Vue d'ensemble
Fabrication OEM carbide rods involves a complex process that transforms high-quality metal powders into durable and precise rods used in various industries. This comprehensive guide covers everything you need to know about OEM carbide rods, including types, applications, material properties, and selecting the right rods for your needs. By diving into the specifics of each aspect, we ensure a detailed understanding of what makes these rods essential in modern manufacturing.
Types of OEM Carbide Rods
Different OEM carbide rods cater to varying applications. Let’s explore some specific metal powder models and their unique characteristics.
Type de tige en carbure | Description |
---|---|
H10F | Known for high toughness and good wear resistance. Suitable for machining steel. |
K40 | High wear resistance, ideal for cast iron and non-ferrous metals. |
WC-10Co | Tungsten carbide with 10% cobalt. Offers excellent hardness and strength. |
WC-6Ni | Tungsten carbide with 6% nickel. Provides good corrosion resistance. |
P40 | Versatile, with balanced hardness and toughness. Suitable for general machining. |
C2 | Fine grain structure, excellent for precision tools. |
T30 | High thermal stability, used in high-speed cutting applications. |
N10 | Designed for non-ferrous materials, great wear resistance. |
K30 | Good balance of hardness and toughness, ideal for interrupted cuts. |
H13 | High toughness, used in heavy-duty applications. |
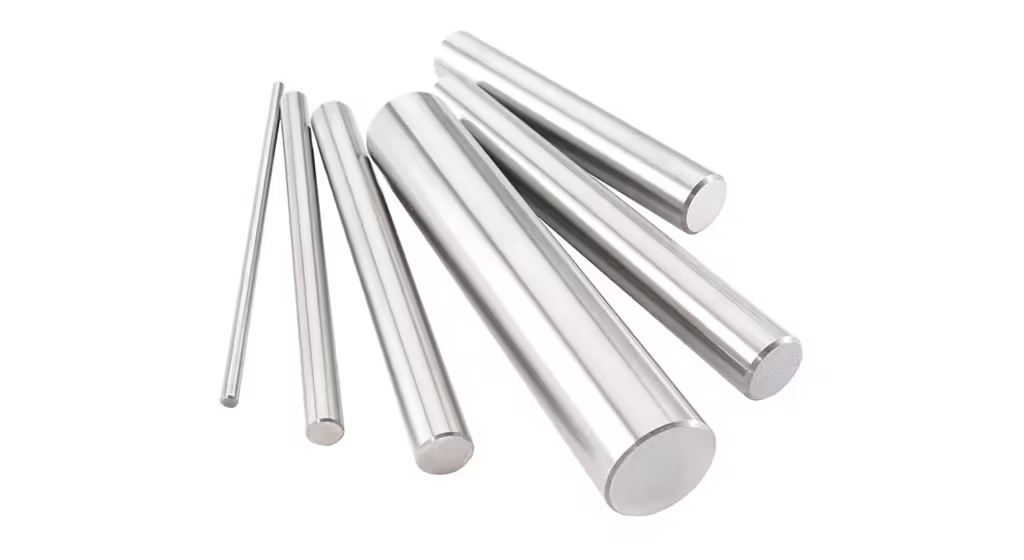
Applications of OEM Carbide Rods
OEM carbide rods are integral to various industrial applications due to their durability and precision. Here’s how they’re utilized across different sectors.
Application | Description |
---|---|
Outils de coupe | Used in end mills, drills, and reamers for machining metals. |
Outils d'exploitation minière | Employed in rock drilling and cutting tools due to their high wear resistance. |
Industrie automobile | Components for engines and transmissions. |
Aérospatiale | Precision parts for aircraft and spacecraft manufacturing. |
Travail du bois | Tools for cutting, shaping, and forming wood materials. |
Dispositifs médicaux | Instruments chirurgicaux et outils dentaires. |
La construction | Components in heavy machinery and tools. |
Électronique | Precision tools for circuit board manufacturing. |
Fabrication de bijoux | Used in dies and molds for shaping metals and gemstones. |
Pétrole et gaz | Drilling and exploration tools. |
Propriétés des matériaux
The material properties of OEM tiges en carbure are crucial for their performance. Here’s a detailed look at their composition, properties, and characteristics.
