Vue d'ensemble Boutons en carbure
Les boutons en carbure, souvent appelés boutons en carbure cémenté, sont des composants essentiels utilisés dans diverses industries, en particulier dans l'exploitation minière, le forage et les outils de coupe. Ces composants sont réputés pour leur incroyable dureté, leur résistance à l'usure et leur capacité à supporter des pressions élevées, ce qui les rend indispensables dans les environnements difficiles. Mais que sont exactement les boutons en carbure et pourquoi sont-ils si importants dans ces applications ?
Imaginez que vous essayez de couper un matériau résistant comme de la roche ou de l'acier. Les outils ordinaires n'y parviendraient pas, littéralement. C'est là que les boutons en carbure entrent en jeu. Ce sont les héros des tâches difficiles, qui réussissent là où d'autres échoueraient. Dans cet article, nous allons explorer tout ce que vous devez savoir sur les boutons en carbure, depuis leurs types et leurs applications jusqu'à la façon dont vous pouvez sélectionner le bon bouton pour vos besoins spécifiques. Plongeons dans le vif du sujet !
Qu'est-ce qu'un bouton en carbure ?
Les boutons en carbure sont de petites pièces en forme de bouton fabriquées à partir de carbure cémenté, un matériau composite composé de particules de carbure dur liées entre elles par un liant métallique. Le carbure de tungstène (WC) est le type le plus courant, connu pour sa dureté et sa durabilité exceptionnelles.
Pourquoi les boutons en carbure sont-ils si résistants ?
En d'autres termes, les boutons en carbure sont aussi durs que des clous, voire plus durs encore. Le carbure de tungstène, le principal matériau utilisé dans ces boutons, est presque aussi dur que le diamant. Cela signifie que les boutons en carbure peuvent couper presque tout. Mais pourquoi cette dureté est-elle si importante ? Dans des secteurs comme l'exploitation minière ou le forage pétrolier, les outils sont soumis à des conditions extrêmes : pression élevée, abrasion et chaleur. Les boutons en carbure sont conçus pour résister à ces conditions sans transpirer, ce qui les rend inestimables pour les tâches lourdes.
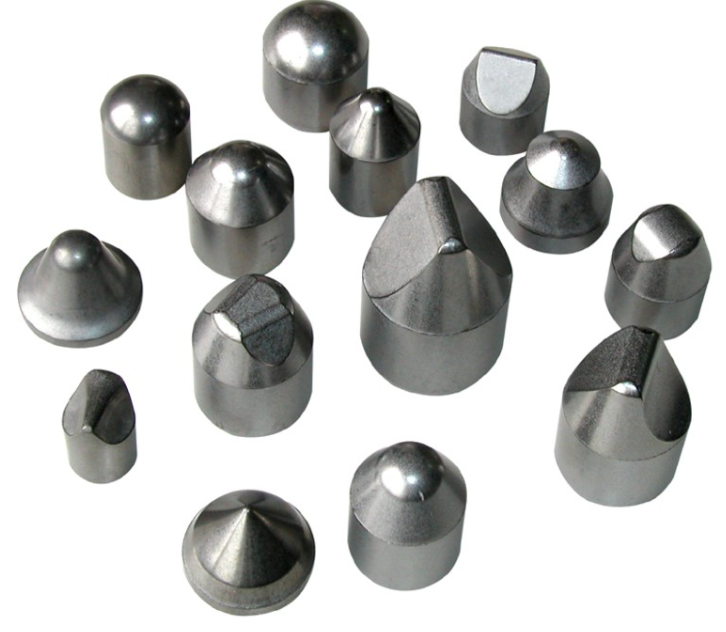
Types de boutons en carbure
Les boutons en carbure se présentent sous différentes formes, tailles et compositions, chacune d'entre elles étant conçue pour des applications différentes. Qu'il s'agisse de forer dans de la roche tendre ou de découper du métal dur, il existe un bouton en carbure adapté à la tâche à accomplir. Nous présentons ici les types les plus courants.
