Vue d'ensemble
Carbure Les bandes de poinçonnage sont des composants essentiels dans la fabrication de précision, offrant une dureté, une résistance à l'usure et une durabilité inégalées. Ces bandes jouent un rôle crucial dans diverses industries, notamment l'automobile, l'aérospatiale et la métallurgie. Dans ce guide complet, nous allons explorer tout ce que vous devez savoir sur les bandes de poinçonnage en carbure, y compris leur définition, leurs principes de fonctionnement, leur utilisation, leur processus de fabrication, leurs types, les tendances du marché, leurs applications, leurs comparaisons, ainsi que leurs avantages et inconvénients.
Introduction détaillée
Qu'est-ce qu'une bande de poinçonnage en carbure ?
Les bandes de poinçonnage en carbure sont des barres allongées en carbure de tungstène, conçues pour être utilisées dans les opérations de poinçonnage et d'emboutissage. Le carbure de tungstène est un matériau composite composé de tungstène et de carbone, souvent associé à un liant métallique tel que le cobalt ou le nickel. Ces bandes sont connues pour leur dureté et leur résistance à l'usure exceptionnelles, ce qui les rend idéales pour les applications qui nécessitent un poinçonnage précis et répétitif.
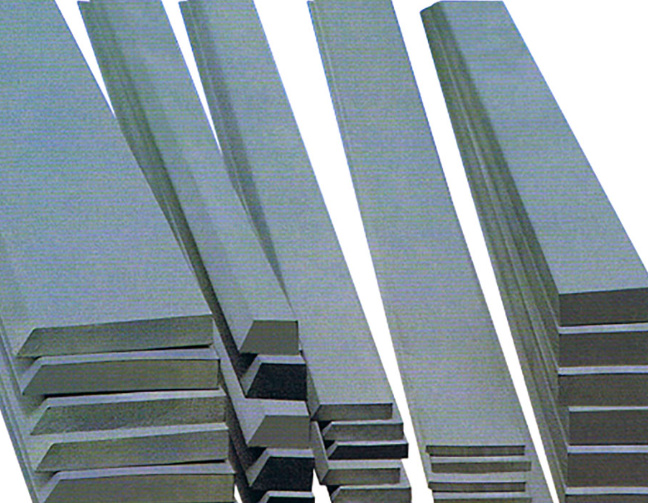
Principes de fonctionnement des bandes de poinçonnage en carbure
Les bandes de poinçonnage en carbure fonctionnent selon le principe de l'impact à haute pression. Lorsqu'une bande de poinçonnage est pressée contre un matériau, elle délivre une force concentrée qui coupe ou façonne le matériau. La dureté du carbure de tungstène permet à la bande de conserver son arête vive et de résister à l'usure, même sous une pression intense.
Comment utiliser les poinçons en carbure de tungstène
L'utilisation de bandes de poinçonnage en carbure comporte plusieurs étapes :
- La sélection: Choisissez le type et la taille appropriés de la bande de poinçonnage en carbure en fonction du matériau et de la forme de poinçonnage souhaitée.
- Installation: Fixez la bande de perforation dans la machine à perforer, en veillant à ce qu'elle soit correctement alignée.
- Fonctionnement: Utiliser la machine conformément aux instructions du fabricant, en maintenant une pression et une vitesse adéquates.
- Maintenance: Inspectez et affûtez régulièrement la bande de poinçonnage pour maintenir ses performances.
Processus de fabrication des bandes de poinçonnage en carbure
Le processus de fabrication des bandes de poinçonnage en carbure comprend les étapes suivantes :
- Mélange de poudres: La poudre de carbure de tungstène est mélangée à un liant, généralement du cobalt ou du nickel.
- Appuyer sur: Le mélange de poudres est pressé dans la forme souhaitée à l'aide d'un moule.
- Frittage: Les pièces pressées sont chauffées dans un four de frittage, ce qui permet aux particules de se lier et de former une pièce solide.
- Finition: Les pièces frittées sont rectifiées et polies pour obtenir les dimensions et l'état de surface souhaités.
Types de bandes de poinçonnage en carbure
Il existe plusieurs types de bandes de poinçonnage en carbure, chacune étant conçue pour des applications spécifiques :
- Poinçons standard en carbure: Utilisé pour les applications générales de poinçonnage.
