Lorsqu'il s'agit d'outils de coupe performants et durables, les bandes de carbure sont souvent le matériau de prédilection des fabricants. Que vous travailliez le métal ou le bois, ou que vous ayez besoin d'outils pour d'autres applications industrielles, il est essentiel de comprendre les tenants et les aboutissants des bandes de carbure et de leurs fabricants. Nous allons nous pencher sur ce sujet fascinant et explorer tout ce que vous devez savoir.
Aperçu des bandes de carbure
Les bandes de carbure sont réputées pour leur dureté exceptionnelle, leur résistance à l'usure et leur capacité à conserver une arête vive dans des conditions extrêmes. Généralement utilisées dans les outils de coupe, les applications résistantes à l'usure et divers équipements industriels, ces bandes sont fabriquées à partir d'un matériau composite composé de particules de carbure et d'un liant métallique, généralement du cobalt.
Caractéristiques principales des bandes de carbure :
- Dureté : Leur dureté supérieure les rend idéales pour les applications de coupe et d'usure.
- Résistance à l'usure : Excellente résistance à l'abrasion et à l'usure.
- La robustesse : Capacité à résister aux chocs mécaniques.
- Résistance à la chaleur : Conserve ses propriétés à haute température.
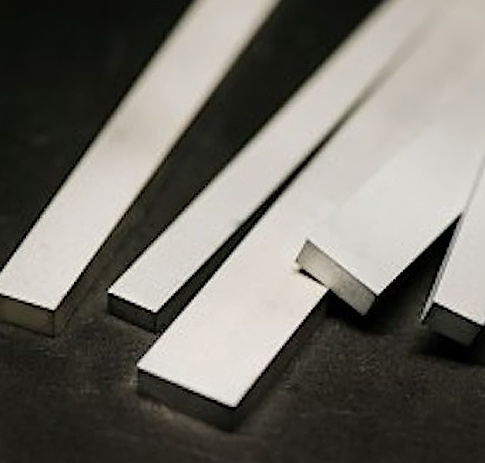
Types de bandes de carbure
Pour vous aider à comprendre les différents types de bandes en carbure disponibles, voici un tableau détaillé résumant les différents modèles :
Modèle | Description |
---|---|
WC-6%Co | Carbure de tungstène avec liant cobalt 6%, dureté élevée et ténacité modérée. |
WC-10%Co | Carbure de tungstène avec cobalt 10%, offrant un équilibre entre ténacité et dureté. |
WC-12%Co | Teneur en cobalt plus élevée pour une meilleure ténacité et une meilleure résistance aux chocs. |
WC-15%Co | Ténacité maximale avec une teneur importante en cobalt, utilisé dans les outils de coupe à usage intensif. |
TiC-WC-Co | Carbure de titane ajouté pour une meilleure résistance à l'usure dans des conditions difficiles. |
CrC-WC-Co | Carbure de chrome ajouté pour une meilleure résistance à la corrosion et à l'usure. |
VC-WC-Co | Le carbure de vanadium est inclus pour améliorer le contrôle de la taille des grains et la dureté. |