Types courants de boutons en carbure
Type | Description |
---|---|
Boutons en carbure sphérique | Les boutons sphériques sont utilisés pour les formations extrêmement dures. Ils offrent une excellente résistance à l'usure et sont conçus pour minimiser le risque de rupture pendant le forage. |
Boutons coniques en carbure | Idéal pour les formations moyennes à dures, les boutons coniques offrent un équilibre entre le taux de pénétration et la durabilité. |
Boutons en carbure à tête plate | Ils sont utilisés dans les formations plus tendres où des taux de pénétration élevés sont nécessaires. Ils s'usent plus rapidement que les boutons sphériques mais sont plus économiques. |
Boutons en carbure parabolique | Conçus pour les formations tendres et dures, les boutons paraboliques offrent une solution polyvalente, équilibrant la résistance à l'usure et l'efficacité de la coupe. |
Boutons en carbure de tungstène | Les boutons biseautés conviennent mieux au forage directionnel et aux formations plus tendres. Ils permettent un contrôle précis et des taux de pénétration élevés. |
Boutons hémisphériques en carbure | Ces boutons sont conçus pour des conditions de forage difficiles et sont idéaux pour les formations dures et abrasives. |
Boutons trapézoïdaux en carbure | Les boutons trapézoïdaux offrent une combinaison de résistance à l'usure et de résistance aux chocs, adaptée aux formations dures. |
Boutons en carbure de Pyramide | Les boutons pyramidaux sont idéaux pour briser des surfaces extrêmement dures et offrent une résistance supérieure aux chocs. |
Boutons en carbure en forme de balle | Les boutons en forme de balle sont utilisés pour le forage profond dans des formations dures, offrant une excellente résistance à l'usure et une grande durabilité. |
Boutons en carbure de tungstène | Ces boutons sont idéaux pour le perçage à usage général, offrant un équilibre entre la ténacité et la résistance à l'usure. |
Comme vous pouvez le constater, la forme et la conception d'un bouton en carbure jouent un rôle crucial dans ses performances. Le bon choix peut faire la différence entre une opération réussie et un échec coûteux.
Applications des boutons en carbure
Les boutons en carbure sont les chevaux de bataille de nombreuses industries, employés dans des tâches qui exigent une résistance et une précision extrêmes. Examinons les principales applications dans lesquelles ces petits composants puissants se distinguent.
Applications courantes des boutons en carbure
Application | L'industrie | Fonction |
---|---|---|
Forage de roches | Exploitation minière | Les boutons en carbure sont utilisés dans les trépans pour le forage des roches, offrant durabilité et résistance à l'usure. |
Forage de pétrole et de gaz | Pétrole et gaz | Dans les forages pétroliers et gaziers, les boutons en carbure aident à percer les formations rocheuses difficiles. |
Outils de coupe des métaux | Fabrication | Utilisés dans les outils de coupe, les boutons en carbure offrent précision et longévité dans le travail des métaux. |
Construction de routes | La construction | Dans la construction routière, les boutons en carbure sont utilisés dans les outils de coupe pour l'asphalte et le béton. |
Chasse-neige | Maintenance municipale | Les boutons en carbure sont intégrés dans les lames de chasse-neige pour améliorer la résistance à l'usure lors du déneigement des routes. |
Travail du bois | Charpenterie | Utilisés dans les outils de coupe, les boutons en carbure fournissent des arêtes tranchantes qui durent plus longtemps que les outils en acier. |
Matériel forestier | Sylviculture | Les boutons en carbure sont utilisés dans les outils de coupe pour la sylviculture afin de garantir leur durabilité et leur tranchant. |
Machines agricoles | Agriculture | Dans les machines agricoles, les boutons en carbure sont utilisés dans les équipements de labourage pour une meilleure pénétration dans le sol. |
Pièces d'usure dans les machines lourdes | Matériel lourd | Les boutons en carbure améliorent la résistance à l'usure des composants des machines lourdes. |
Applications de défense | Défense | Utilisés dans les munitions perforantes, les boutons en carbure assurent la pénétration et la durabilité. |
Du perçage à la coupe, la polyvalence des boutons en carbure en fait un élément indispensable dans de nombreuses industries. Leur capacité à maintenir leurs performances dans des conditions extrêmes est inégalée par d'autres matériaux.
