Qu'est-ce que Plaques de carbure?
Plongeons dans un sujet qui pourrait sembler appartenir à un laboratoire de haute technologie : les plaques de carbure. Mais croyez-moi, ce matériau est le héros méconnu de l'industrie manufacturière. Les plaques de carbure, également appelées plaques de carbure de tungstène, sont des petites bêtes résistantes fabriquées à partir de poudre de carbure de tungstène - un matériau plus dur que presque tout le reste, à l'exception du diamant. Ces plaques sont largement utilisées dans des industries telles que la métallurgie, l'exploitation minière, la construction et même l'aérospatiale en raison de leur durabilité exceptionnelle, de leur résistance à l'usure et de leur capacité à conserver leur solidité sous une chaleur et une pression intenses.
Il s'agit en quelque sorte de l'armure la plus résistante du monde industriel. Il ne s'agit pas de simples morceaux de métal, mais de produits manufacturés, fabriqués par des procédés de frittage qui fusionnent le carbure de tungstène avec un liant (généralement du cobalt), ce qui donne un composé qui résiste à la corrosion, à la déformation et à la fissuration comme un champion.
Ainsi, la prochaine fois que vous verrez une perceuse ou un outil de coupe qui ronge des matériaux durs comme s'il s'agissait de beurre, il y a de fortes chances qu'il soit alimenté par des plaques de carbure en coulisses.
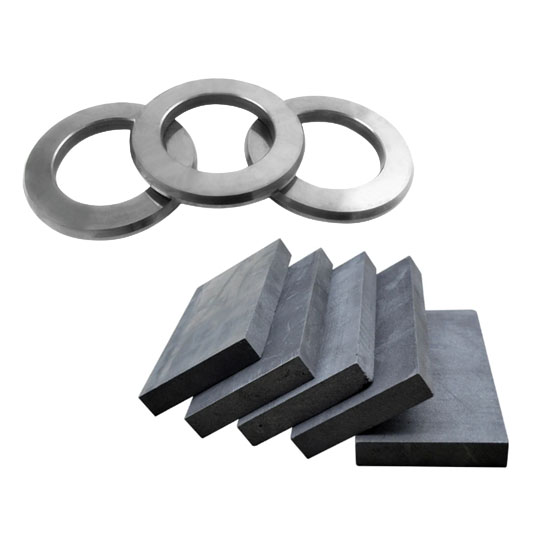
Importance des normes industrielles
Pourquoi s'intéresser aux normes de fabrication des plaques de carbure ? Les fabricants ne peuvent-ils pas se contenter de fabriquer ce qui fonctionne et s'en tenir là ? Non, pas si l'on se soucie de la qualité, de la sécurité et de la cohérence.
Les normes industrielles sont en quelque sorte le mode d'emploi de l'ensemble du processus. Elles garantissent des performances prévisibles, quel que soit le lieu de fabrication des plaques de carbure (Allemagne, Chine ou États-Unis). C'est important pour le commerce mondial, la fiabilité des produits et la sécurité des opérations.
Imaginez la construction d'un moteur à réaction ou d'une plate-forme pétrolière à l'aide d'outils qui pourrait se brisent sous la pression. Ce n'est pas bon, n'est-ce pas ? C'est là que ces normes brillent. Elles garantissent :
- Composition chimique homogène
- Dimensions physiques uniformes
- Propriétés mécaniques fiables telles que la dureté et la résistance à la rupture
- Reproductibilité des performances d'un lot à l'autre
Oui, les normes ne sont pas que de la paperasserie. Elles sont le ciment de la promesse de qualité industrielle.
Normes communes pour les Plaque de carbure Fabrication
C'est ici que nous entrons dans le vif du sujet : quelles sont les normes auxquelles les plaques en carbure doivent satisfaire ?
1. ISO 513 - Classification internationale des outils
Utilisée dans le monde entier, la norme ISO 513 classe les plaques de carbure en fonction de leur application : P (acier), M (inoxydable), K (fonte), N (non-ferreux), S (alliages résistants à la chaleur) et H (acier trempé).
2. ISO 3327 - Carbures métalliques frittés - Dimensions et tolérances
Spécifie les formes, les tailles et les écarts admissibles. Il s'agit en quelque sorte de la règle qui régit la vie des fabricants de carbure.
3. ASTM B777 - Spécification standard pour les alliages métalliques haute densité à base de tungstène
Principalement pertinent pour les carbures de tungstène de haute densité utilisés dans le blindage contre les radiations et dans l'aérospatiale.
