Vue d'ensemble
Bandes de carbure are essential components in various industrial applications due to their exceptional hardness, strength, and wear resistance. These strips, made from tungsten carbide, are commonly used in manufacturing processes, particularly in tools and machinery where high durability and performance are crucial. This comprehensive guide explores the intricacies of carbide strips, including their types, applications, properties, and how to select the right ones for your needs.
Types de bandes de carbure
Type | Description |
---|---|
Bandes de carbure standard | Commonly used in woodworking and metal cutting. Known for general-purpose applications. |
Micro-grain Carbide Strips | Have finer grain size, offering higher strength and better finish. Ideal for precision machining. |
Sub-micro Grain Carbide Strips | Provide even higher hardness and wear resistance, used in demanding applications. |
Nano-grain Carbide Strips | Feature the smallest grain size for the highest hardness and toughness. Suitable for high-precision tools. |
Cemented Carbide Strips | Combined with a metallic binder like cobalt, enhancing toughness and strength. |
Bandes de carbure de titane | Offer better oxidation resistance, used in high-temperature environments. |
Bandes de carbure de tantale | Known for excellent thermal shock resistance, suitable for extreme conditions. |
Bandes de carbure de chrome | High resistance to corrosion and wear, used in harsh chemical environments. |
Bandes de carbure de vanadium | Exceptional wear resistance, commonly used in cutting tools. |
Mixed Carbide Strips | Combination of various carbide powders to achieve specific properties for specialized applications. |
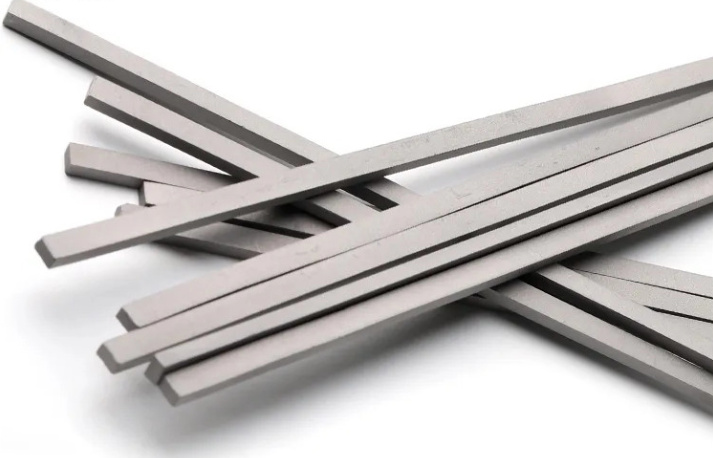
Applications de la Bandes de carbure
Application | Description |
---|---|
Outils pour le travail du bois | Carbide strips are used in saw blades, planer knives, and other woodworking tools for their durability and sharpness. |
Outils de coupe des métaux | Employed in lathe tools, milling cutters, and drill bits for precise and efficient metal cutting. |
Outils d'exploitation minière | Essential in the mining industry for drills and cutters due to their hardness and wear resistance. |
Outils de construction | Used in construction equipment for cutting and grinding, ensuring longevity and performance. |
Machines industrielles | Integral in various machinery components that require high strength and resistance to wear. |
