Qu'est-ce qu'une tige en carbure ?
Barres en carbure—those seemingly simple, cylindrical metal pieces—are anything but ordinary. They’re the unsung heroes behind many high-performance tools and applications. But what exactly are they made of? Imagine taking the hardness of diamond (well, almost!) and fusing it with the resilience of steel. That’s what you get with a carbide rod.
These rods are typically composed of tungsten carbide, a compound made by combining tungsten and carbon. Add in a bit of cobalt as a binder, and you’ve got a material that’s incredibly hard, dense, and resistant to wear and tear.
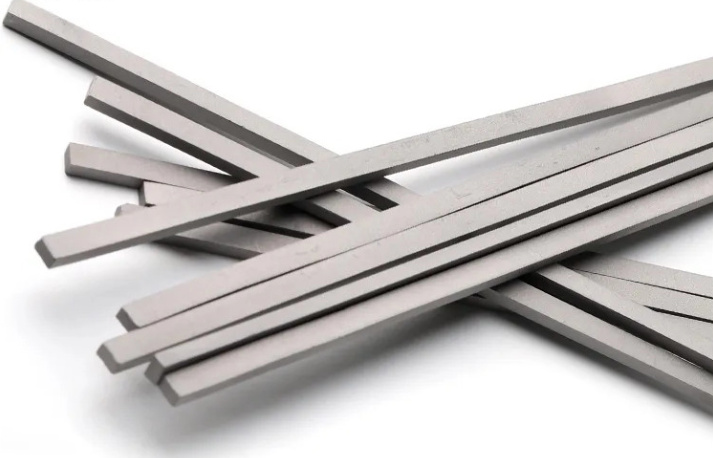
The Science of Heat Resistance
So what gives carbide rods their superpower to stand tall in the face of blazing heat? The answer lies deep in material science. Tungsten carbide has a melting point of around 2,870°C (5,198°F). That’s hotter than lava from most volcanoes. Sounds impressive, right?
The molecular structure of tungsten carbide is incredibly tight-knit, meaning heat has a hard time penetrating and breaking it apart. It doesn’t expand or contract wildly with temperature swings, so it maintains its shape and performance even when other materials would start warping or cracking. Compare that to high-speed steel (HSS), which starts to lose its hardness at just around 600°C.