4. ANSI B212.15 - Normes nationales américaines pour les plaquettes en carbure
Couvre la nomenclature, les tolérances géométriques et les conditions de coupe recommandées pour les plaques utilisées dans les outils de coupe.
5. DIN ISO 3366 - Norme allemande équivalente à la norme ISO pour les carbures
Utile pour les applications européennes. Se concentre sur les caractéristiques des matériaux et la résistance à la chaleur.
6. GOST 3882-74 - Norme russe pour les alliages durs
Toujours référencé dans les pays d'Europe de l'Est et de la CEI. Décrit les qualités, les compositions et les traitements thermiques.
7. JIS B 4051 - Norme industrielle japonaise pour les nuances de carbure cémenté
Fournit une nomenclature normalisée et des paramètres d'essai pour la résistance à l'usure et la ténacité à la rupture.
8. GB/T 13865-2008 - Norme nationale chinoise
Couvre les matériaux en carbure, les cas d'utilisation recommandés et les procédures d'essai.
9. SAE AMS 7876 - Spécification des matériaux aérospatiaux pour le carbure de tungstène
Essentielle pour les composants aéronautiques, elle spécifie la composition des poudres et les processus de frittage.
10. ISO 3290-1 - Billes de précision - Spécifications pour les billes en carbure
Bien qu'elle concerne principalement les roulements à billes, cette norme ISO a un impact sur les pièces en carbure sphérique fabriquées à partir de poudres de base similaires.
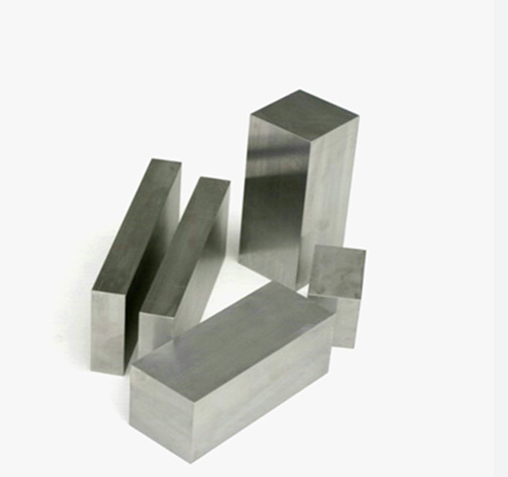
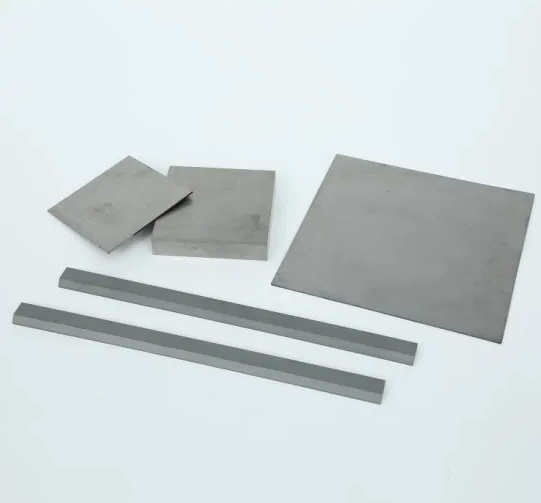
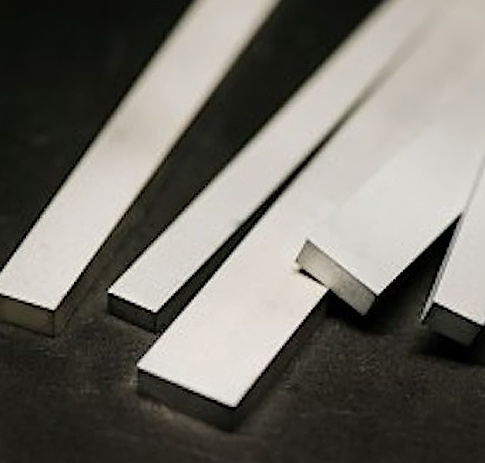
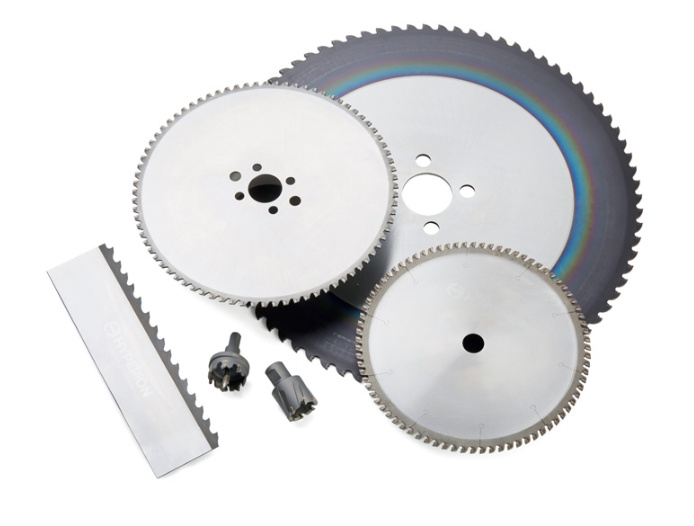
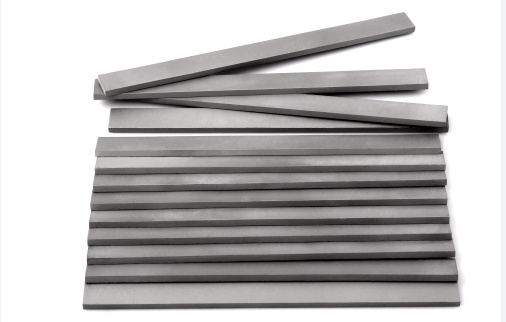
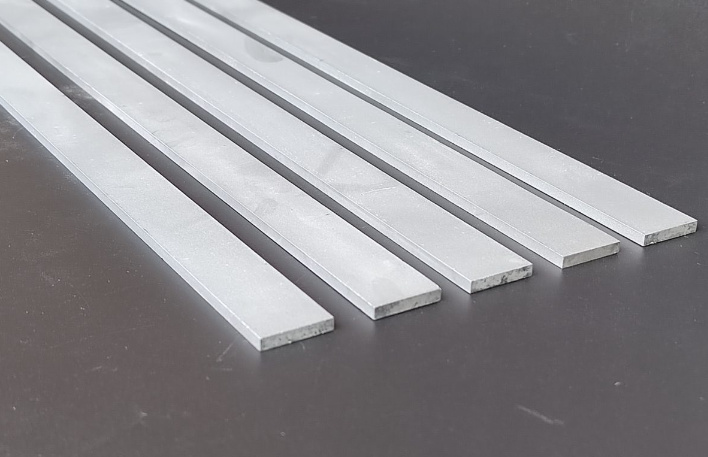
Paramètres clés définis par Plaque de carbure Normes
Vous trouverez ci-dessous un tableau reprenant les paramètres les plus importants définis par les normes internationales du carbure.
Spécifications techniques définies par les normes relatives aux plaques de carbure
Paramètres | Description | Pourquoi c'est important |
---|---|---|