WC-8%Co-Ni | Liant cobalt-nickel pour une ténacité et une résistance à la corrosion accrues. |
WC-8%Co-Cr | Liant cobalt-chrome pour une meilleure résistance à l'oxydation. |
WC-8%Co-Ta | Ajout de carbure de tantale pour améliorer la ténacité et la stabilité thermique. |
Applications des bandes de carbure
Les bandes de carbure sont utilisées dans une grande variété d'applications industrielles. Voici un tableau résumant leurs utilisations typiques :
Application | Détails |
---|---|
Découpage du métal | Utilisés dans les outils de tournage, les fraises et les forets pour leurs capacités de coupe supérieures. |
Travail du bois | Idéal pour les lames de scie, les mèches de toupie et les rabots. |
Exploitation minière | Utilisé dans les outils miniers pour le forage et l'excavation. |
La construction | Utilisé dans les outils de coupe pour le béton et la pierre. |
Pièces d'usure | Utilisé dans les environnements à forte usure comme les buses de sablage et les garnitures mécaniques. |
Industrie textile | Lames et cutters pour la fabrication de textiles. |
Papier et pâte à papier | Outils de coupe pour le traitement du papier et de la pâte à papier. |
Plastique et caoutchouc | Lames pour la coupe de matériaux en plastique et en caoutchouc. |
Coupe du verre | Outils pour la découpe de précision du verre. |
Électronique | Outils de coupe de précision pour les composants électroniques. |
Propriétés des matériaux des bandes de carbure
Il est essentiel de comprendre les propriétés des matériaux des bandes de carbure pour choisir le bon type de bande pour votre application. Voici un tableau résumant les principales propriétés des matériaux :
Propriété | Valeur |
---|---|
Dureté | 89 - 94 HRA (dureté Rockwell A) |
Densité | 14,5 - 15,2 g/cm³ |
Résistance à la rupture transversale | 2500 - 3500 MPa |
Module de Young | 500 - 700 GPa |
Conductivité thermique | 50 - 110 W/m-K |
Coefficient de dilatation thermique | 4,5 - 6,5 µm/m-K |
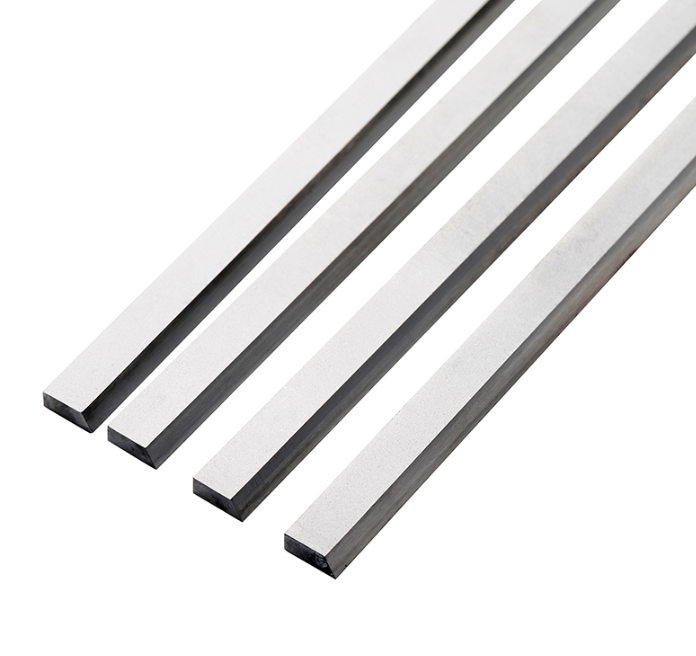
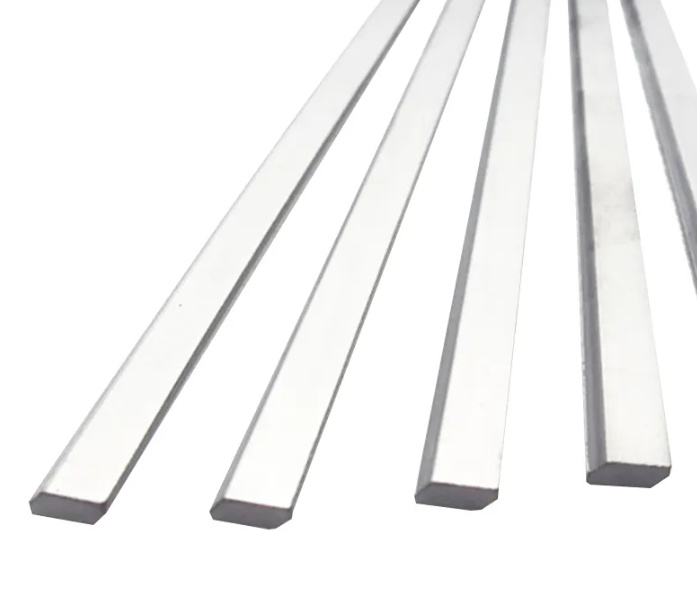
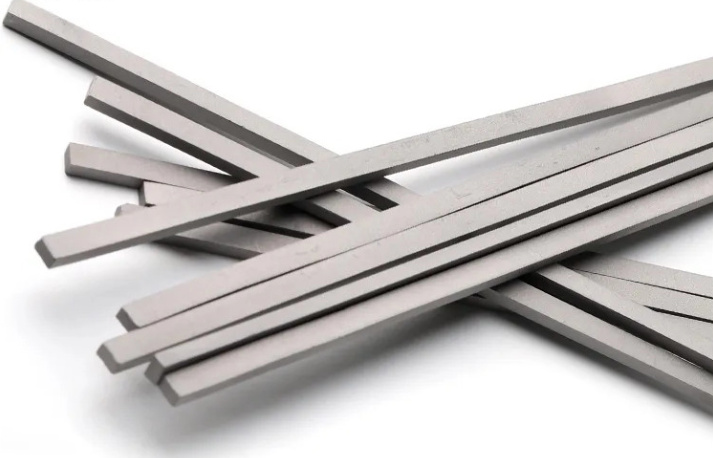
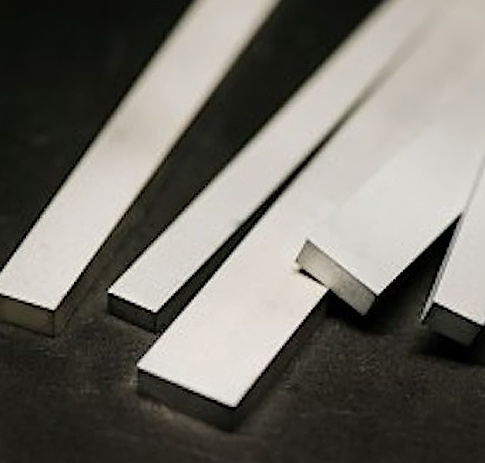
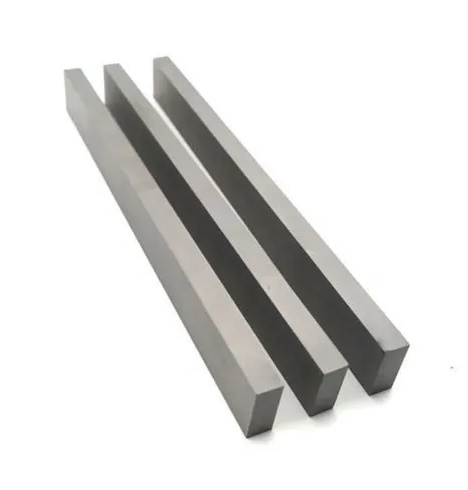
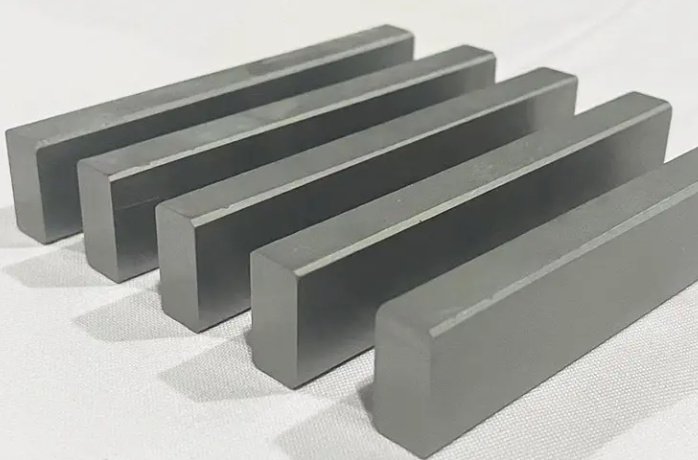
Composition et caractéristiques des bandes de carbure
