L'importance du carbure pour les outils de précision
Outils en carbure sont les héros méconnus de l'ingénierie de précision. Imaginez que vous essayez de sculpter un chef-d'œuvre avec un ciseau émoussé ou de couper des légumes avec un couteau émoussé. C'est frustrant et inefficace, n'est-ce pas ? C'est là qu'interviennent les outils en carbure, qui sont des outils de travail tranchants et fiables dans des secteurs allant de l'aérospatiale au travail du bois.
Qu'est-ce qui rend le carbure indispensable ? C'est une question de précision et de durabilité. Les outils en carbure conservent leur tranchant plus longtemps que les autres matériaux, ce qui garantit la précision dans les applications à fort enjeu. Qu'il s'agisse de créer des moules complexes ou d'usiner des composants métalliques résistants, les outils en carbure offrent une précision inégalée. Voyons plus en détail ce qui rend ce matériau si spécial.
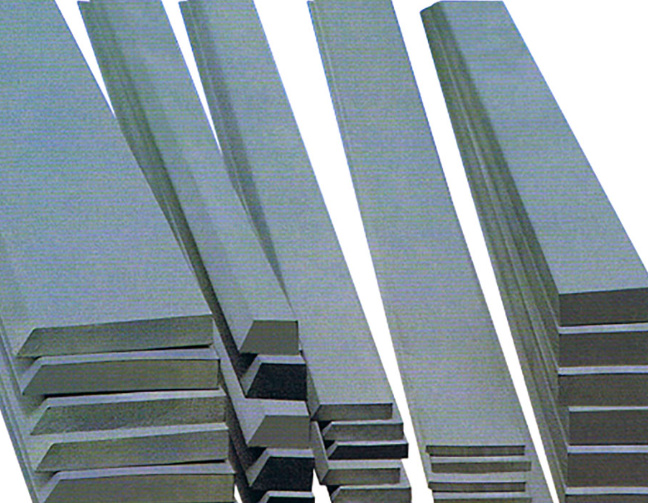
Qu'est-ce que le carbure pour les outils de précision ?
Le carbure est un matériau composite composé principalement de carbure de tungstène et d'un liant, généralement du cobalt. Il s'agit d'un matériau hybride qui offre le meilleur des deux mondes : la dureté des céramiques et la résistance des métaux. Les particules de carbure de tungstène sont semblables à de minuscules diamants, ce qui confère au matériau une dureté incroyable, tandis que le liant métallique maintient ces particules ensemble, ce qui leur confère une plus grande solidité.
Pourquoi cela est-il important ? Parce que c'est cette combinaison unique qui permet au carbure de résister à l'usure extrême de la coupe, du meulage et du perçage. Il n'est pas exagéré de dire que le carbure est l'épine dorsale de la fabrication moderne.
Ingrédients du carbure pour les outils de précision
C'est la composition du carbure qui lui confère ses superpouvoirs. Voyons cela de plus près :
- Carbure de tungstène (WC) : Il s'agit de l'ingrédient principal, qui représente 70-97% du matériau. Il est incroyablement dur, se classant juste en dessous du diamant sur l'échelle de Mohs.
- Cobalt (Co) : Un liant métallique qui maintient les particules de carbure de tungstène ensemble. Il est responsable de la ténacité du matériau.
- Autres additifs : Des éléments tels que le titane, le tantale ou le vanadium sont parfois ajoutés pour améliorer des propriétés spécifiques, telles que la résistance à la chaleur ou à la corrosion.
La recette exacte varie en fonction de l'application prévue de l'outil. Par exemple, les outils utilisés pour l'usinage à grande vitesse peuvent avoir une teneur en cobalt plus élevée pour une meilleure résistance.
