L'usure est inévitable dans les secteurs de la machinerie lourde, de l'exploitation minière et de la fabrication. Plaques en carbure pour les revêtements d'usure offrent une solution exceptionnelle pour prolonger la durée de vie des équipements et améliorer leur efficacité.
Caractéristiques des plaques de carbure pour les revêtements d'usure
Plaques en carbure, principalement à base de carbure de tungstène (WC) ou carbure de chrome (CrC)sont conçus pour résister à des conditions d'usure extrêmes. Voici ce qui les rend exceptionnels :
- Dureté extrême: Avec un Dureté de Mohs de 9+.Les plaques de carbure de tungstène sont presque aussi dures que les diamants.
- Haute résistance à l'usure: Ces plaques peuvent supporter des matériaux abrasifs comme le sable, le minerai et le charbon bien plus longtemps que l'acier.
- Résistance à la corrosion: Contrairement à l'acier standard, les plaques en carbure résistent à l'oxydation et à l'exposition chimique, ce qui les rend idéales pour les environnements difficiles.
- Résistance aux chocs: Certaines compositions de carbure offrent une résistance accrue aux chocs, réduisant ainsi les risques de casse.
- Composition personnalisable: Selon l'application, les plaques de carbure peuvent être mélangées à différentes poudres métalliques pour améliorer les propriétés spécifiques.

Les 10 meilleurs modèles de poudres métalliques pour les plaques de carbure
Pour optimiser les performances, les plaques de carbure intègrent différentes poudres métalliques. En voici quelques-unes 10 poudres métalliques de premier choix utilisées dans les plaques de carbure :
Modèle de poudre métallique | Composition | Meilleur pour |
---|---|---|
WC-Co | Carbure de tungstène + Cobalt | Exploitation minière, forage |
Cr3C2-NiCr | Carbure de chrome + Nickel Chrome | Applications à haute température |
TiC | Carbure de titane | Outils de coupe, usinage à grande vitesse |
Mo2C | Carbure de molybdène | Aérospatiale, résistance extrême à l'usure |
NbC | Carbure de niobium | Industrie sidérurgique, blindage thermique |
VC | Carbure de vanadium | Outils à haute résistance |
ZrC | Carbure de zirconium | Nucléaire, résistance à la chaleur extrême |
TaC | Carbure de tantale | Aérospatiale, électronique avancée |
WC-Ni | Carbure de tungstène + nickel | Forage pétrolier, revêtements résistants à l'usure |
B4C | Carbure de bore | Applications pare-balles, armures légères |
Secteurs d'application courants des plaques de carbure pour revêtements d'usure
Les revêtements d'usure en carbure jouent un rôle crucial dans diverses industries où la durabilité et la longévité sont essentielles. Voici quelques-unes des industries qui bénéficient le plus des plaques en carbure :
1. Mines et carrières
- Utilisé dans les revêtements de goulottes, les trémies et les bandes transporteuses pour résister à l'abrasion de la roche.
- Prolonge la durée de vie des concasseurs et broyeurs.
2. Forage de pétrole et de gaz
- Essentiel pour forets et revêtements résistants à l'usure sur les machines d'extraction.
- Réduit les temps d'arrêt dus à l'usure prématurée.
3. Construction et terrassement
- Revêtements de godets de pelleteuses, lames de bulldozerset les plaques d'usure bénéficient de plaques en carbure.
- Améliore la résistance aux terrains difficiles et aux charges d'impact.
4. Fabrication d'acier et de métal
- Protège les parois des fours, les revêtements des poches de coulée et les laminoirs.
- Réduit les dommages causés par la chaleur et la corrosion dans des conditions extrêmes.
5. Agriculture et sylviculture
- Utilisé dans socs, matériel de récolteet les lames de scie.
- Prévient l'usure due au sol, au gravier et à la végétation.
