Qu'est-ce que Carbide Materials?
Carbide materials might sound like something out of a science fiction novel, but trust me—they’re very real and very powerful. At the core, carbide is a compound composed of carbon and a less electronegative element, usually a metal. The most common and widely used type is tungsten carbide, a compound of tungsten and carbon that’s nearly as hard as diamonds. Imagine trying to scratch a diamond with steel—it’s just not going to happen. But tungsten carbide? That stuff comes close to giving diamonds a run for their money.
Carbide materials are sintered powders, made by compressing metal powders and heating them to bond without melting. This process creates tools that are insanely tough, wear-resistant, and able to maintain their shape under brutal heat and pressure. This makes them perfect for precision machining—where accuracy isn’t just appreciated, it’s mandatory.
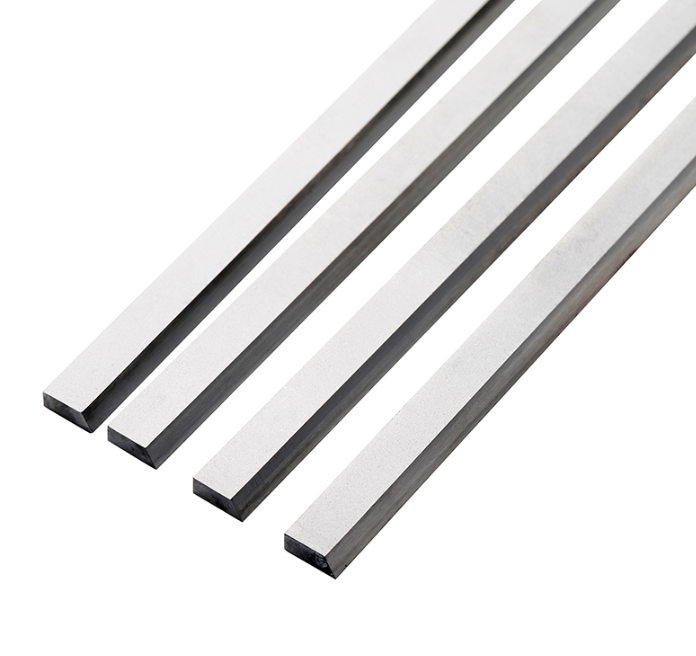
Role of Carbure in Precision Machining
Now, let’s talk machining—the unsung hero of modern manufacturing. Every sleek smartphone, shiny car part, or medical device likely owes its finish to high-precision machining. And right at the heart of that process? Carbide tools.
Carbide tools cut cleaner, faster, and with more precision than traditional steel. Why? Because they can withstand heat without softening. When you’re spinning at thousands of RPMs, generating massive friction, the last thing you want is a tool that melts like butter. Carbide tools stay cool, sharp, and reliable.
Compared to high-speed steel (HSS), carbide tools last 10 to 20 times longer. They’re like the marathon runners of the tool world—sturdy, consistent, and tireless. You get better surface finishes, tighter tolerances, and reduced downtime. And let’s face it—less downtime means more profit.
Key Industries Leveraging Carbide Tools
You’d be surprised just how many industries are riding the carbide wave. Here are a few of the big players:
1. Aerospace Industry
Precision is everything in aerospace. If a turbine blade is even slightly off, you’re risking performance failure. Carbide tools allow aerospace engineers to machine titanium, Inconel, and other tough alloys with pinpoint accuracy.
2. Automotive Sector
From engine blocks to transmission components, automotive manufacturing depends on tight tolerances and smooth finishes. Carbide tools help deliver that consistency while keeping production lines humming.
3. Medical Device Manufacturing
Think of orthopedic implants or surgical instruments. These parts are tiny, complex, and must be flawless. Carbide micro-tools can handle the delicate machining of stainless steel and titanium with finesse.
4. Oil & Gas Industry
Drilling components, valves, and pump parts are exposed to extreme pressure and corrosive environments. Carbide’s durability ensures these parts meet demanding specs.
5. Electronics and Semiconductor Fields
Miniaturization requires ultra-precise machining. Carbide tools help fabricate microscopic components with clean, repeatable results.