Role of Cobalt Binder in Thermal Stability
If tungsten carbide is the muscle, cobalt is the glue. But not just any glue—we’re talking super-heat-resistant, industrial-grade adhesive that keeps everything together when the going gets tough.
Cobalt acts as a binder that holds the tungsten carbide grains in place. Its magic trick? It retains its toughness even at high temperatures. Cobalt allows the material to absorb mechanical stress without falling apart. Imagine it as the rubbery sole of a hiking boot. While the hard parts do the climbing, the sole ensures everything moves smoothly.
The percentage of cobalt can vary—usually between 3% and 30%—depending on the required hardness and toughness. More cobalt means better toughness but slightly reduced hardness, and vice versa.
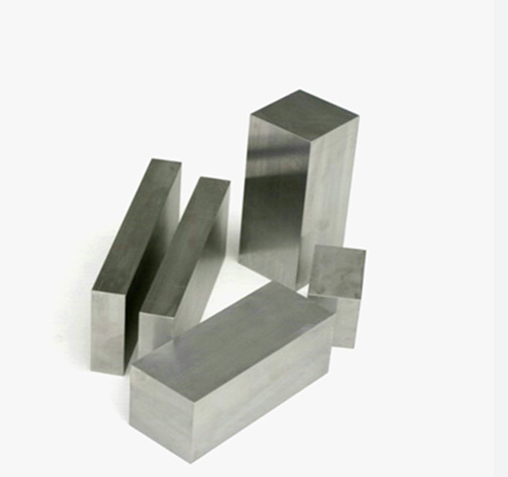
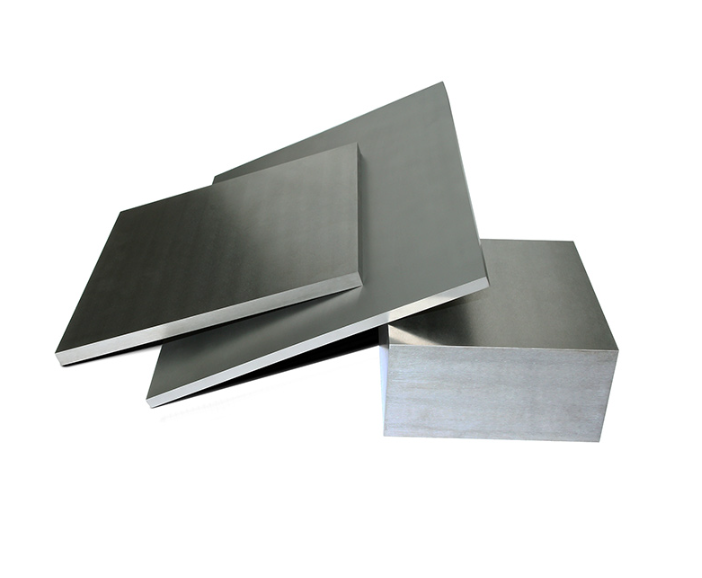

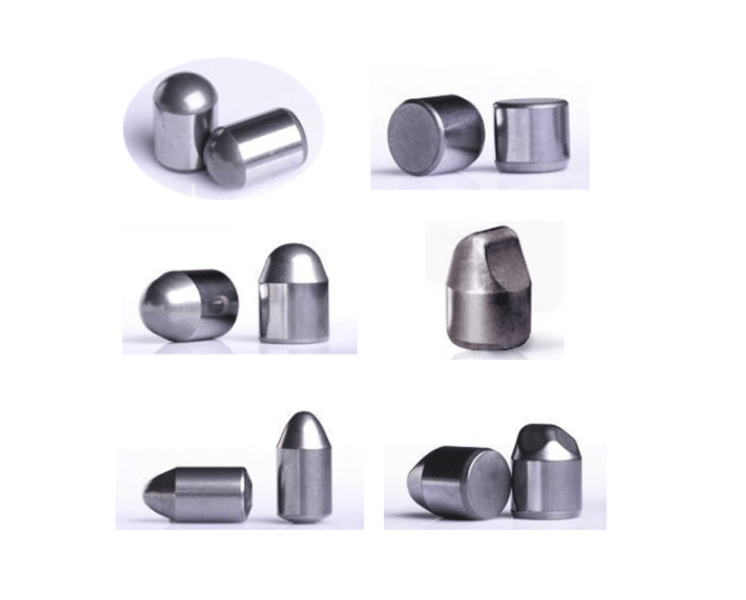
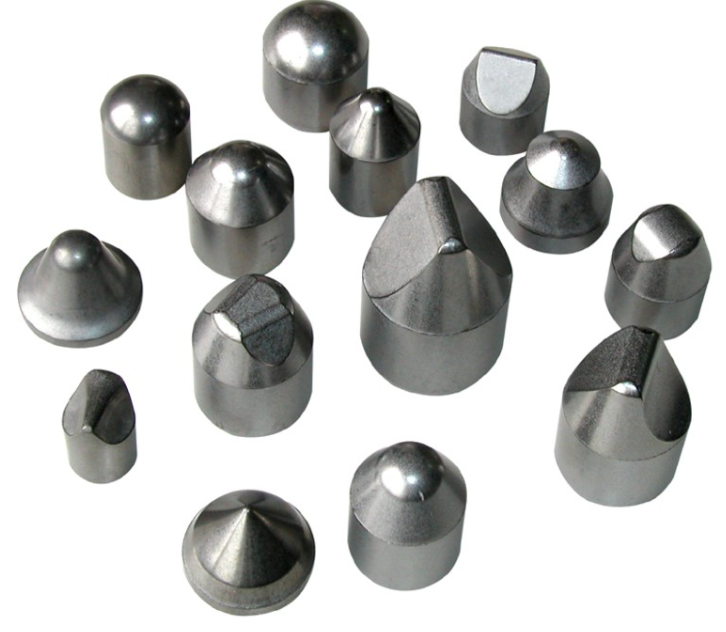
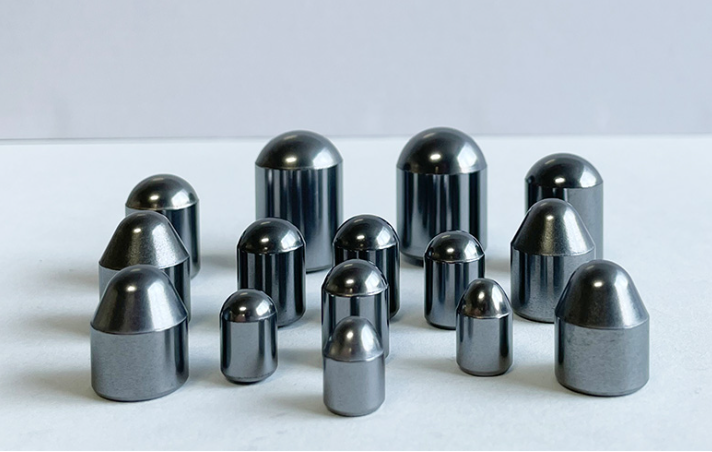
Comparison with Other Materials in High-Temperature Performance
Below is a comprehensive table that pits tungsten tiges en carbure against some other commonly used high-temperature materials. Each is measured across critical metrics like melting point, hardness, thermal expansion, and cost.