La composition des bandes de carbure varie en fonction de l'application envisagée. Voici un tableau détaillant leur composition, leurs propriétés et leurs caractéristiques :
Modèle | Composition | Propriétés | Caractéristiques |
---|---|---|---|
WC-6%Co | Carbure de tungstène, 6% Cobalt | Dureté élevée, ténacité moyenne | Des performances équilibrées |
WC-10%Co | Carbure de tungstène, 10% Cobalt | Bonne dureté et ténacité | Utilisation polyvalente |
WC-12%Co | Carbure de tungstène, 12% Cobalt | Ténacité accrue | Convient aux applications sujettes aux chocs |
WC-15%Co | Carbure de tungstène, 15% Cobalt | Ténacité maximale | Outils robustes |
TiC-WC-Co | TiC, carbure de tungstène, cobalt | Résistance accrue à l'usure | Environnements à forte abrasion |
CrC-WC-Co | CrC, carbure de tungstène, cobalt | Résistance supérieure à la corrosion | Conditions corrosives |
VC-WC-Co | VC, carbure de tungstène, cobalt | Amélioration de la taille des grains et de la dureté | Outils de précision |
WC-8%Co-Ni | Carbure de tungstène, 8% Cobalt, Nickel | Ténacité accrue, résistance à la corrosion | Polyvalent, durable |
WC-8%Co-Cr | Carbure de tungstène, 8% Cobalt, Chrome | Résistance accrue à l'oxydation | Applications à haute température |
WC-8%Co-Ta | Carbure de tungstène, 8% Cobalt, Tantale | Amélioration de la stabilité thermique | Environnements à haute température |
Dureté, solidité et résistance à l'usure
Lors du choix des bandes de carbure, la dureté, la solidité et la résistance à l'usure sont des paramètres essentiels. Voici un tableau comparatif de ces propriétés :
Modèle | Dureté (HRA) | Résistance (MPa) | Résistance à l'usure |
---|---|---|---|
WC-6%Co | 92 | 3200 | Haut |
WC-10%Co | 90 | 3000 | Haut |
WC-12%Co | 88 | 2900 | Modéré |
WC-15%Co | 86 | 2800 | Modéré |
TiC-WC-Co | 93 | 3100 | Très élevé |
CrC-WC-Co | 91 | 3000 | Haut |
VC-WC-Co | 92 | 3200 | Haut |
WC-8%Co-Ni | 90 | 3100 | Haut |
WC-8%Co-Cr | 90 | 3100 | Haut |
WC-8%Co-Ta | 91 | 3150 | Haut |
Spécifications, tailles et normes
Les bandes de carbure sont disponibles en différentes tailles et répondent à certaines normes. Voici un tableau détaillé des spécifications :
Spécifications | Détails |
---|---|
Tailles standard | Longueur : 100-300 mm, largeur : 10-30 mm, épaisseur : 1-10 mm |