- Bandes de poinçonnage en carbure micrograin: Fabriqué avec des particules de carbure plus petites pour un bord plus tranchant et une meilleure résistance à l'usure.
- Bandes de poinçonnage en carbure sub-micrograin: Des particules encore plus petites pour une précision et une durabilité accrues.
- Bandes de poinçonnage en carbure revêtues: Ils sont dotés d'un revêtement supplémentaire qui améliore la résistance à l'usure et réduit le frottement.
Tendances du marché
Le marché des bandes de poinçonnage en carbure se développe en raison de leur polyvalence et de leur durabilité. Les industries telles que l'automobile, l'aérospatiale et la métallurgie adoptent de plus en plus ces bandes pour leur précision et leur rentabilité. La demande de processus de fabrication avancés et de produits de haute qualité stimule la croissance du marché des bandes de poinçonnage en carbure.
Informations sur le produit
Informations de base sur les bandes de poinçonnage en carbure
Type | Composition | Propriétés | Caractéristiques | Spécifications | Applications typiques |
---|---|---|---|---|---|
Poinçons standard en carbure | WC + Co | Dureté élevée, bonne ténacité | Durable, fiable | Tailles personnalisables | Poinçonnage et emboutissage général |
Bandes de poinçonnage en carbure micrograin | WC + Co | Dureté plus élevée, meilleure résistance à l'usure | Tranchant, précis | Tailles personnalisables | Poinçonnage de précision, estampage fin |
Bandes de poinçonnage sub-micrograin | WC + Co | Dureté supérieure, excellente résistance à l'usure | Très durable, faible frottement | Tailles personnalisables | Poinçonnage à grande vitesse, emboutissage de précision |
Bandes de poinçonnage en carbure revêtues | WC + Co + Revêtement | Résistance accrue à l'usure, réduction de la friction | Durée de vie plus longue, moins d'entretien | Tailles personnalisables | Poinçonnage haute performance, matériaux abrasifs |
Description: Ce tableau fournit des informations détaillées sur les différents types de bandes de poinçonnage en carbure, en soulignant leur composition, leurs propriétés, leurs caractéristiques, leurs spécifications et leurs applications typiques.
Applications des bandes de poinçonnage en carbure
Les bandes de poinçonnage en carbure sont utilisées dans diverses industries en raison de leur précision et de leur durabilité. Voici quelques-unes des principales applications :
- Industrie automobile: Utilisé dans la fabrication de panneaux de carrosserie, de composants de moteur et d'autres pièces de précision.
- Industrie aérospatiale: Employés dans la production de composants et de pièces structurelles d'aéronefs.
- Travail des métaux: Utilisé dans les opérations de poinçonnage et d'emboutissage pour la fabrication de tôles.
- Électronique: Utilisé dans la fabrication de composants électroniques et de cartes de circuits imprimés.
- Emballage: Appliqué à la production de matériaux d'emballage et de conteneurs.
- Médical: Utilisé dans la création de dispositifs médicaux et d'instruments chirurgicaux.
- La construction: Employé dans la fabrication d'éléments de construction et d'outils.
Comparaison des fournisseurs
Comparaison de TRUER avec différents fournisseurs
Fournisseur | Localisation | Fourchette de prix (par pièce) | Spécialités |
---|---|---|---|
TRUER | ÉTATS-UNIS | $30 – $50 | Haute précision, dimensions personnalisées, livraison rapide |
ABC Carbide Suppliers | Allemagne | $35 – $55 | Excellente résistance à l'usure, vaste gamme de produits |
Outils XYZ | Chine | $25 – $45 | Commandes de gros volumes à un prix avantageux |
DEF Industriel | Japon | $40 – $60 | Technologie avancée, qualité supérieure |
Description: Ce tableau compare TRUER avec différents fournisseurs, en mettant l'accent sur la localisation, la fourchette de prix par pièce et les spécialités. Il fournit une comparaison claire pour vous aider à choisir le bon fournisseur pour vos besoins.