Propriété | Description |
---|---|
Dureté | Measured in HRA, typically ranges from 85 to 94. |
Solidité | High fracture toughness, essential for resisting breakage. |
Résistance à l'usure | Exceptional, ensures long tool life. |
Conductivité thermique | Efficient heat dissipation. |
Résistance à la corrosion | Varies with binder metals like cobalt or nickel. |
Densité | High density, around 14-15 g/cm³. |
Résistance à la compression | High, capable of withstanding heavy loads. |
Stabilité thermique | Maintient les performances à des températures élevées. |
Composition et caractéristiques
The unique composition of OEM carbide rods defines their performance attributes.
Composition | Caractéristiques |
---|---|
Carbure de tungstène (WC) | Dureté et résistance à l'usure extrêmes. |
Cobalt (Co) | Adds toughness and impact resistance. |
Nickel (Ni) | Améliore la résistance à la corrosion. |
Carbure de titane (TiC) | Améliore la résistance à l'usure et la ténacité. |
Carbure de tantale (TaC) | Increases hardness and thermal stability. |
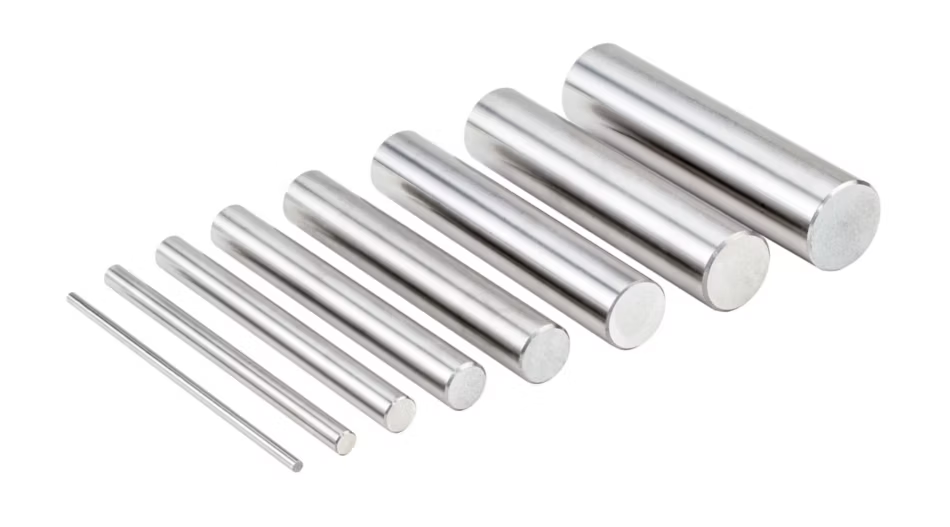
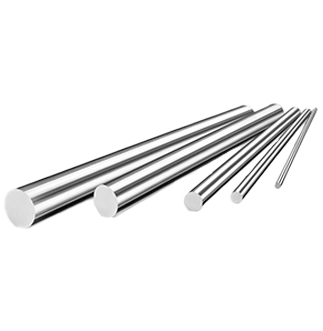
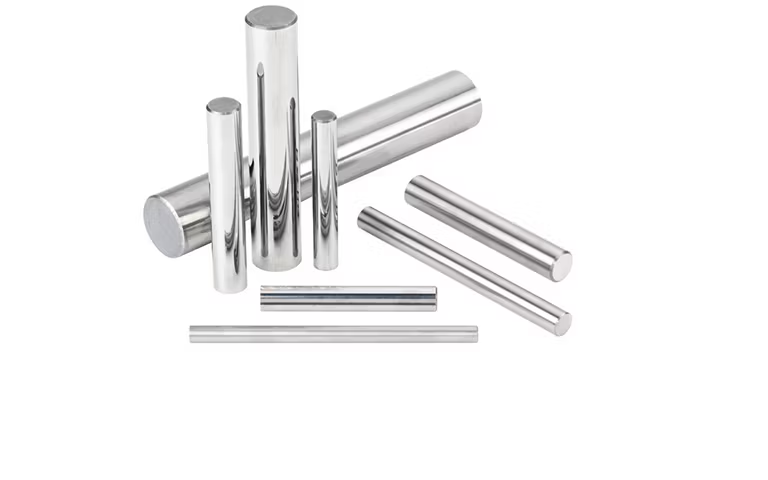
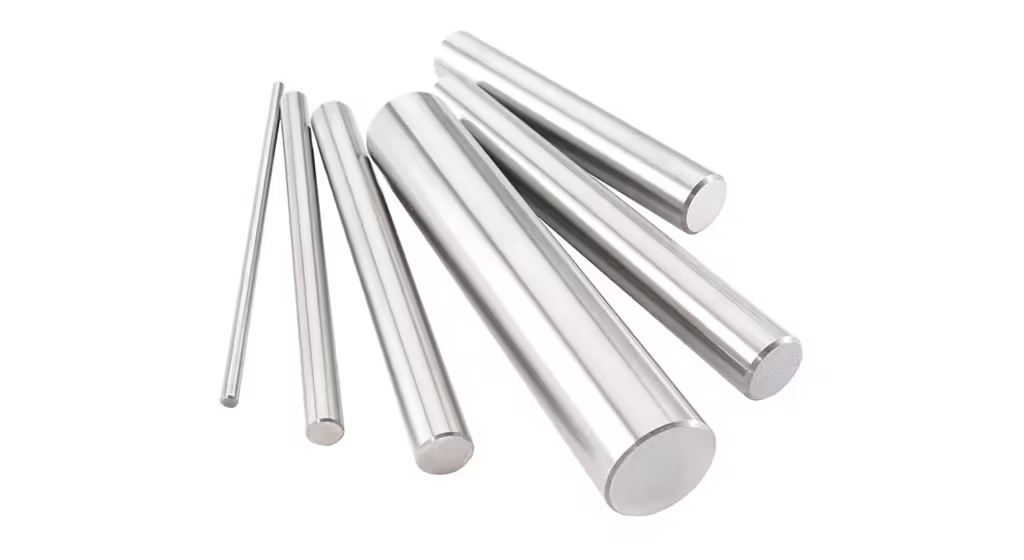
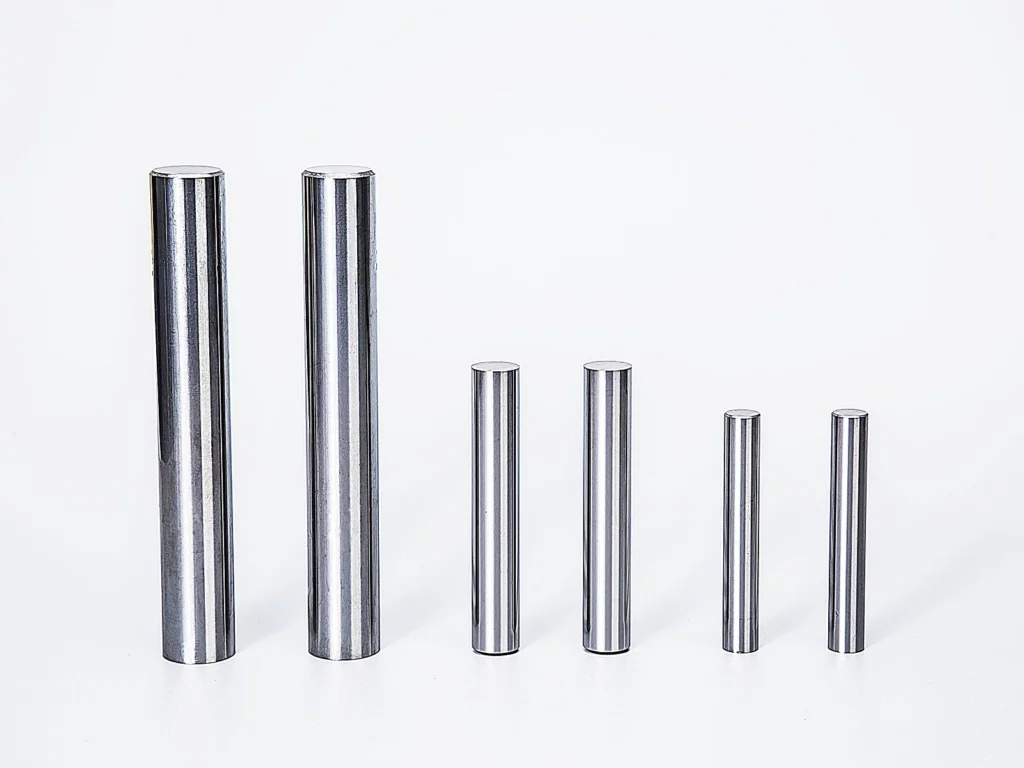
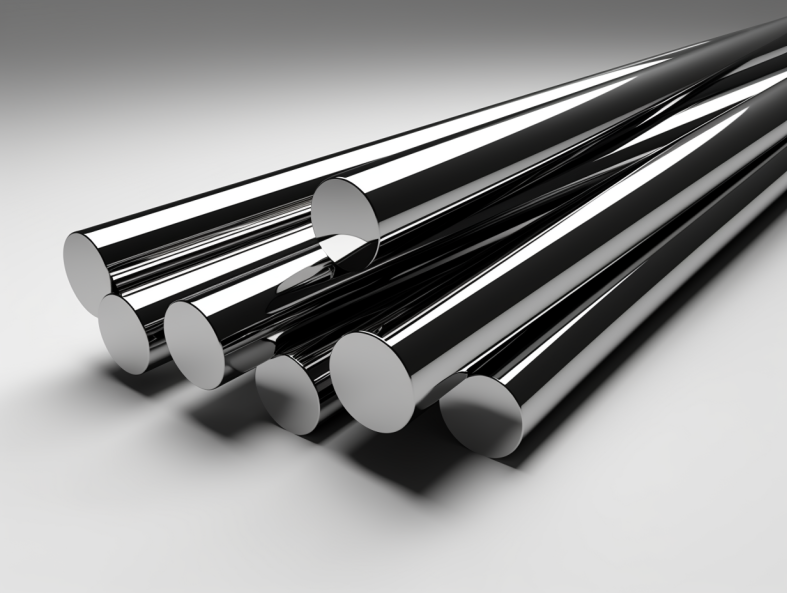
Dureté, solidité et résistance à l'usure
Understanding the mechanical properties of OEM carbide rods helps in selecting the right type for specific applications.
Métrique | Range/Value |
---|---|
Dureté (HRA) | 85-94 |
Résistance à la compression (MPa) | 3000-4500 |
Résistance à l'usure | Excellent, varies by type and application. |
Spécifications, tailles, formes et normes
Carbide rods come in various sizes and shapes, adhering to industry standards.
Spécifications | Détails |
---|---|
Gamme de diamètres | 1mm à 50mm |
Longueur Plage | 50mm à 330mm |
Formes | Ronde, carrée, rectangulaire |
Normes | ISO, ANSI, DIN |
Fournisseurs et détails des prix
Choosing the right supplier ensures quality and cost-effectiveness. Here are some reputable suppliers and typical pricing details.
Fournisseur | Région | Prix (par kg) |
---|---|---|
Carbure XYZ | ÉTATS-UNIS | $50 – $70 |
Outils ABC | Chine | $40 – $60 |
Global Carbide | L'Europe | $55 – $75 |
Métaux de précision | Inde | $45 – $65 |
Selecting the Right OEM Tiges en carbure
Choosing the appropriate carbide rod involves considering several factors, including the application, material properties, and cost.
Considération | Détails |
---|---|
Application | Match the rod type to the specific use case. |
Propriétés des matériaux | Ensure the rod has the necessary hardness and toughness. |
Coût | Balance quality with budget constraints. |
Fiabilité des fournisseurs | Choose reputable suppliers with consistent quality. |
Advantages and Limitations of OEM Carbide Rods
Understanding the pros and cons of different carbide rods helps in making an informed decision.