Forme | Rectangulaire, Carré, Formes personnalisées |
Tolérance | ±0,05 mm pour la longueur, ±0,02 mm pour la largeur et l'épaisseur |
Normes | ISO 9001, ASTM B777, DIN ISO 3313 |
Fournisseurs et détails des prix
Le choix d'un fournisseur fiable est essentiel pour garantir la qualité et la performance. Voici un tableau récapitulatif des principaux fournisseurs et de leurs tarifs :
Fournisseur | Localisation | Prix (USD par kg) | Caractéristiques spéciales |
---|---|---|---|
Kennametal | ÉTATS-UNIS | 50 – 100 | Des solutions personnalisées de haute qualité |
Sandvik | Suède | 45 – 95 | Large gamme, excellente durabilité |
Ceratizit | Luxembourg | 40 – 90 | Des produits innovants, une grande performance |
Carbure cémenté de Zhuzhou | Chine | 30 – 70 | Rentable et fiable |
Matériaux Hyperion | ÉTATS-UNIS | 50 – 110 | Haute précision, dimensions sur mesure |
Comment choisir le bon fabricant de bandes de carbure
Le choix du bon fabricant peut faire une différence significative dans la performance et la durée de vie de vos bandes de carbure. Voici un guide pour vous aider à prendre une décision éclairée :
Critères | Considérations |
Réputation | Recherchez des fabricants jouissant d'une solide réputation et d'avis positifs. |
Normes de qualité | Veillez à ce qu'ils respectent les normes de qualité internationales telles que la norme ISO 9001. |
Personnalisation | Vérifiez s'ils proposent des options de personnalisation pour des besoins spécifiques. |
Support technique | Optez pour des fournisseurs qui offrent une assistance technique et un service après-vente solides. |
Tarification | Comparez les prix pour vous assurer d'obtenir le meilleur rapport qualité-prix sans compromettre la qualité. |
Délai d'exécution | Tenez compte du délai de livraison du fabricant. |
Expérience | Les fabricants ayant une grande expérience dans le secteur sont souvent plus fiables. |
Comparaison des avantages et des limites des bandes de carbure
Pour vous aider à comprendre les avantages et les inconvénients, voici un tableau comparatif :
Aspect | Avantages | Limites |
---|---|---|
Dureté | Très dur, maintient la netteté | Peut être fragile en cas d'impact important |
Résistance à l'usure | Résistance exceptionnelle à l'usure | Coût initial plus élevé |