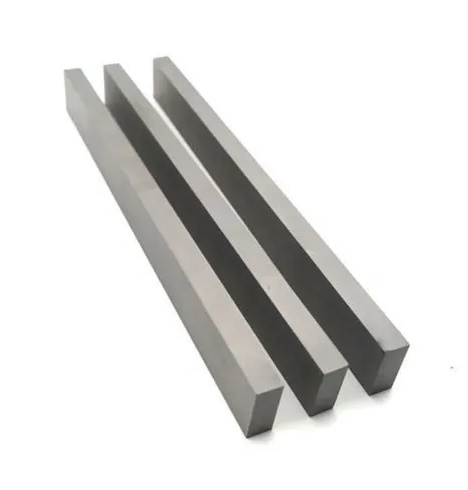
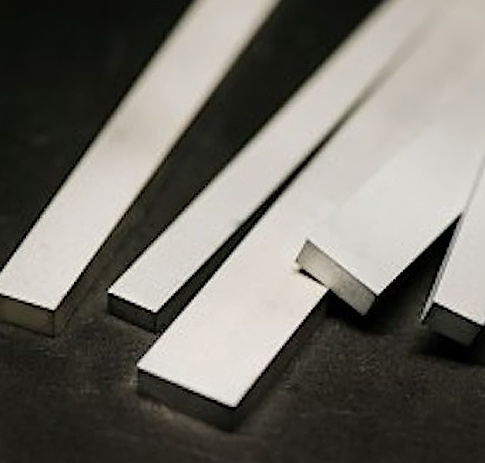
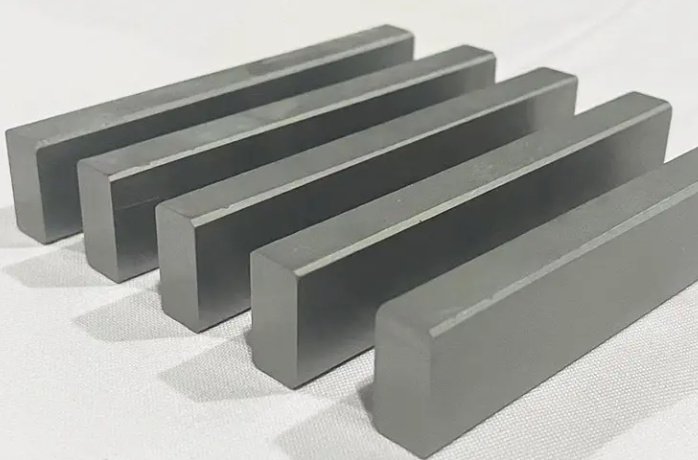
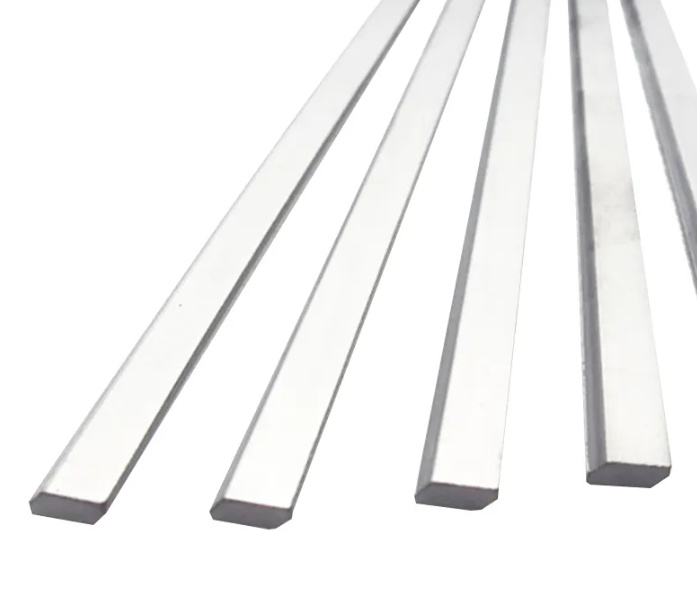
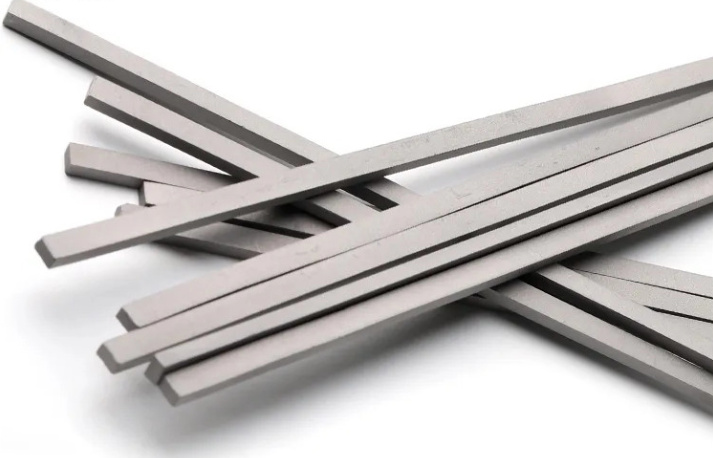
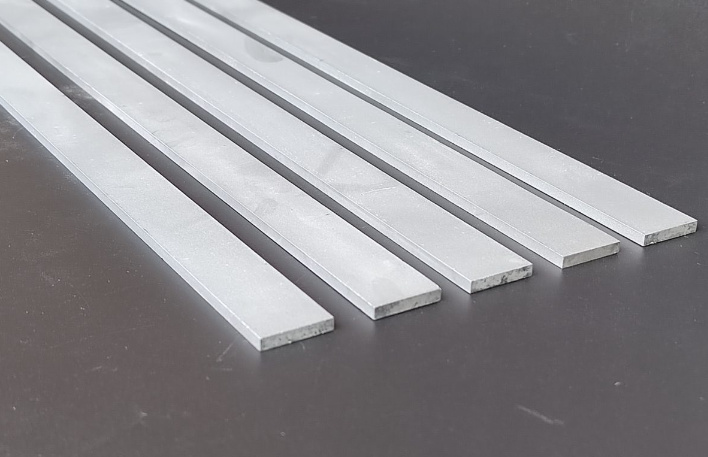
Comparaison des Outils en carbure Versus Traditional Materials
Advantages and Performance Comparison: Carbide vs. Traditional Tooling Materials
Fonctionnalité | Outils en carbure | High-Speed Steel (HSS) Tools | Outils en céramique | CBN/PCD Tools |
---|---|---|---|---|
Dureté | Extrêmement élevé | Modéré | Très élevé | Très élevé |
Résistance à la chaleur | Excellent (up to 1000°C) | Fair (up to 600°C) | Très élevé | Excellent |
Résistance à l'usure | Supérieure | Plus bas | Haut | Excellent |
Durée de vie de l'outil | Long (10x to 20x HSS) | Plus court | Moyen | Très longue |
Qualité de l'état de surface | Smooth and precise | Less consistent | Haut | Ultra-high |
Coût | Higher upfront, lower over time | Cheap upfront, costly in maintenance | Haut | Très élevé |
Matériaux appropriés | Alloys, stainless steel, titanium | Aluminum, mild steel | Hardened steel, cast iron | Non-ferrous, abrasive materials |
Application Versatility | Haut | Modéré | Specialized | Niche |
Top Metal Powder Models for Carbide Tooling
These are some of the most trusted and high-performing carbide powder models used in manufacturing precision tools:
Modèle à poudre | Description |