Type | Avantages | Limites |
---|---|---|
H10F | Ténacité élevée, bonne résistance à l'usure | Limited corrosion resistance |
K40 | Excellente résistance à l'usure | Not ideal for high-impact applications |
WC-10Co | Superb hardness and strength | Coûteux |
WC-6Ni | Bonne résistance à la corrosion | Lower hardness than WC-10Co |
How to Choose OEM Carbide Rods
Selecting the right OEM carbide rods can be challenging. Here are some tips to help you make the best choice.
- Identify Your Needs: Determine the specific requirements of your application.
- Evaluate Material Properties: Consider the hardness, toughness, and wear resistance required.
- Compare Suppliers: Look for reliable suppliers with good reviews.
- Check Standards: Ensure the rods meet industry standards like ISO or ANSI.
- Consider Cost: Balance the quality and performance with your budget.
Function of OEM Carbide Rods
OEM carbide rods play a crucial role in various manufacturing processes due to their durability and precision.
- Cutting Efficiency: Their hardness ensures efficient cutting and shaping of materials.
- Longevity: High wear resistance extends the tool life, reducing replacement frequency.
- Polyvalence : Suitable for a wide range of materials, including metals, wood, and composites.
- Précision : Maintains tight tolerances, essential for high-precision applications.
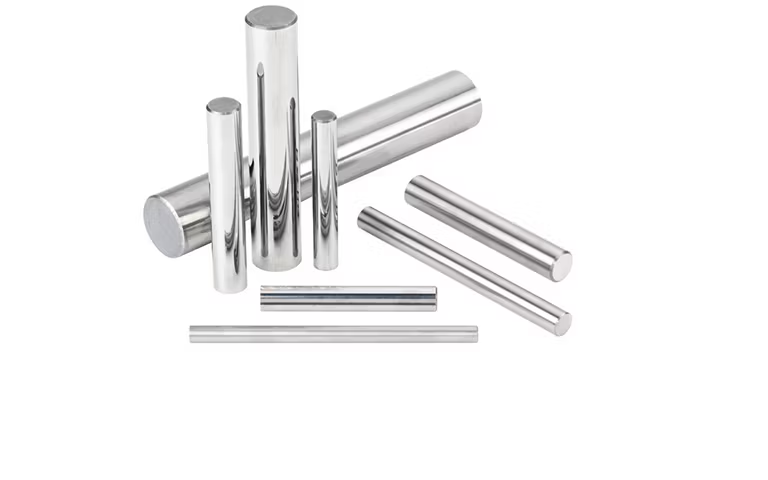
FAQ
Question | Réponse |
---|---|
What are OEM carbide rods made of? | Primarily tungsten carbide with binders like cobalt or nickel. |
Why are carbide rods preferred in cutting tools? | Due to their exceptional hardness and wear resistance. |
Comment choisir la bonne tige de carbure ? | Consider the application, material properties, and cost. |
What industries use OEM carbide rods? | Automotive, aerospace, mining, woodworking, and more. |
Toutes les tiges en carbure sont-elles identiques ? | No, they vary in composition, hardness, and application suitability. |
What is the typical hardness of carbide rods? | Ranges from 85 to 94 HRA. |
Can carbide rods be used for high-speed cutting? | Yes, especially types like T30 designed for high thermal stability. |
What are the benefits of using OEM carbide rods? | Increased tool life, precise cutting, and versatility across various materials. |
How are carbide rods manufactured? | Through a process involving powder metallurgy, pressing, and sintering. |
What is the cost range for carbide rods? | Typically between $40 to $75 per kg, depending on the type and supplier. |
Conclusion
OEM tiges en carbure are indispensable in modern manufacturing, offering unparalleled hardness, wear resistance, and precision. By understanding the different types, applications, and properties, you can select the right carbide rods to meet your specific needs. Whether you’re in automotive, aerospace, or any other industry, these rods provide the durability and performance required for high-quality production.