Introduction
Carbure saw tips are the unsung heroes of the cutting world, enhancing tool performance and longevity in countless applications. But did you know that not all carbide saw tips are created equal? The grade of a carbide saw tip determines its properties and suitability for specific tasks. In this comprehensive guide, we’ll delve into the fascinating world of carbide saw tip grades, exploring how different grades impact performance and how to choose the right one for your needs.
Understanding Carbide Saw Tip Grades
What Are Carbide Saw Tip Grades?
Carbide saw tip grades refer to the classification of carbide tips based on their composition, grain size, and performance characteristics. These grades dictate the tip’s hardness, toughness, wear resistance, and overall suitability for various cutting applications.
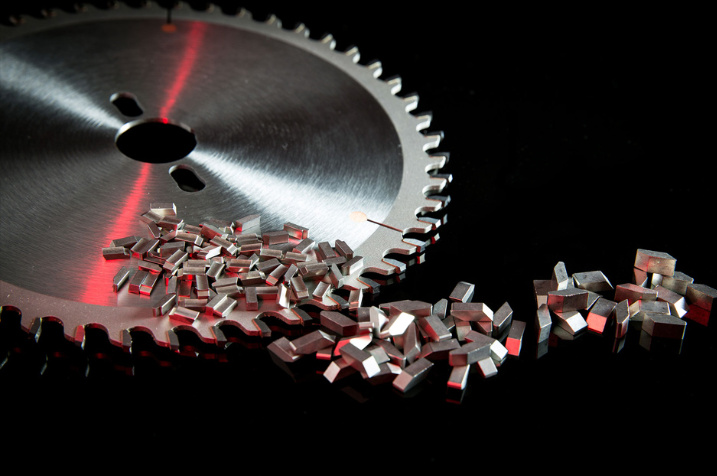
Composition of Carbide Saw Tips
Carbide saw tips are primarily composed of tungsten carbide (WC) particles bonded with a metal binder, typically cobalt (Co). The ratio of tungsten carbide to cobalt and the grain size of the carbide particles are key factors that determine the grade of the saw tip.
Importance of Choosing the Right Grade
Selecting the appropriate carbide saw tip grade is crucial for optimizing tool performance and longevity. The right grade ensures efficient cutting, reduced wear and tear, and minimized downtime. Conversely, using an unsuitable grade can lead to poor performance, frequent tool replacements, and increased costs.
Detailed Classification of Carbide Saw Tip Grades
Carbide saw tip grades are generally classified into three main categories based on their grain size: micro-grain, medium-grain, and coarse-grain. Each category offers unique properties suited for different applications.
Micro-Grain Carbide Saw Tips
Micro-grain carbide saw tips are composed of extremely fine tungsten carbide particles, typically less than 1 micron in size. These tips are renowned for their exceptional sharpness and precision. They are ideal for applications requiring highly accurate cuts, such as woodworking and fine metalworking.
Medium-Grain Carbide Saw Tips
Medium-grain carbide saw tips have a grain size ranging from 1 to 2 microns. These tips offer a balanced combination of hardness and toughness, making them versatile for a wide range of cutting tasks. They are commonly used in general-purpose saw blades for wood, metal, and plastic cutting.
Coarse-Grain Carbide Saw Tips
Coarse-grain carbide saw tips are composed of larger tungsten carbide particles, typically greater than 2 microns. These tips prioritize toughness and impact resistance over sharpness. They are suitable for heavy-duty applications, such as cutting hard metals and abrasive materials.
Properties and Applications of Different Grades
The following table provides a detailed comparison of the properties and applications of different carbide saw tip grades.
Grade | Taille des grains | Dureté | Solidité | Résistance à l'usure | Applications idéales |
---|---|---|---|---|---|
Micro-grain | < 1 micron | Extrêmement élevé | Modéré | Très élevé | Fine woodworking, fine metalworking, precision cuts |
Medium-Grain | 1-2 microns | Haut | Haut | Haut | General woodworking, metal cutting, plastic cutting |
Coarse-Grain | > 2 microns | Modéré | Très élevé | Modéré | Heavy-duty metal cutting, abrasive materials |
Description du contenu du tableau
This table highlights the key properties of different carbide saw tip grades, including grain size, hardness, toughness, and wear resistance. It also outlines the ideal applications for each grade, helping users make informed decisions based on their specific cutting needs.