---|---|
WC-Co (carbure de tungstène-cobalt) | Most widely used. Offers high hardness and toughness. Perfect for cutting tools and mining equipment. |
WC-Ni (carbure de tungstène-nickel) | Corrosion-resistant alternative to WC-Co. Ideal for medical and marine applications. |
TiC (carbure de titane) | Exceptional hardness and oxidation resistance. Commonly used in composite coatings. |
TaC (carbure de tantale) | Highly corrosion-resistant. Used in applications involving acidic environments and in aerospace. |
NbC (carbure de niobium) | Improves high-temperature strength. Often alloyed with other carbides for tough composites. |
Cr3C2 (carbure de chrome) | Excellent wear and oxidation resistance. Often used for coating and wear applications. |
VC (carbure de vanadium) | Enhances grain structure and hardness in cutting tool composites. |
Mo2C (carbure de molybdène) | Balances strength and corrosion resistance. Often used in alloy matrices. |
ZrC (carbure de zirconium) | High melting point and chemical resistance. Found in nuclear and space industries. |
HfC (carbure de hafnium) | One of the highest melting points known. Used in extreme-temperature environments like space shuttle nose cones. |
Emerging Trends in Carbide Machining
You’d think something as old-school as metal cutting wouldn’t change much—but carbide machining is evolving fast. The tech is hot, and not just literally.