Propriétés matérielles des Boutons en carbure
Les boutons en carbure ne sont pas seulement durs : ils possèdent une combinaison unique de propriétés qui les rend aptes à des applications difficiles. Voyons ce qui distingue ces composants.
Principales propriétés des matériaux
Propriété | Description |
---|---|
Dureté | Les boutons en carbure sont extrêmement durs, généralement entre 85 et 95 HRA, ce qui les rend idéaux pour les applications de coupe, de forage et de résistance à l'usure. |
Solidité | Malgré leur dureté, les boutons en carbure sont résistants, capables de supporter des forces d'impact élevées sans se briser. |
Résistance à l'usure | Ils présentent une excellente résistance à l'usure, ce qui prolonge la durée de vie des outils et réduit les temps d'arrêt. |
Résistance à la compression | Les boutons en carbure peuvent résister à des forces de compression extrêmement élevées, ce qui est crucial pour le perçage et la coupe dans des matériaux résistants. |
Stabilité thermique | Les boutons en carbure conservent leurs propriétés à haute température, ce qui est essentiel dans les applications impliquant une chaleur intense, telles que la coupe de métaux ou le forage de roches. |
Résistance à la corrosion | Ils résistent mieux à la corrosion que de nombreux autres métaux, ce qui accroît leur longévité dans les environnements difficiles. |
La fragilité | Bien que les boutons en carbure soient résistants, ils peuvent être fragiles dans certaines conditions, par exemple lorsqu'ils sont soumis à une contrainte de traction. |
Ces propriétés rendent les boutons en carbure incroyablement fiables pour les applications exigeantes. Cependant, il est essentiel de comprendre ces propriétés pour choisir le bouton en carbure qui convient à vos besoins spécifiques.
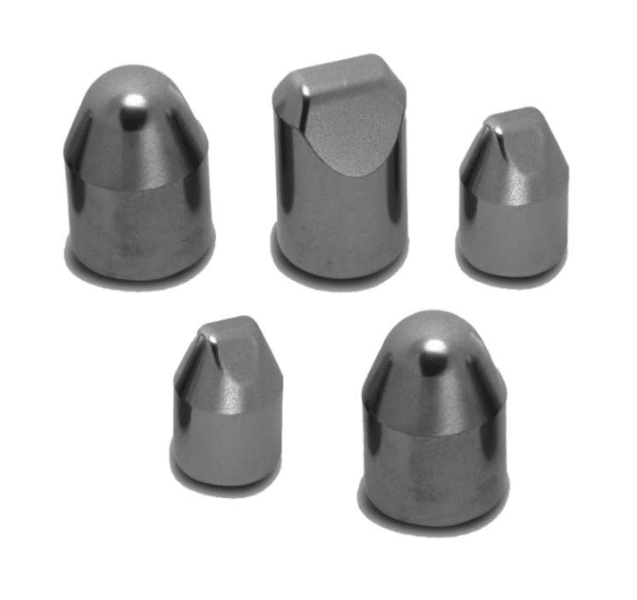
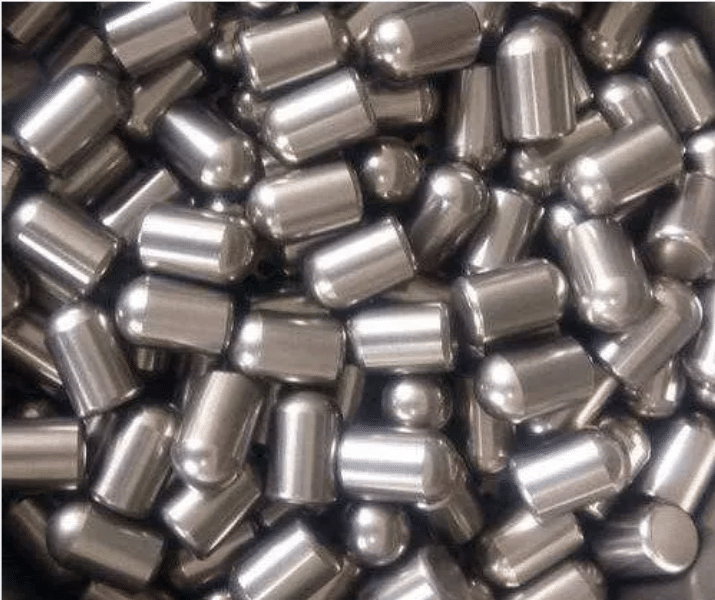
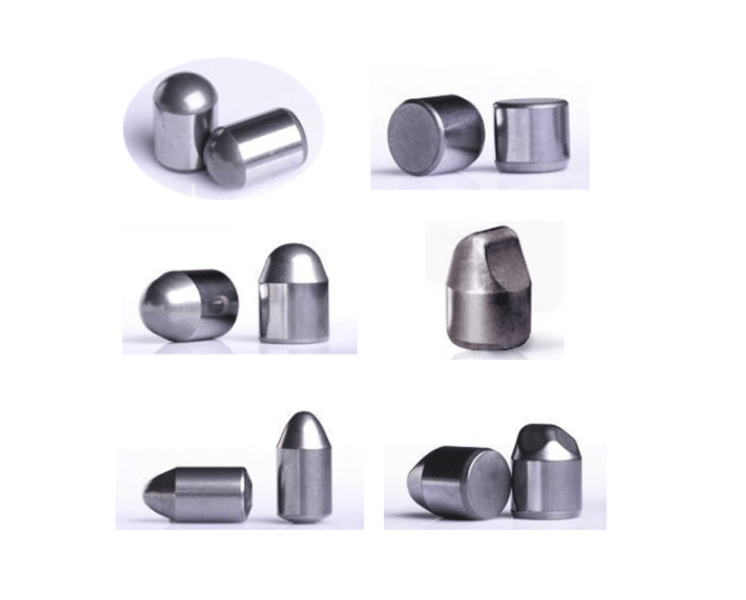
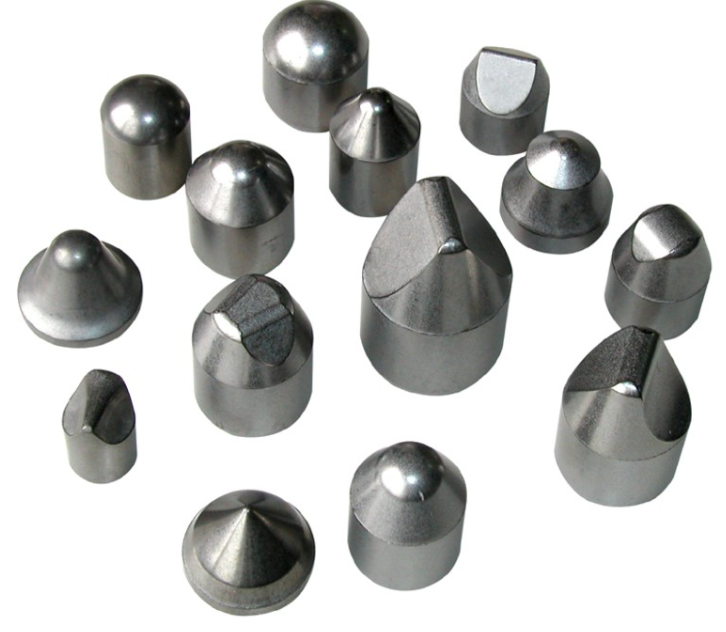
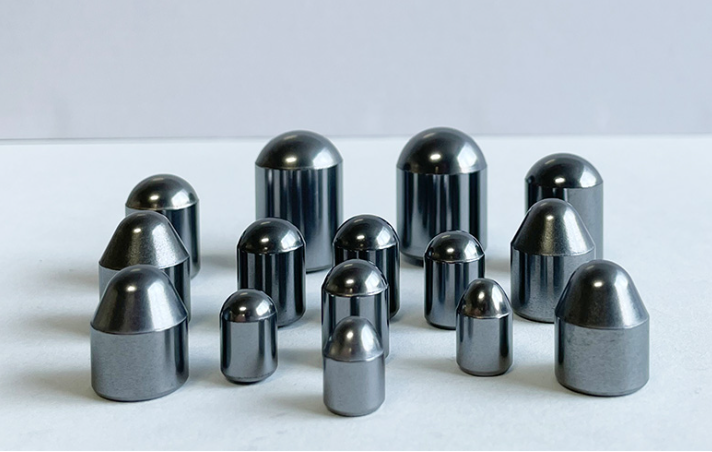
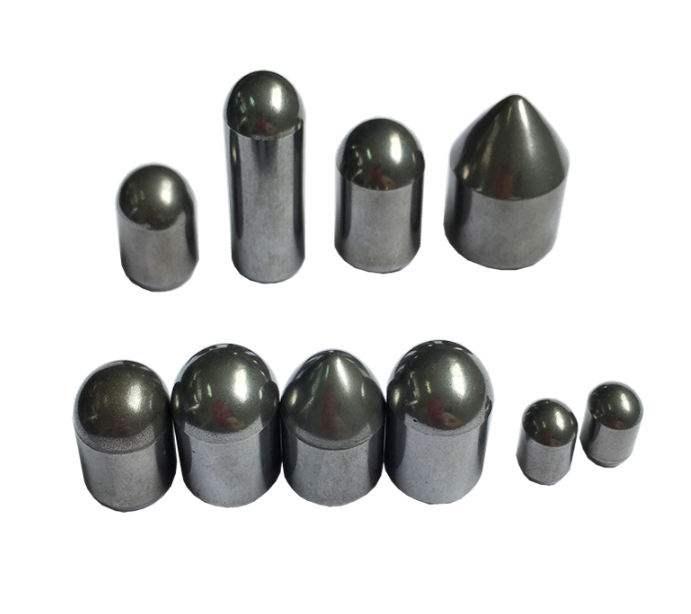
Composition des boutons en carbure
C'est la composition des boutons en carbure qui leur confère leurs propriétés exceptionnelles. En général, ces composants sont constitués de particules de carbure de tungstène liées à un liant métallique, tel que le cobalt ou le nickel.
Composition typique des boutons en carbure
Composant | Rôle |
---|---|
Carbure de tungstène (WC) | C'est le composant principal qui assure la dureté et la résistance à l'usure. |
Cobalt (Co) | Agit comme un liant qui maintient les particules de carbure de tungstène ensemble et leur confère de la ténacité. |
Nickel (Ni) | Un liant alternatif utilisé lorsque la résistance à la corrosion est nécessaire. |
Poudres de carbure | Peut inclure d'autres carbures comme le carbure de titane (TiC) ou le carbure de tantale (TaC) pour modifier les propriétés telles que la ténacité ou la résistance à l'usure. |
Additifs | De petites quantités d'autres éléments peuvent être ajoutées pour améliorer des propriétés spécifiques, telles que des inhibiteurs de croissance du grain ou des éléments résistants à la corrosion. |
En modifiant la composition, les fabricants peuvent adapter les propriétés des boutons en carbure aux besoins de différentes applications. Cette personnalisation est cruciale dans les industries où la précision et les performances sont essentielles.
Dureté, solidité et résistance à l'usure des boutons en carbure
La combinaison de la dureté, de la solidité et de la résistance à l'usure fait des boutons en carbure les favoris des industries qui exigent durabilité et fiabilité. Examinons ces aspects.