Industrie aérospatiale | Utilized in components that endure extreme conditions, providing reliability and performance. |
Industrie automobile | Applied in engine parts and cutting tools, ensuring efficiency and durability. |
Traitement chimique | Used in equipment exposed to corrosive chemicals, offering excellent resistance. |
Dispositifs médicaux | Incorporated in surgical instruments and other devices for their precision and reliability. |
Defense Industry | Employed in military applications where high-performance materials are crucial. |
Propriétés des matériaux des bandes de carbure
Propriété | Description |
---|---|
Dureté | Measured in Rockwell or Vickers, indicating the material’s resistance to deformation. |
Solidité | The ability to absorb energy and resist fracture. |
Résistance à l'usure | The ability to resist abrasion and erosion. |
Résistance à la compression | La capacité à supporter des charges tendant à réduire la taille. |
Conductivité thermique | The ability to conduct heat. |
Coefficient de dilatation thermique | The rate at which the material expands with temperature. |
Densité | The mass per unit volume, affecting strength and performance. |
Module d'élasticité | A measure of the material’s stiffness. |
Résistance à la rupture | The ability to resist crack propagation. |
Résistance à l'oxydation | The ability to resist oxidation at high temperatures. |
Composition et caractéristiques
Composition | Propriétés | Caractéristiques |
---|---|---|
WC-Co (carbure de tungstène-cobalt) | Dureté élevée, bonne ténacité | Commonly used, versatile, reliable |
WC-TiC (Tungsten Carbide-Titanium Carbide) | Enhanced wear resistance, good oxidation resistance | Convient aux applications à haute température |
WC-TaC (Tungsten Carbide-Tantalum Carbide) | Excellent thermal shock resistance, high hardness | Ideal for extreme conditions |
WC-Cr3C2 (Tungsten Carbide-Chromium Carbide) | Superior corrosion and wear resistance | Used in harsh chemical environments |
WC-VC (Tungsten Carbide-Vanadium Carbide) | Exceptional wear resistance, good toughness | Commonly used in cutting tools |
WC-Co/Ni (Tungsten Carbide-Cobalt/Nickel) | High strength, good corrosion resistance | Used in diverse applications |
WC-Co-Cr (carbure de tungstène-cobalt-chrome) | Enhanced toughness, good wear resistance | Suitable for demanding applications |
WC-Co-V (Carbure de tungstène-Cobalt-Vanadium) | High hardness, improved wear resistance | Ideal for cutting and machining |