Avantages de la Carbure pour les outils de précision
Fonctionnalité | Avantage |
---|---|
Dureté | Conserve les bords tranchants plus longtemps, réduisant ainsi les temps d'arrêt pour l'affûtage. |
Résistance à l'usure | Gère facilement les environnements à fort coefficient de frottement. |
Résistance à la chaleur | Il est performant dans les applications à haute température sans perdre de sa résistance. |
Solidité | Résiste à l'écaillage et à la fissuration sous de lourdes charges. |
Polyvalence | Convient à une large gamme d'applications, de la coupe au meulage. |
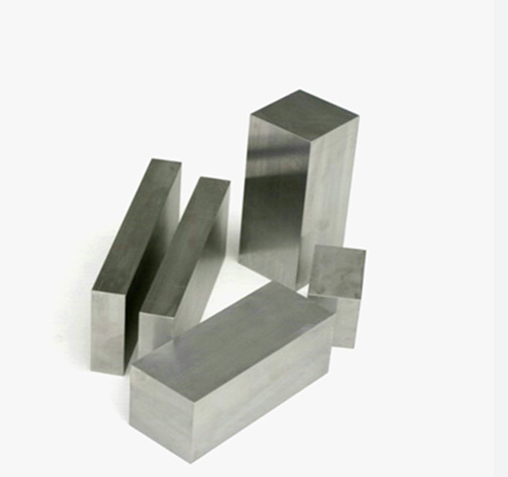
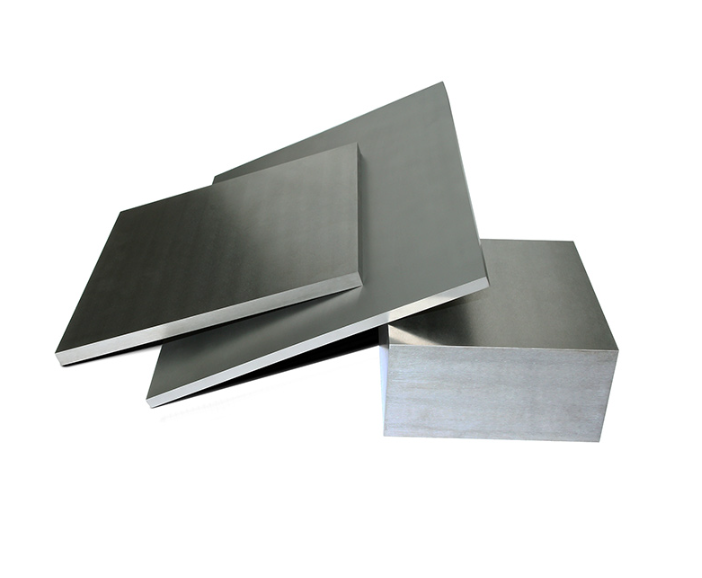
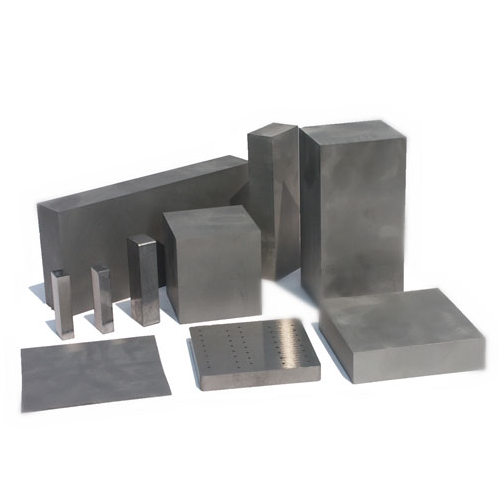
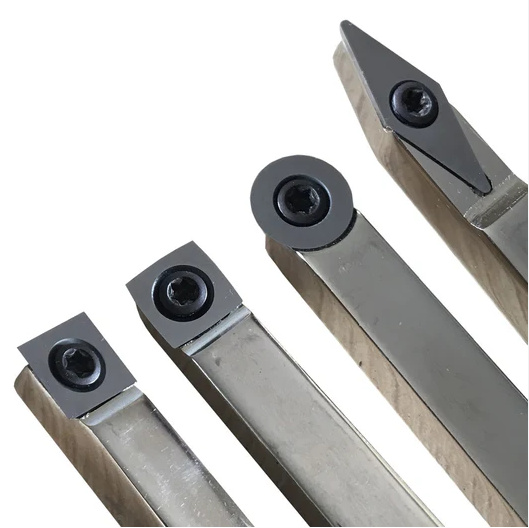
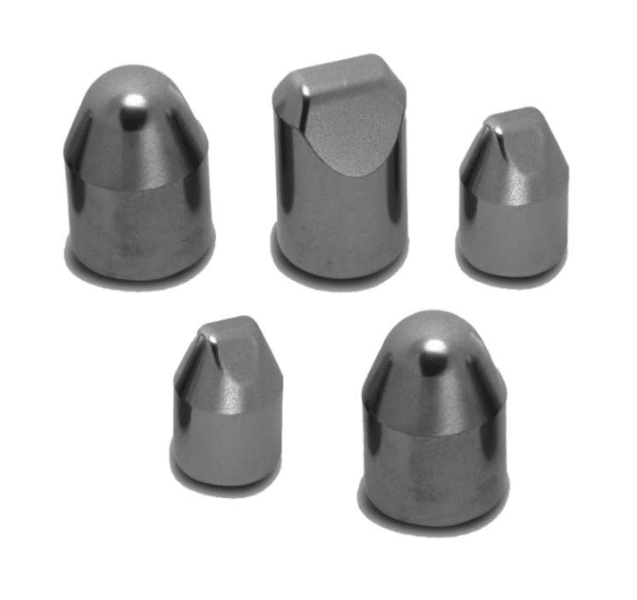
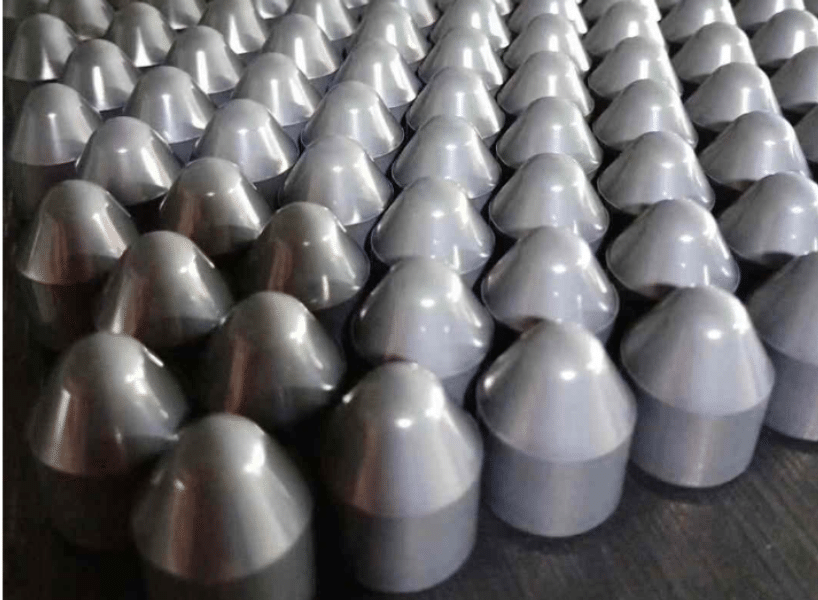
Applications des outils de précision en carbure
L'industrie | Application |
---|---|
Aérospatiale | Usinage d'alliages légers à haute résistance. |
Automobile | Fabrication de composants de moteurs et de pièces de transmission. |
Travail des métaux | Opérations de coupe, de perçage et de fraisage. |
Travail du bois | Créer des finitions lisses sur les bois durs et les bois tendres. |
Exploitation minière | Forage et excavation de roches. |
Comparaison : Carbure vs. autres matériaux d'outils
Lorsqu'il s'agit de matériaux pour outils, le carbure arrive souvent en tête, mais comparons-le à d'autres matériaux courants :
Carbure et acier rapide (HSS)
- Dureté : Le carbure est nettement plus dur que l'acier rapide, ce qui le rend plus adapté aux applications de haute précision.
