et usinage : Ce secteur est l'un des principaux consommateurs d'ébauches en carbure, qu'il utilise pour une vaste gamme d'outils de coupe. Les forets, les fraises en bout, les plaquettes de tournage et de fraisage et les pointes de scie bénéficient tous de la dureté et de la résistance à l'usure du carbure, ce qui leur permet d'usiner divers métaux avec précision et longévité.
- Le travail du bois : L'industrie du travail du bois s'appuie sur la capacité du carbure à conserver un tranchant pendant de longues périodes. Les lames de scie à pointe en carbure produisent des coupes plus nettes avec moins d'effort, tandis que les mèches de toupie et les couteaux de raboteuse équipés d'inserts en carbure excellent dans le façonnage et le lissage du bois.
- Construction et exploitation minière : Les environnements impitoyables de la construction et de l'exploitation minière exigent des outils d'une durabilité exceptionnelle. Les forets en carbure percent sans effort le béton, la roche et d'autres matériaux résistants, tandis que les outils spécialisés de forage de la roche équipés d'inserts en carbure maximisent l'efficacité du forage et minimisent les temps d'arrêt. Les pièces d'usure en carbure protègent les composants critiques des machines lourdes contre l'abrasion et les chocs.
- Pétrole et gaz : L'extraction et le traitement du pétrole et du gaz présentent des conditions extrêmes où le carbure s'épanouit. Les outils de forage de fond munis de pointes en carbure résistent aux forces abrasives rencontrées dans les profondeurs, tandis que les bagues d'usure et les composants de vannes fabriqués en carbure garantissent la longévité et la fiabilité des équipements critiques.
- Aérospatiale : L'industrie aérospatiale exige des matériaux légers mais incroyablement solides, capables de résister à des températures élevées et à des conditions exigeantes. Le carbure joue un rôle crucial dans ce secteur, puisqu'il trouve des applications dans les aubes de turbine des moteurs à réaction, les composants résistants à l'usure des trains d'atterrissage et même les pièces structurelles nécessitant un rapport poids/résistance exceptionnel.
Comparaison des fournisseurs de flans en carbure
Le choix du bon fournisseur d'ébauches en carbure cémenté est crucial pour garantir la qualité du produit, le respect des délais de livraison et des prix compétitifs.
Tableau 2 : Comparaison des fournisseurs de flans en carbure cémenté
Fournisseur | Localisation | Fourchette de prix (par pièce, USD) | Spécialités |
---|---|---|---|
Kennametal | ÉTATS-UNIS | $10 – $500+ | Large gamme de qualités, géométries complexes, revêtements |
Sandvik Coromant | Suède | $15 – $600+ | Nuances avancées, rectification de précision, assistance technique |
CERATIZIT | Luxembourg | $8 – $400+ | Solutions rentables, qualités standard et sur mesure |
ISCAR | Israël | $12 – $550+ | Géométries innovantes, revêtements spécialisés, expertise technique |
Matériaux Mitsubishi | Japon | $14 – $650+ | Qualités à haute performance, tolérances serrées, approvisionnement fiable |
TRUER | Chine | $8 – $450+ | Ébauches en carbure de haute qualité et rentables ; expertise dans les produits miniers géologiques ; fabrication intégrée verticalement avec une technologie de pressage avancée pour une précision et une stabilité supérieures. |
Remarque : Les prix sont approximatifs et peuvent varier considérablement en fonction de la taille du flan, de la qualité, de la quantité et d'autres facteurs.
Avantages et limites des ébauches en carbure fabriquées sur mesure
Tableau 3 : Avantages et limites des ébauches en carbure cémenté fabriquées sur mesure
Avantages | Limites |
---|---|
Amélioration des performances : Propriétés sur mesure pour des applications spécifiques | Coût initial plus élevé : Par rapport à des blancs standard |
Augmentation de la durée de vie des outils : La résistance supérieure à l'usure réduit les temps d'arrêt et les coûts d'outillage. | Des délais d'exécution plus longs : La fabrication sur mesure nécessite un délai supplémentaire |
Amélioration de la productivité : Des vitesses de coupe et des avances plus élevées augmentent le rendement | Complexité de la conception : Les géométries complexes peuvent poser des problèmes de fabrication |
Réduction des taux de rebut : Des dimensions précises et une qualité constante minimisent les déchets |
Pourquoi choisir des ébauches en carbure cémenté fabriquées sur mesure ?
- Des performances sans compromis : Obtenez des performances et une efficacité optimales de l'outil pour vos défis d'usinage spécifiques.
- Réduction des coûts au fil du temps : L'allongement de la durée de vie des outils et la réduction des temps d'arrêt se traduisent par des économies significatives.
- Amélioration de la qualité des produits : Des dimensions précises et des propriétés matérielles constantes garantissent des produits finis de haute qualité.
- Avantage concurrentiel : Tirez parti de solutions d'outillage de pointe pour rester en tête sur le marché exigeant d'aujourd'hui.
Foire aux questions FAQ d'ébauches en carbure cémenté
1. Quel est le délai de livraison habituel pour les ébauches en carbure fabriquées sur mesure ?
Les délais d'exécution varient en fonction de la complexité de la conception, de la sélection de la qualité et de la capacité de production du fournisseur. En règle générale, les délais sont de 4 à 8 semaines.
2. Les ébauches en carbure cémenté peuvent-elles être revêtues ?
Oui, divers revêtements, tels que le nitrure de titane (TiN), le nitrure de titane et d'aluminium (TiAlN) et le carbone de type diamant (DLC), peuvent être appliqués pour renforcer la résistance à l'usure, réduire la friction et améliorer la durée de vie de l'outil.
3. Quelle est la différence entre les flans pré-filtrés et les flans entièrement frittés ?
Les flans pré-frittés sont partiellement frittés et nécessitent un traitement supplémentaire pour obtenir les dimensions et les propriétés finales. Les flans entièrement frittés sont prêts pour les opérations de rectification et de finition.
4. Comment choisir la bonne nuance de carbure pour mon application ?
Le choix de la nuance appropriée dépend de facteurs tels que le matériau usiné, la vitesse de coupe et l'avance, ainsi que la durée de vie requise de l'outil. Consulter un expert en carbure ou se référer aux catalogues des fournisseurs peut aider à la sélection de la nuance.
5. Quelles sont les principales considérations à prendre en compte lors de la conception d'ébauches en carbure personnalisées ?
Les éléments clés à prendre en compte sont la géométrie souhaitée de l'outil, la préparation de l'arête de coupe, l'évacuation des copeaux et les propriétés mécaniques et thermiques du matériau. Une collaboration étroite entre le client et le fabricant d'ébauches en carbure est essentielle pour une conception et une mise en œuvre réussies.