Taille des grains | Gamme de mesures allant de l'échelle submicronique à plusieurs microns | Affecte le compromis ténacité/dureté |
Dureté (HRA) | Typiquement 86-94 HRA | Une valeur plus élevée signifie une plus grande résistance à l'usure |
Résistance à la rupture transversale | Mesuré en MPa | Indique la capacité à résister à la rupture sous contrainte |
Densité | 14-15,5 g/cm³ pour les qualités WC-Co | Reflète la teneur en liant et la compacité globale |
Teneur en cobalt (%) | Fourchette de 4% à 30% | Plus de cobalt = plaque plus résistante mais plus souple |
Taux de porosité | Échelle de A (aucun) à C (pores visibles) | Impact sur l'intégrité structurelle et la longévité des performances |
Saturation magnétique | Utilisé pour détecter la consistance de la phase du liant | Aide au contrôle de qualité et garantit un comportement prévisible |
Conductivité thermique (W/mK) | Généralement de 70 à 100 | Crucial pour la gestion de la chaleur dans les outils à grande vitesse |
Module d'élasticité (GPa) | ~500-700 | Reflète la rigidité, utile pour les conceptions porteuses. |
Finition de la surface | Mesuré en Ra (microns) | Impacts sur la compatibilité avec les revêtements et les ajustements de précision |
Contrôle de la qualité et essais dans la production de plaques de carbure
Parlons des tests, car même les meilleures normes ne signifient pas grand-chose si personne n'en vérifie le respect. Le contrôle de la qualité des plaques de carbure implique :
- Fluorescence des rayons X (XRF) pour confirmer la composition
- Microscopie électronique à balayage (MEB) pour observer les limites des grains et la porosité
- Tests de saturation magnétique pour détecter les variations de phase du liant
- Essais par ultrasons pour détecter les fissures ou les vides internes
- Essais destructifs (comme la résistance à la rupture transversale) aux limites mécaniques de référence
Les fabricants fiables appliquent des procédures d'inspection rigoureuses à chaque étape de la production - mélange de poudres, pressage, frittage, finition - afin d'éliminer la variabilité et de garantir des performances à long terme.