Comprendre la dureté, la solidité et la résistance à l'usure
Caractéristique | Description |
---|---|
Dureté | Mesurée sur l'échelle de Rockwell, la dureté indique la résistance du matériau à la déformation. Les boutons en carbure ont généralement une dureté comprise entre 85 et 95 HRA, ce qui garantit une grande durabilité. |
La force | Les boutons en carbure possèdent une résistance élevée à la compression, ce qui est crucial pour le perçage et la coupe dans des matériaux résistants. |
Résistance à l'usure | Leur capacité à résister à l'usure garantit une longue durée de vie, ce qui réduit la fréquence des remplacements et les temps d'arrêt. |
Ces caractéristiques font des boutons en carbure un choix de premier ordre pour les applications lourdes. Cependant, le choix du bon équilibre entre ces propriétés est essentiel pour optimiser les performances dans votre application spécifique.
Spécifications, tailles, formes et normes pour Boutons en carbure
Les boutons en carbure sont disponibles dans une grande variété de tailles, de formes et de spécifications afin de répondre aux divers besoins des différentes industries. La normalisation garantit la compatibilité et les performances.
Spécifications, tailles et formes courantes
Spécifications | Détails |
---|---|
Tailles | La taille des boutons en carbure varie en fonction de l'application, de quelques millimètres de diamètre pour les petits outils de coupe à plusieurs centimètres pour les forets industriels. |
Formes | Les formes les plus courantes sont les suivantes : sphérique, conique, plate, parabolique, ciselée, hémisphérique, trapézoïdale, pyramidale, en forme de balle et en forme de dôme. |
Normes | Les normes internationales telles que l'ISO et l'ANSI garantissent la cohérence de la qualité et des performances entre les différents fabricants. |
Tolérances | La précision est essentielle, des tolérances étroites étant souvent requises, en particulier dans les industries à fort enjeu telles que l'aérospatiale ou la fabrication automobile. |
Le choix de la bonne taille, de la bonne forme et de la bonne spécification est essentiel pour garantir une performance et une longévité optimales dans votre application spécifique.
Sélection du bon bouton en carbure
Choisir le bon bouton en carbure ne consiste pas seulement à choisir l'option la plus dure ou la plus résistante à l'usure - il s'agit d'adapter les propriétés du bouton aux besoins spécifiques de votre application.
Facteurs à prendre en compte lors du choix d'un bouton en carbure
Facteur | Description |
---|---|
Application | Tenez compte de l'application spécifique - qu'il s'agisse de forage, de coupe ou de protection contre l'usure - car des applications différentes requièrent des propriétés différentes. |
Matière à travailler | La dureté et l'abrasivité du matériau sur lequel vous travaillez déterminent le bouton en carbure approprié. |
Conditions de fonctionnement | La température, la pression et les conditions environnementales doivent influencer votre choix. |
Coût et performance | Bien que les boutons en carbure puissent être plus chers que d'autres matériaux, leur longévité et leurs performances justifient souvent le coût dans les applications exigeantes. |
Réputation du fabricant | Tenez compte de la réputation du fabricant, car la qualité peut varier considérablement d'un fournisseur à l'autre. |
Faire le bon choix peut permettre d'améliorer les performances, de réduire les coûts et d'allonger la durée de vie des outils.
Comparaison des boutons en carbure : Avantages et limites
Si les boutons en carbure offrent de nombreux avantages, ils présentent également certaines limites. Les comprendre peut vous aider à prendre une décision en connaissance de cause.
Avantages et limites
Aspect | Avantages | Limites |
---|---|---|
Dureté | La dureté supérieure garantit des performances durables dans les applications de coupe et de forage. | Une dureté élevée peut également les rendre cassants dans certaines conditions. |
Résistance à l'usure | L'excellente résistance à l'usure réduit les temps d'arrêt et le besoin de remplacements fréquents. | Dans certaines compositions, la résistance à l'usure peut se faire au détriment de la ténacité. |
Solidité | Les boutons en carbure sont suffisamment robustes pour résister à des forces d'impact élevées. | Dans des conditions très exigeantes, la ténacité peut être insuffisante, ce qui entraîne des ébréchures ou des ruptures. |
Coût | Bien que plus coûteux au départ, leur durabilité permet souvent de réaliser des économies au fil du temps. | Le coût initial plus élevé peut constituer un obstacle, en particulier pour les petites entreprises ou les applications moins exigeantes. |
Polyvalence | Disponibles dans une large gamme de formes, de tailles et de compositions pour répondre à différentes applications. | La variété peut rendre difficile le choix du bon type sans connaissances ou conseils appropriés. |
Comprendre ces facteurs vous permet de peser le pour et le contre et de faire un choix plus éclairé, adapté à vos besoins spécifiques.