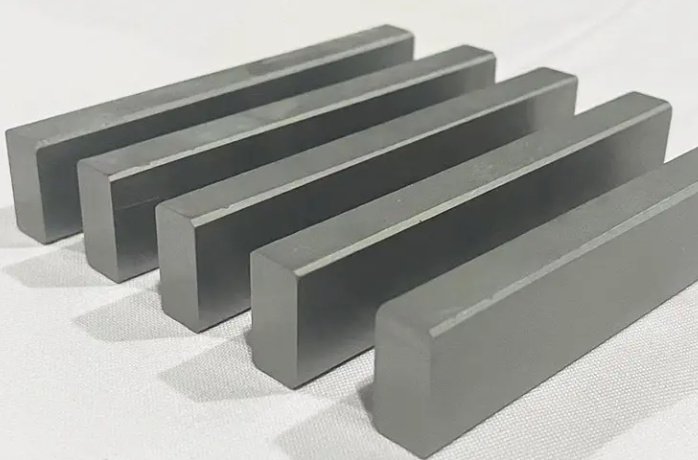
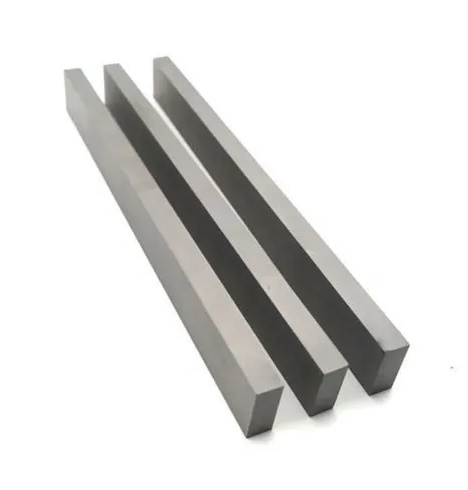
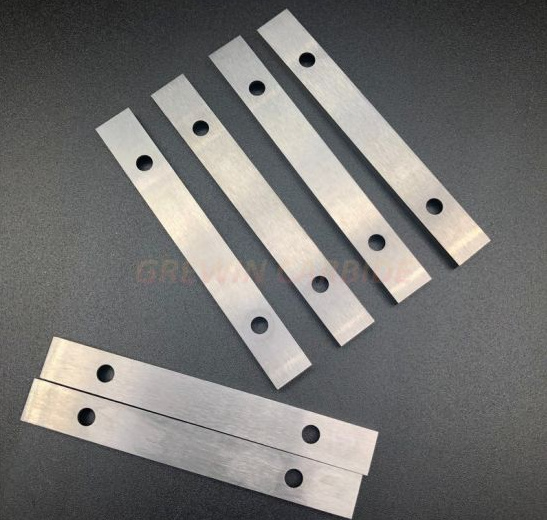
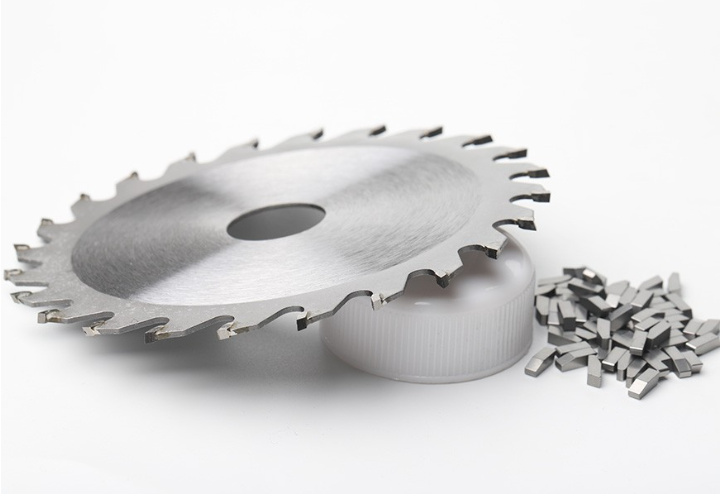
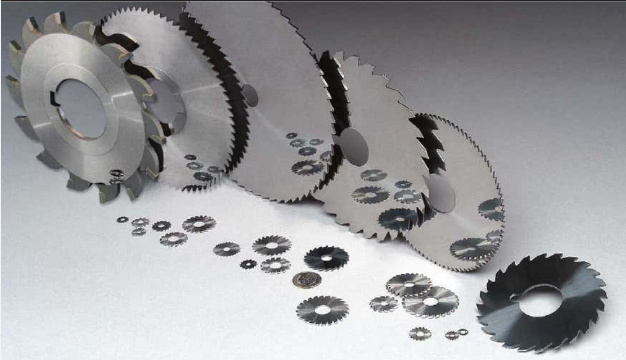
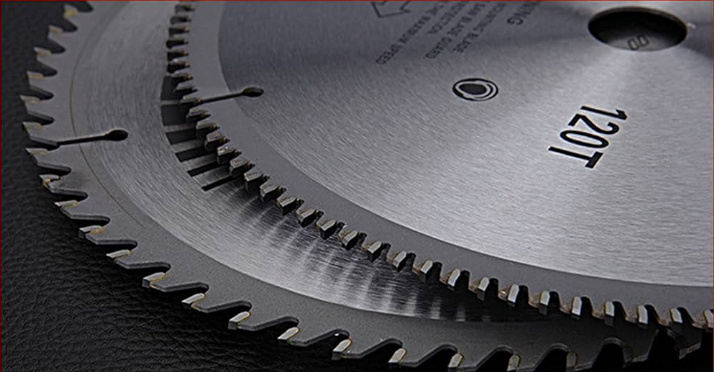
Comment choisir les plaques de carbure appropriées pour les revêtements d'usure ?