WC-Co-Nb (Tungsten Carbide-Cobalt-Niobium) | Good thermal stability, high hardness | Used in specialized applications |
WC-TiC-TaC (Tungsten Carbide-Titanium Carbide-Tantalum Carbide) | Combined properties for high performance | Suitable for complex and demanding tasks |
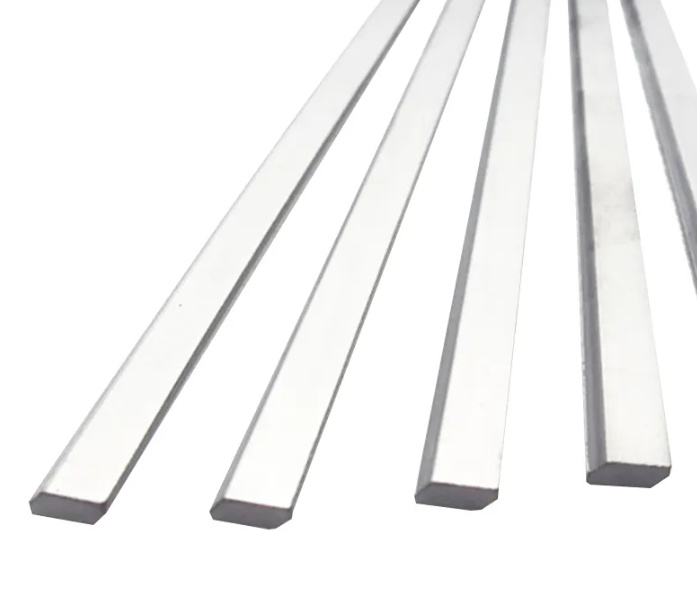
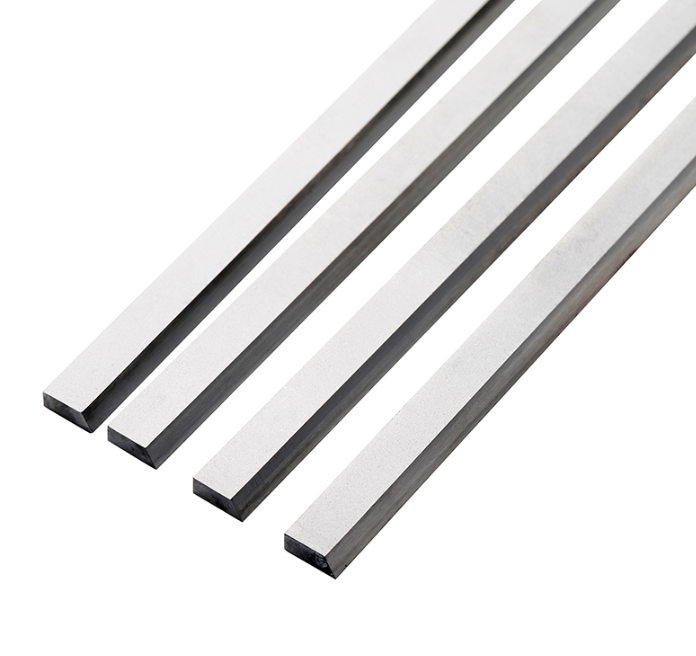
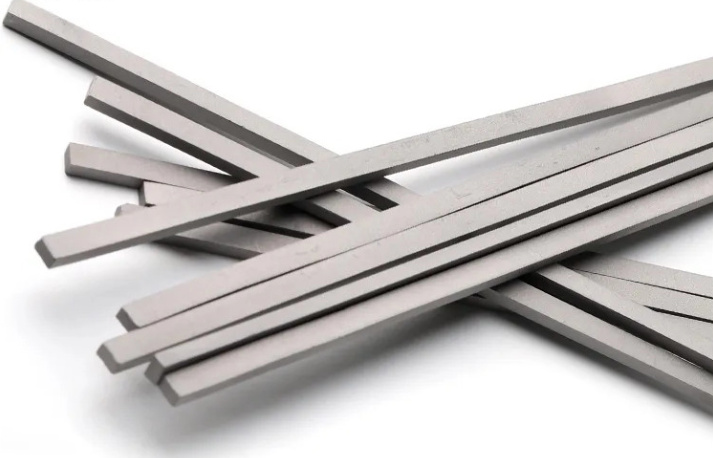
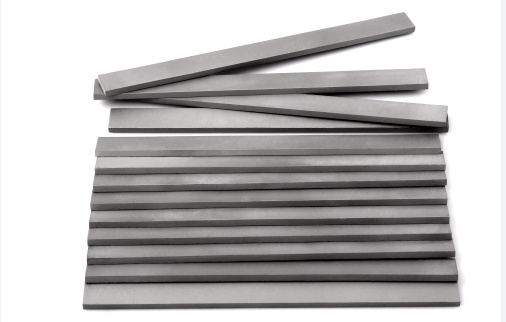
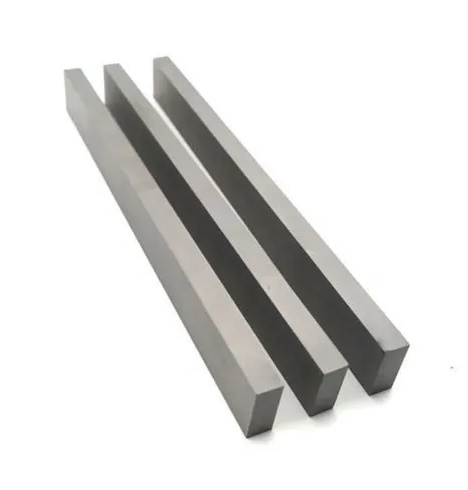
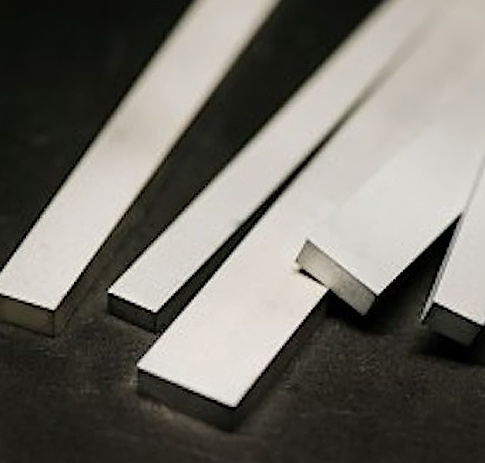
Dureté, solidité et résistance à l'usure
Type | Dureté (HRA) | Résistance (MPa) | Résistance à l'usure |
---|---|---|---|
Bandes de carbure standard | 89-93 | 1500-2000 | Haut |
Micro-grain Carbide Strips | 90-94 | 1800-2500 | Très élevé |
Sub-micro Grain Carbide Strips | 91-95 | 2000-2700 | Extrêmement élevé |
Nano-grain Carbide Strips | 92-96 | 2200-2900 | Maximum |
Cemented Carbide Strips | 88-92 | 1400-1900 | Haut |
Bandes de carbure de titane | 89-93 | 1500-2000 | Très élevé |
Bandes de carbure de tantale | 90-94 | 1600-2100 | Extrêmement élevé |
Bandes de carbure de chrome | 89-92 | 1400-1800 | Haut |
Bandes de carbure de vanadium | 91-94 | 1800-2300 | Très élevé |
Mixed Carbide Strips | 90-95 | 1700-2400 | Variable |
Spécifications, tailles, formes, normes
Spécifications | Détails |
---|---|
Tailles | Available in a range of lengths, widths, and thicknesses to suit various applications. |
Formes | Typically rectangular, but custom shapes can be produced to meet specific requirements. |
Normes | Manufactured according to ISO, ASTM, and other relevant industry standards. |
Tolérance | Precision tolerances can be achieved to ensure the exact fit and performance. |
Finition de la surface | Available in polished or ground finishes to meet specific needs. |
Spécifications personnalisées | Tailored solutions can be developed for unique applications. |
Fournisseurs et détails des prix
Fournisseur | Localisation | Tarification | Notes |
---|---|---|---|
Kennametal | ÉTATS-UNIS | $$ – $$$ | Known for high-quality carbide products. |
Sandvik | Suède | $$ – $$$ | Offers a wide range of carbide materials. |
CERATIZIT | Luxembourg | $$ – $$$ | Renowned for innovative carbide solutions. |
Sumitomo Electric | Japon | $$ – $$$ | Provides high-performance carbide strips. |
Guhring | Allemagne | $$ – $$$ | Specializes in precision carbide tools. |
ISCAR | Israël | $$ – $$$ | Leading manufacturer of carbide cutting tools. |
Tungaloy | Japon | $$ – $$$ | Offers durable and reliable carbide products. |