Fournisseurs et prix des boutons en carbure
Le marché des boutons en carbure est vaste et de nombreux fournisseurs proposent une gamme de produits. Nous allons ici mettre en avant quelques fournisseurs connus et donner un aperçu des prix.
Principaux fournisseurs et aperçu des prix
Fournisseur | Région | Gamme de produits | Tarification |
---|---|---|---|
Kennametal | Mondial | Offre une large gamme de boutons en carbure, en particulier pour les applications minières et de forage. | Les prix varient en fonction de la taille, de la forme et de la composition, généralement entre $10 et $100 par bouton. |
Sandvik | Europe, Amériques | Renommée pour ses produits en carbure de haute qualité, notamment ses boutons pour le forage des roches et la coupe des métaux. | Des prix compétitifs axés sur des produits de haute performance, généralement de $20 à $150 par bouton. |
Carbure cémenté de Zhuzhou | Asie | Un fournisseur majeur en Chine, offrant une variété de boutons en carbure à des prix inférieurs. | Options plus abordables, allant souvent de $5 à $50 par bouton, en fonction des spécifications. |
Alliage lourd de tungstène | Amérique du Nord | Spécialisée dans la fabrication de boutons en carbure sur mesure pour des applications de niche, avec un accent particulier sur la qualité. | Les commandes personnalisées peuvent varier considérablement en prix, généralement à partir de $30 par bouton. |
Ingersoll Rand | Mondial | Offre une variété de produits industriels, y compris des boutons en carbure pour les machines lourdes. | Des prix élevés, souvent justifiés par la longévité et la performance de leurs produits, avec des prix allant de $50 à $200 par bouton. |
Le choix d'un fournisseur implique de trouver un équilibre entre la qualité, le coût et le service. Il est essentiel de tenir compte non seulement du prix, mais aussi de la réputation et de la fiabilité du fournisseur.
Comment choisir le bon bouton en carbure
Choisir le bouton en carbure idéal pour votre application peut sembler insurmontable, compte tenu de la multitude d'options disponibles. Mais n'ayez crainte, nous avons quelques conseils pratiques pour vous aider à faire le bon choix.
Étapes à suivre pour choisir le bon bouton en carbure
Étape | Description |
---|---|
Identifier l'application | Commencez par comprendre clairement l'application spécifique et les exigences qu'elle impose au bouton en carbure. |
Évaluer le matériel | Tenez compte de la dureté et de l'abrasivité du matériau avec lequel vous allez travailler, car cela influencera le type de bouton en carbure dont vous avez besoin. |
Tenir compte des conditions | Évaluer les conditions de fonctionnement, telles que la température, la pression et les facteurs environnementaux, qui peuvent affecter les performances du bouton en carbure. |
Consulter des experts | N'hésitez pas à consulter des fournisseurs ou des experts du secteur qui peuvent vous donner des conseils fondés sur leur expérience et leur connaissance des produits. |
Tester avant de valider | Si possible, testez un petit lot de boutons en carbure pour votre application avant de vous engager dans un achat important. Vous éviterez ainsi des erreurs coûteuses. |
Évaluer le coût par rapport à la longévité | Comparez le coût initial du bouton en carbure à sa longévité et à ses performances attendues. Parfois, une option plus coûteuse permet de réaliser des économies à long terme. |
En suivant ces étapes, vous pouvez vous assurer que vous choisissez un bouton en carbure qui non seulement répond à vos besoins, mais qui offre également la meilleure valeur pour votre investissement.