Material Performance Compared in Extreme Heat Environments
Matériau | Point de fusion (°C) | Dureté (HV) | Thermal Expansion (x10^-6/°C) | Relative Cost | Stability at 1000°C |
---|---|---|---|---|---|
Carbure de tungstène | ~2870 | 1600-2200 | 4.5 | Haut | Excellent |
Acier rapide (HSS) | ~1400 | 800-1200 | 10-13 | Faible | Pauvre |
Titanium Alloy | ~1670 | 700-1000 | 8.6 | Moyen | Juste |
Ceramic (Alumina) | ~2072 | 1500 | 7.5 | Moyenne-élevée | Bon |
Cermets | ~1700 | 1000-1500 | 6 | Moyen | Bon |
Inconel | ~1390 | 200-400 | 13 | Très élevé | Juste |
Molybdenum | ~2623 | 1500 | 5.2 | Moyen | Bon |
Acier inoxydable | ~1510 | 200-300 | 16 | Faible | Pauvre |
Niobium Alloy | ~2470 | 250-350 | 7.3 | Moyen | Juste |
Acier à outils | ~1425 | 600-900 | 10 | Faible | Pauvre |
Common Applications in High-Temperature Environments
You know that screeching drill bit or the fiery tip of a machining tool? Carbide rods are what let those tools keep going long after others have tapped out.
In aerospace, they’re used in components that touch jet engines. In automotive, they’re in tools machining engine blocks and brake discs. And in oil and gas? Oh boy, carbide rods are buried miles underground, laughing in the face of friction and heat.
But that’s not all. You’ll find them in:
- Metal cutting tools
- End mills and reamers
- Mining and construction bits
- Woodworking tools
- High-speed rotary tools
Each of these applications involves insane friction, pressure, and heat—and carbide rods don’t flinch.
Protective Coatings for Enhanced Heat Resistance
Even Superman wears a cape, right? Carbide rods may be tough, but with the right coatings, they turn almost indestructible.
Let’s talk about the popular choices:
- Nitrure de titane (TiN) : Shiny gold and ultra-hard. Boosts surface hardness and heat resistance.
- Carbonitrure de titane (TiCN) : Offers better wear resistance than TiN, especially at higher temperatures.
- Nitrure d'aluminium et de titane (AlTiN) : This one’s a beast. Perfect for dry machining and works wonders in temperatures above 800°C.
- Diamond Coating: For when you’re machining non-ferrous materials. Provides insane wear resistance.
These coatings act like armor, protecting the already tough carbide beneath from oxidation, corrosion, and extreme friction.
Modèles de poudres métalliques spécifiques utilisées dans les Tige en carbure Fabrication
Here are some of the top-performing metal powder models that form the base of high-performance carbide rods:
Modèle à poudre | Description | Dureté (HV) | Applications typiques |
---|---|---|---|
WC-10Co | 90% carbure de tungstène, 10% cobalt | 1600 | General purpose tools |
WC-6Co | 94% carbure de tungstène, 6% cobalt | 1900 | High-wear resistance tools |
WC-20Co | 80% tungsten carbide, 20% cobalt | 1400 | Mining, construction |
WC-CoCr | Cobalt-Chromium bonded | 1500 | Corrosion resistant applications |
WC-Ni | Nickel bonded carbide | 1300 | Food and chemical processing |
WC-TiC-Co | Carbure de titane ajouté | 1700 | Heat and oxidation resistant |
WC-12Co-VC | With vanadium carbide | 1650 | Anti-wear coating tools |
WC-15NiCr | Nickel-Chrome alloy binder | 1450 | Environnements à haute température |
WC-8Co + Cr3C2 | Chromium carbide additive | 1500 | Enhanced corrosion and oxidation resistance |
WC-9FeNi | Iron-Nickel binder | 1200 | Low-cost, good mechanical properties |
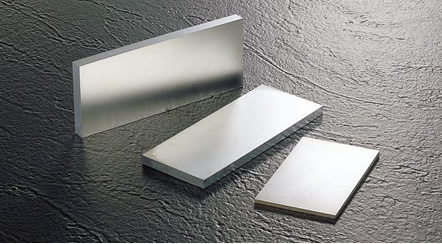
FAQ
Frequently Asked Questions: Heat Resistance in Carbide Rods
Question | Réponse |
---|---|
Why don’t carbide rods melt at high temperatures? | Tungsten carbide has a very high melting point (~2870°C), so it remains stable in most industrial heat conditions. |
How does cobalt help in heat resistance? | Cobalt acts as a binder, maintaining structural integrity even under thermal stress. |
Are carbide rods better than high-speed steel in hot environments? | Yes, carbide rods maintain hardness and shape where HSS loses performance. |
What happens if you overheat a carbide rod? | While very heat-resistant, overheating can degrade the cobalt binder and lead to thermal cracks. |
Can coatings improve thermal performance? | Absolutely. Coatings like AlTiN or TiCN can significantly enhance heat resistance and wear life. |
Which industries use carbide rods the most? | Aerospace, automotive, oil & gas, mining, and metalworking industries rely heavily on them. |
How are carbide rods made? | Typically via powder metallurgy—metal powders are sintered under high pressure and temperature. |
Can you sharpen carbide tools without damaging them? | Yes, but it requires diamond abrasives and specific grinding techniques. |
Toutes les tiges en carbure sont-elles identiques ? | Not at all. The binder content, grain size, and additives create huge performance differences. |
Is the cost worth it compared to other materials? | For high-performance or high-heat environments, absolutely. The longevity and reliability offset the initial cost. |