Factors Influencing Carbide Saw Tip Grades
Several factors influence the grading of carbide saw tips, including:
1. Composition
The ratio of tungsten carbide to cobalt significantly impacts the grade. Higher tungsten carbide content generally increases hardness, while higher cobalt content enhances toughness.
2. Taille des grains
The size of the tungsten carbide particles plays a crucial role in determining the grade. Finer grains result in higher hardness and precision, while coarser grains provide greater toughness and impact resistance.
3. Manufacturing Process
The methods used in the production of carbide saw tips, such as pressing, sintering, and grinding, also affect the final grade. Precision manufacturing techniques ensure consistent quality and performance.
4. Coating
Advanced coatings, such as titanium nitride (TiN) or diamond coatings, can enhance the properties of carbide saw tips, improving their wear resistance and extending their lifespan.
Choosing the Right Carbide Saw Tip Grade
Selecting the appropriate carbide saw tip grade involves considering several factors:
1. Material Being Cut
Different materials require different grades of carbide saw tips. For example, fine woodworking requires micro-grain tips, while heavy-duty metal cutting benefits from coarse-grain tips.
2. Cutting Conditions
The cutting speed, feed rate, and temperature conditions also influence the choice of grade. High-speed cutting may require tips with enhanced thermal stability.
3. Desired Finish
The finish quality of the cut is another important factor. Precision cuts with smooth finishes are best achieved with micro-grain tips.
4. Tool Longevity
For applications requiring extended tool life, selecting a grade with high wear resistance is essential. Coated tips can provide additional durability.
Market Trends and Innovations
The market for carbide saw tips is continually evolving, driven by technological advancements and changing industry demands. Key trends include:
1. Advanced Coatings
Innovations in coating technologies, such as nano-coatings and PVD (Physical Vapor Deposition) coatings, are enhancing the performance and longevity of carbide saw tips.
2. Sustainable Practices
Manufacturers are increasingly adopting sustainable practices, such as recycling carbide materials and reducing waste in the production process.
3. Customization
Customized carbide saw tips tailored to specific applications and cutting conditions are becoming more prevalent, offering users optimized performance for their unique needs.
4. Integration with Smart Technologies
The integration of smart technologies, such as IoT-enabled tools and AI-driven maintenance systems, is revolutionizing the use of carbide saw tips. These innovations enable real-time monitoring, predictive maintenance, and enhanced performance optimization.
FAQ
Q1: What are the key differences between micro-grain, medium-grain, and coarse-grain carbide saw tips?
A1 : Micro-grain tips offer exceptional sharpness and precision, ideal for fine woodworking and metalworking. Medium-grain tips provide a balance of hardness and toughness, suitable for general-purpose cutting. Coarse-grain tips prioritize toughness and impact resistance, making them perfect for heavy-duty applications.
Q2: How does the composition of carbide saw tips affect their performance?
A2 : The composition, particularly the ratio of tungsten carbide to cobalt, influences the tip’s hardness and toughness. Higher tungsten carbide content increases hardness, while higher cobalt content enhances toughness, impacting the tip’s suitability for different cutting tasks.
Q3: Can advanced coatings improve the performance of carbide saw tips?
A3 : Yes, advanced coatings such as titanium nitride (TiN) or diamond coatings can significantly enhance the wear resistance, hardness, and overall performance of carbide saw tips, extending their lifespan and improving cutting efficiency.
Q4: What factors should be considered when choosing a carbide saw tip grade?
A4 : Key factors include the material being cut, cutting conditions (such as speed and temperature), desired finish quality, and tool longevity requirements. Selecting the right grade ensures optimal performance and durability for specific applications.
Q5: What are some current trends in the carbide saw tip market?
A5 : Current trends include advancements in coating technologies, sustainable manufacturing practices, increased customization of carbide tips, and the integration of smart technologies for real-time monitoring and predictive maintenance.
Vous souhaitez acheter des pointes de scie en carbure à un prix avantageux ? Cliquez ici ici.