1. Nanostructured Carbides
Imagine building tools at the atomic level. Nanostructured carbides are setting the stage for even harder, tougher, and more wear-resistant tools. Their grain size is 100x smaller than traditional carbides, offering unmatched mechanical properties.
2. Additive Manufacturing with Carbide Powders
3D printing with metal powders is revolutionizing how we think about tool production. Carbide powders are being sintered into complex shapes that were impossible with traditional machining. Less waste, more freedom.
3. Smart Machining and Tool Monitoring
Sensors embedded in carbide tools? Yep, it’s happening. Smart tools can now monitor wear, temperature, and cutting force in real-time, making predictive maintenance a breeze.
4. Eco-Friendly Binders
Cobalt has always been a reliable binder in carbide, but it’s also toxic. New research is pushing for cobalt-free or recycled binders, making the process more sustainable without compromising performance.
5. AI-Driven Tool Design
With machine learning, we’re seeing optimized geometries for carbide tools. These AI-designed tools reduce vibration, increase life, and enhance cutting performance in ways we couldn’t manually calculate.
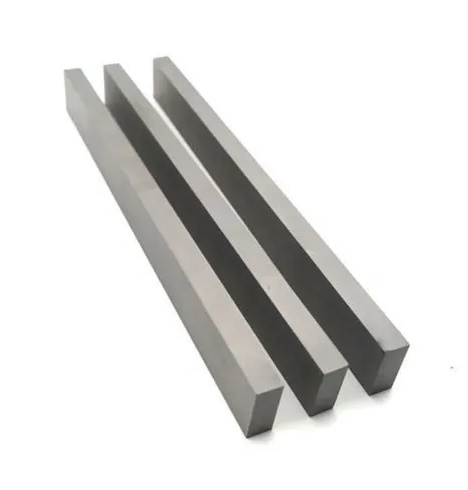
FAQ
Question | Réponse |
---|---|
What are carbide materials? | Carbides are compounds of carbon and metals, known for extreme hardness, wear resistance, and high-temperature stability. |
Why are carbide tools better than steel tools? | They last longer, stay sharper under heat, and deliver cleaner, more precise cuts, making them ideal for high-performance machining. |
Which industries use carbide tools the most? | Aerospace, automotive, medical device manufacturing, oil & gas, and electronics all rely heavily on carbide tooling. |
How is carbide made? | Through powder metallurgy—metal powders are compressed and sintered to form hard, durable tools. |
Are there environmentally friendly carbide options? | Yes, newer cobalt-free binders and recycled powders are helping make carbide tools more eco-friendly. |
Can carbide be used in 3D printing? | Absolutely! Additive manufacturing with carbide powders is an emerging trend for creating complex, high-performance parts. |
How do smart carbide tools work? | They include embedded sensors to monitor wear, cutting force, and temperature in real time, aiding predictive maintenance. |
What are some key carbide powder models? | WC-Co, WC-Ni, TiC, TaC, NbC, Cr3C2, VC, Mo2C, ZrC, HfC—each with unique advantages for different applications. |
Are carbide tools more expensive? | Initially, yes—but their longevity and performance result in lower total cost of ownership compared to traditional tools. |
Is carbide machining future-proof? | With ongoing innovations like AI design and nanostructured powders, carbide machining continues to lead the way in advanced manufacturing. |