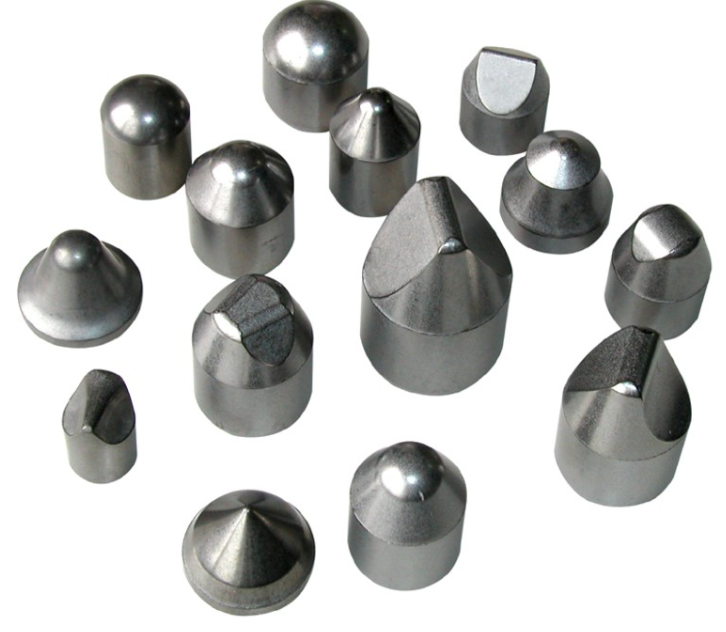
FAQ
Question | Réponse |
---|---|
En quoi sont faits les boutons en carbure ? | Les boutons en carbure sont généralement constitués de particules de carbure de tungstène liées à un liant métallique, tel que le cobalt ou le nickel. |
Pourquoi les boutons en carbure sont-ils utilisés dans le forage ? | Leur dureté exceptionnelle et leur résistance à l'usure font des boutons en carbure des outils idéaux pour pénétrer les formations rocheuses difficiles sans s'user rapidement. |
Comment choisir le bon bouton en carbure ? | Tenez compte de l'application, du matériau, des conditions d'utilisation et consultez des experts pour trouver la solution la mieux adaptée à vos besoins. |
Les boutons en carbure sont-ils chers ? | Bien qu'ils puissent être plus coûteux au départ, leur durabilité permet souvent de réaliser des économies au fil du temps, en particulier dans les applications exigeantes. |
Les boutons en carbure peuvent-ils être utilisés pour la coupe des métaux ? | Oui, les boutons en carbure sont couramment utilisés dans les outils de coupe des métaux en raison de leur capacité à maintenir une arête vive et à résister à l'usure. |
Quelle est la durée de vie des boutons en carbure ? | La durée de vie d'un bouton en carbure dépend de l'application et des conditions, mais ils durent généralement beaucoup plus longtemps que d'autres matériaux dans des rôles similaires. |
Quelles sont les formes des boutons en carbure ? | Ils se présentent sous différentes formes : sphérique, conique, plate, parabolique, ciselée, hémisphérique, trapézoïdale, pyramidale, en forme de balle et en forme de dôme. |
Les différentes compositions ont-elles une incidence sur les performances ? | Oui, la composition du bouton de carbure, y compris le type de liant et d'additifs, peut affecter de manière significative ses performances dans différentes applications. |
Les boutons en carbure peuvent-ils résister à la corrosion ? | Selon leur composition, certains boutons en carbure, en particulier ceux contenant des liants en nickel, offrent une bonne résistance à la corrosion. |
Où puis-je acheter des boutons en carbure ? | Les boutons en carbure peuvent être achetés auprès de divers fournisseurs dans le monde, notamment auprès de grandes entreprises telles que Kennametal, Sandvik et Zhuzhou Cemented Carbide. |
Conclusion
Boutons en carbure Les boutons en carbure de tungstène sont un élément crucial dans les industries qui ont besoin d'outils capables de résister à des conditions extrêmes. Qu'il s'agisse de forer la roche ou de couper le métal, le choix du bon bouton en carbure peut avoir un impact significatif sur l'efficacité, la rentabilité et le succès de votre opération. En comprenant les différents types, les propriétés des matériaux et les facteurs qui influencent leurs performances, vous pouvez prendre des décisions éclairées qui profiteront à votre travail sur le long terme.