Avantages et limites des bandes de poinçonnage en carbure
Avantages et limites de la bande de poinçonnage en carbure
Avantages | Limites |
---|---|
Dureté élevée et résistance à l'usure | Coût plus élevé que celui d'autres matériaux |
Longue durée de vie, réduisant le remplacement des outils | Nécessite des processus de fabrication précis |
Des applications polyvalentes dans tous les secteurs d'activité | La nature fragile peut conduire à l'écaillage |
Personnalisable pour répondre à des besoins spécifiques | Limité aux applications où la fragilité n'est pas un problème |
Description: Ce tableau met en évidence les avantages et les inconvénients de l'utilisation des bandes de poinçonnage en carbure, offrant une vue équilibrée de leurs performances et de leurs limites.
Contenu connexe
Innovations dans la technologie du carbure
Les progrès récents de la technologie du carbure ont conduit au développement de nouvelles qualités et de nouveaux revêtements qui améliorent les performances des bandes de poinçonnage en carbure. Ces innovations comprennent des carbures nanostructurés et des matériaux à gradient qui offrent une ténacité et une résistance à l'usure accrues.
Maintenance et entretien des bandes de poinçonnage en carbure
Une maintenance et un entretien adéquats peuvent considérablement prolonger la durée de vie des bandes de poinçonnage en carbure. Il s'agit notamment de procéder à un nettoyage régulier, d'éviter toute chaleur excessive et de veiller à une utilisation correcte pour éviter l'écaillage et l'usure.
Impact environnemental de la fabrication du carbure
La fabrication de bandes de poinçonnage en carbure implique des processus qui peuvent avoir un impact sur l'environnement. Toutefois, les progrès réalisés en matière de recyclage et de pratiques de fabrication durables contribuent à minimiser ces effets.
Pourquoi choisir TRUER
Choisir TRUER pour votre bande de poinçonnage en carbure offre plusieurs avantages :
- Haute précision: TRUER fournit des bandes de poinçonnage en carbure de haute précision qui garantissent des performances précises et constantes.
- Dimensions sur mesure: TRUER propose des tailles personnalisables pour répondre à vos besoins spécifiques.
- Livraison rapide: Grâce à des processus de production efficaces, TRUER garantit des délais de livraison rapides.
- Excellente assistance à la clientèle: TRUER offre une assistance clientèle exceptionnelle pour vous aider à choisir et à entretenir votre bande de poinçonnage en carbure.
FAQ
Q1 : Qu'est-ce qui rend les bandes de poinçonnage en carbure supérieures aux autres matériaux de poinçonnage ?
A1 : Les bandes de poinçonnage en carbure sont supérieures en raison de leur dureté exceptionnelle, de leur résistance à l'usure et de leur capacité à conserver une arête vive dans des conditions extrêmes. Il en résulte une plus longue durée de vie des outils et de meilleures performances dans les applications exigeantes.
Q2 : Comment choisir le type de bande de poinçonnage en carbure adapté à mon application ?
A2 : Le choix dépend des exigences spécifiques de votre application, telles que le matériau poinçonné, les conditions de fonctionnement et la durée de vie souhaitée de l'outil. La consultation d'un fournisseur compétent peut vous aider à sélectionner le type approprié.
Q3 : Les bandes de poinçonnage en carbure peuvent-elles être personnalisées pour des applications spécifiques ?
A3 : Oui, les bandes de poinçonnage en carbure peuvent être personnalisées en termes de taille, de forme et de composition pour répondre aux besoins spécifiques des différentes applications. Cela garantit des performances et une efficacité optimales.
Q4 : Quelles sont les applications courantes des bandes de poinçonnage en carbure dans l'industrie automobile ?
A4 : Dans l'industrie automobile, les bandes de poinçonnage en carbure sont couramment utilisées dans la fabrication de panneaux de carrosserie, de composants de moteur et d'autres pièces de précision. Elles offrent un bord tranchant et durable qui permet de perforer le métal avec efficacité et précision.
Q5 : Quel est le coût des bandes de poinçonnage en carbure par rapport aux autres matériaux de poinçonnage ?
A5 : Bien que le coût initial des bandes de poinçonnage en carbure puisse être plus élevé que celui d'autres matériaux, leur longue durée de vie et leurs performances supérieures se traduisent souvent par des coûts globaux inférieurs en raison de la réduction des besoins de remplacement et d'entretien des outils.