Choisir le bon plaques en carbure dépend de plusieurs facteurs. Voici ce qu'il faut prendre en compte :
- Composition du matériau - WC-Co pour l'exploitation minière, Cr3C2-NiCr pour les hautes températures, etc.
- Dureté et ténacité - Dureté plus élevée pour la résistance à l'abrasion, mais ténacité accrue pour la résistance aux chocs.
- Environnement de l'application - Résistance à la corrosion nécessaire ? Chaleur élevée ? Charges d'impact élevées ?
- Épaisseur et taille - Les plaques plus épaisses durent plus longtemps mais peuvent être plus lourdes et plus coûteuses.
- Coût et longévité - Un investissement initial plus élevé se traduit souvent par des coûts de remplacement moins élevés à long terme.
Plaques en carbure et autres matériaux résistants à l'usure
Propriété | Plaques en carbure de tungstène | Plaques de carbure de chrome | Acier trempé | Céramique |
---|---|---|---|---|
Dureté | Extrême (9+ Mohs) | Haute (6-7 Mohs) | Modéré (4-6 Mohs) | Très élevé (9-10 Mohs) |
Résistance à l'usure | Supérieure | Excellent | Bon | Supérieure |
Résistance aux chocs | Modéré | Haut | Haut | Faible |
Résistance à la corrosion | Haut | Très élevé | Faible | Haut |
Résistance à la chaleur | Haut | Très élevé | Modéré | Haut |
Coût | Haut | Moyen | Faible | Haut |
Comment l'installer et l'entretenir Plaques de carbure pour les revêtements d'usure
Techniques d'installation
- Soudage: Meilleur pour les applications à forte charge, mais nécessite de la précision pour éviter les fissures.
- Boulonnage: Permet un remplacement facile mais peut ne pas être aussi sûr que le soudage.
- Collage d'adhésifs: Utilisé dans les zones à faible impact où le soudage n'est pas possible.
Conseils d'entretien
- Inspections régulières: Vérifier l'absence de fissures, de traces d'usure et de corrosion.
- Procédures de nettoyage: Utiliser des nettoyants non abrasifs pour éviter d'endommager la surface.
- Remplacements en temps voulu: Remplacer les sections avant une défaillance complète afin d'éviter un arrêt de la machine.
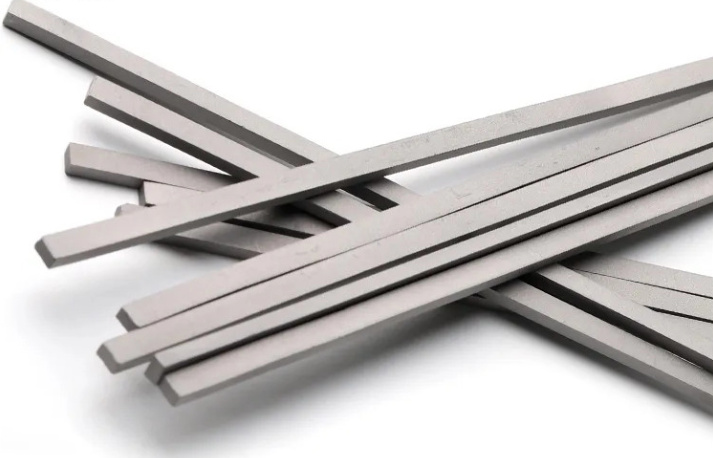
FAQ
Question | Réponse |
---|---|
Quelle est la durée de vie des revêtements d'usure en carbure ? | Elle varie en fonction de l'application, mais dure généralement 3 à 10 fois plus long que les liners en acier. |
Les plaques en carbure sont-elles chères ? | Ils ont un coût initial plus élevé mais réduisent la fréquence de remplacement, ce qui les rend rentables à long terme. |
Les revêtements en carbure peuvent-ils être personnalisés ? | Oui ! Ils peuvent être coupés, façonnés et alliés pour répondre à des besoins industriels spécifiques. |
Comment savoir si j'ai besoin de carbure de tungstène ou de chrome ? | Carbure de tungstène est le meilleur pour résistance à l'abrasion, tandis que carbure de chrome excelle dans environnements à haute température. |
Les plaques en carbure sont-elles respectueuses de l'environnement ? | Oui, ils réduire les déchets de matériaux et sont souvent recyclables. |