Résistance à la chaleur | Bonne performance à des températures élevées | Nécessite des techniques de fabrication précises |
Polyvalence | Convient à une large gamme d'applications | Peut nécessiter une manipulation et une utilisation spécifiques |
Coût | Rentabilité à long terme | Investissement initial plus élevé |
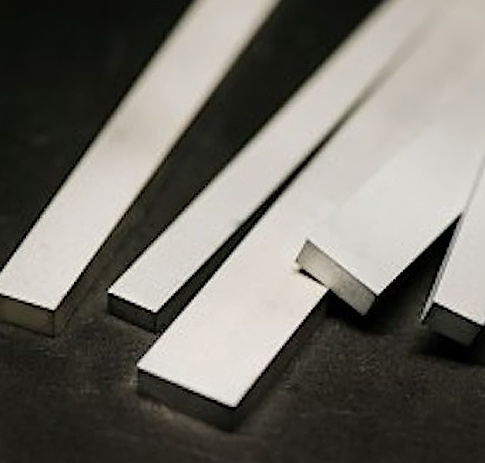
FAQ
De quoi sont faites les bandes de carbure ?
Les bandes de carbure sont constituées de particules de carbure de tungstène liées par un liant métallique, généralement du cobalt.
Quels sont les principaux avantages de l'utilisation des bandes en carbure ?
Les principaux avantages sont une dureté, une résistance à l'usure, une ténacité et une résistance à la chaleur supérieures, ce qui les rend idéales pour les applications de coupe et d'usure.
Comment les bandes de carbure sont-elles utilisées dans les différentes industries ?
Ils sont utilisés pour la coupe des métaux, le travail du bois, l'exploitation minière, la construction et diverses autres industries qui nécessitent des outils de coupe durables et résistants à l'usure.
Quels sont les éléments à prendre en compte lors de la sélection d'un fabricant de bandes en carbure ?
Tenez compte de la réputation du fabricant, de ses normes de qualité, de ses options de personnalisation, de son assistance technique, de ses prix, de ses délais d'exécution et de son expérience dans le secteur.
Les bandes de carbure peuvent-elles être personnalisées ?
Oui, de nombreux fabricants proposent des options de personnalisation pour répondre aux besoins d'applications spécifiques, y compris des formes et des tailles sur mesure.
Conclusion
Choisir les bonnes bandes de carbure et un fabricant fiable est crucial pour assurer le succès et l'efficacité de vos applications industrielles. Grâce aux informations détaillées fournies dans ce guide, vous êtes bien équipé pour prendre des décisions éclairées qui amélioreront vos opérations. Que vous ayez besoin de bandes de carbure pour la coupe, la résistance à l'usure ou des applications industrielles spécialisées, la compréhension des types, des propriétés et des facteurs de sélection d'un fabricant vous aidera à obtenir les meilleurs résultats.