Comment choisir un fabricant de plaques de carbure fiable ?
Le choix du bon fabricant n'est pas seulement une question de prix. Vous voulez un fabricant qui respecte les règles - ou, mieux encore, qui les dépasse. Voici comment reconnaître un bon fabricant :
- Certifications: Les normes ISO 9001, ISO 14001 et les accréditations industrielles spécifiques (par exemple, API, aérospatiale) sont des drapeaux verts.
- Des rapports d'essai cohérents: Demandez les données des essais mécaniques et comparez-les d'un lot à l'autre.
- Traçabilité des matériaux: Peut-on savoir d'où provient chaque gramme de poudre ?
- Soutien à l'ingénierie personnalisée: Les meilleurs d'entre eux adapteront les compositions et les géométries à vos besoins.
- Support après-vente: Recherchez des politiques de garantie claires, des conseils d'utilisation et des services de réaffûtage.
- Références globales: Les témoignages de grands acteurs de l'industrie automobile, minière ou aérospatiale sont précieux.
Dans ce domaine, la réputation ne s'acquiert pas du jour au lendemain, elle se forge sous la pression, tout comme la réputation de l'entreprise. plaques en carbure.
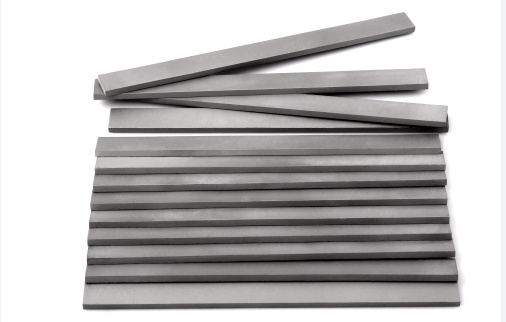
FAQ
Question | Réponse |
---|---|
De quoi sont faites les plaques de carbure ? | Il s'agit principalement de poudre de carbure de tungstène mélangée à un liant tel que le cobalt, pressée en forme et frittée à haute température. |
Quelle est la qualité la plus dure de la plaque de carbure ? | Les qualités à grains ultrafins avec une faible teneur en cobalt (par exemple, WC-Co avec ~4% Co) offrent une dureté maximale, atteignant 93-94 HRA. |
Les plaques en carbure sont-elles toutes magnétiques ? | Uniquement ceux contenant des liants à base de cobalt ou de nickel. Le magnétisme permet de détecter la qualité de la phase du liant. |
Comment puis-je vérifier si une plaque est conforme aux normes ISO ? | Demandez un certificat de matériau ou un test de laboratoire indépendant attestant de la conformité aux normes ISO ou ASTM. |
Quelles sont les causes de défaillance des plaques de carbure ? | Généralement fatigue thermique, érosion du liant, ou utilisation incorrecte de matériaux non compatibles. |
Les plaques de carbure peuvent-elles être recyclées ? | Oui ! Les plaques usagées peuvent être broyées et retraitées pour en fabriquer de nouvelles - c'est ce qu'on appelle le frittage secondaire. |
Comment le pourcentage de cobalt affecte-t-il les performances ? | Plus de cobalt = plus résistant mais moins dur. Moins de cobalt = plus dur mais plus fragile. |
Pourquoi la taille des grains est-elle importante ? | Les grains fins augmentent la dureté mais réduisent la ténacité ; les gros grains font l'inverse. L'équilibre dépend de l'application. |
Les plaques de carbure chinoises répondent-elles aux normes internationales ? | C'est souvent le cas, en particulier chez les fournisseurs certifiés. Demandez toujours des documents de conformité et effectuez des tests indépendants pour vous en assurer. |
Quelle est la durée de vie typique d'une plaque de carbure ? | Cela dépend de l'utilisation, mais peut aller de quelques mois à quelques années dans les environnements à forte usure. |