Matériaux Mitsubishi | Japon | $$ – $$$ | High-quality carbide strips for various industries. |
YG-1 | Corée du Sud | $$ – $$$ | Competitive pricing and quality products. |
KORLOY | Corée du Sud | $$ – $$$ | Known for innovation and quality in carbide materials. |
Choisir le bon Bandes de carbure
Critères | Considérations |
---|---|
Application | Determine the specific application to choose the appropriate type and properties. |
Composition du matériau | Select the composition that offers the best performance for your needs. |
Dureté et résistance | Balance between hardness and toughness based on the working conditions. |
Résistance à l'usure | Higher wear resistance for abrasive environments. |
Propriétés thermiques | Consider thermal conductivity and coefficient of thermal expansion for high-temperature applications. |
Taille et forme | Ensure the correct size and shape for fitting and performance. |
Réputation du fournisseur | Choose a reputable supplier for quality assurance. |
Coût | Balance between cost and performance, considering long-term benefits. |
Exigences personnalisées | Evaluate if custom specifications are necessary for unique applications. |
Respect des normes | Ensure compliance with industry standards for reliability and performance. |
Advantages and Limitations of Carbide Strips
Aspect | Avantages | Limites |
---|---|---|
Dureté | Exceptional hardness for long-lasting performance. | Peut être cassant en cas de contraintes extrêmes. |
Résistance à l'usure | High resistance to wear and abrasion. | May require more frequent sharpening. |
La force | Strong and durable, suitable for tough applications. | Can be more expensive than other materials. |
Stabilité thermique | Conserve ses propriétés à haute température. | Some types may have lower toughness. |
Polyvalence | Wide range of applications across industries. | Requires precise handling and machining. |
Personnalisation | Can be tailored to specific needs. | Custom options may increase lead time and cost. |
Fiabilité | Consistent performance and quality. | Not always the best choice for low-stress applications. |
Longévité | Long service life reduces replacement frequency. | Initial investment can be higher. |
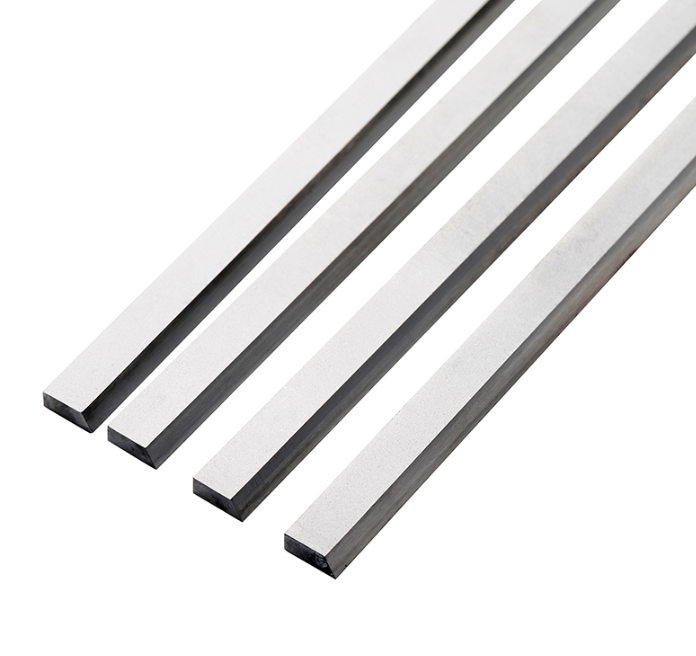
FAQ
Question | Réponse |
---|---|
À quoi servent les bandes de carbure ? | Carbide strips are used in various industrial applications, including cutting tools, mining equipment, construction machinery, and more, due to their hardness and wear resistance. |
Comment les bandes de carbure sont-elles fabriquées ? | They are made by combining tungsten carbide powder with a metallic binder, such as cobalt, and then pressing and sintering the mixture to form a solid strip. |
What is the difference between standard and micro-grain carbide strips? | Standard carbide strips have larger grain sizes and are used for general purposes, while micro-grain carbide strips have finer grains, offering higher strength and better finishes for precision machining. |
Les bandes de carbure peuvent-elles être personnalisées ? | Yes, carbide strips can be customized in terms of size, shape, composition, and properties to meet specific application requirements. |
What factors should be considered when selecting carbide strips? | Consider the application, material composition, hardness, toughness, wear resistance, thermal properties, size, shape, and supplier reputation. |
How do carbide strips compare to other materials? | Carbide strips offer superior hardness, wear resistance, and thermal stability compared to many other materials, making them ideal for demanding applications. |
Are carbide strips cost-effective? | While the initial cost may be higher, their durability and long service life make them cost-effective in the long run. |
Quelles sont les industries qui utilisent les bandes de carbure ? | Industries such as woodworking, metalworking, mining, construction, aerospace, automotive, chemical processing, medical, and defense use carbide strips. |
How are carbide strips maintained? | Regular inspection, proper handling, and timely sharpening are essential for maintaining the performance and longevity of carbide strips. |
Où puis-je acheter des bandes de carbure ? | Carbide strips can be purchased from reputable suppliers like Kennametal, Sandvik, CERATIZIT, Sumitomo Electric, Guhring, ISCAR, Tungaloy, Mitsubishi Materials, YG-1, and KORLOY. |
Conclusion
Bandes de carbure are invaluable in numerous industrial applications due to their remarkable properties, including hardness, wear resistance, and thermal stability. Understanding the different types, applications, and material properties can help you select the right carbide strips for your needs, ensuring optimal performance and longevity. Whether you’re in woodworking, metalworking, or any other industry, investing in high-quality carbide strips can significantly enhance your operations. Choose wisely, and you’ll reap the benefits of this versatile and durable material.