- Durabilité : Les outils en carbure durent plus longtemps, ce qui réduit la nécessité de les remplacer fréquemment.
- Coût : Si le carbure est plus cher au départ, sa longévité le rend souvent plus rentable à long terme.
Outils en carbure ou en céramique
- La robustesse : Le carbure est plus résistant que la céramique et moins susceptible de s'écailler ou de se fissurer.
- Polyvalence : Le carbure donne de bons résultats dans une plus large gamme d'applications, y compris celles qui impliquent des charges lourdes.
- Résistance à la chaleur : Alors que les céramiques peuvent supporter des températures plus élevées, le carbure offre un meilleur équilibre entre la résistance à la chaleur et la ténacité.
Conseils pour choisir les bons outils en carbure
Choisir le bon outil en carbure peut ressembler à choisir le bon mélange de café - il y a tellement d'options ! Voici ce qu'il faut prendre en compte :
- Matériau usiné : Travaillez-vous avec du bois, du métal ou des matériaux composites ? La qualité et la géométrie de l'outil doivent être adaptées au matériau.
- Type d'application : Qu'il s'agisse de couper, de percer ou de meuler, il existe un outil spécifique conçu pour ce travail.
- Revêtement : Les outils dotés de revêtements tels que TiN (nitrure de titane) ou TiAlN (nitrure de titane et d'aluminium) offrent des performances accrues dans les applications à haute température.
- Réputation de la marque : Privilégiez les marques réputées pour leur qualité constante.
- Coût et longévité : Ne vous contentez pas de regarder le prix ; tenez compte de la durée de vie de l'outil et de la valeur qu'il offre.
Comment choisir Carbure Affûtage d'outils
L'affûtage des outils en carbure est un art et une science. Voici comment le faire correctement :
- Comprendre la géométrie de l'outil : Les outils en carbure ont des angles et des géométries spécifiques qui doivent être conservés pendant l'affûtage.
- Utiliser le bon équipement : Les meules diamantées sont essentielles pour l'affûtage des outils en carbure. Les meules ordinaires ne suffisent pas - littéralement !
- Gardez la tête froide : La surchauffe peut endommager le carbure. Utilisez un liquide de refroidissement pour éviter cela.
- Vérifier la présence de fissures : Inspectez l'outil pour vérifier qu'il n'est pas endommagé avant de l'affûter. Un outil fissuré peut être dangereux à utiliser.
- Engagez un professionnel : Si vous n'êtes pas sûr de vous, envisagez de faire appel à un service d'affûtage professionnel. L'investissement en vaut souvent la peine.
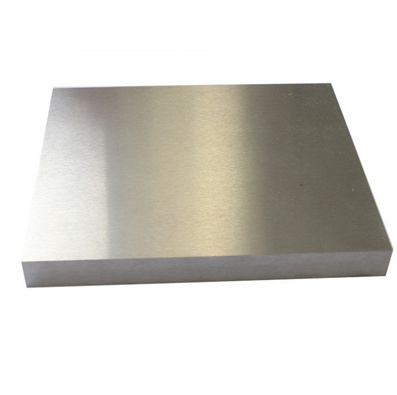
FAQ
Question | Réponse |
---|---|
Quelle est la meilleure méthode pour affûter les outils en carbure ? | Utilisez une meule diamantée pour un affûtage précis et efficace. |
Quelle est la fréquence d'affûtage des outils en carbure ? | Cela dépend de l'utilisation, mais généralement après un ternissement notable ou une baisse des performances. |
Puis-je affûter des outils en carbure à la maison ? | Oui, avec l'équipement et les compétences adéquats, mais des services professionnels garantissent de meilleurs résultats. |
Quelles sont les erreurs courantes en matière d'affûtage ? | Surchauffe, utilisation d'angles incorrects ou d'équipements inadaptés. |
Tous les outils en carbure doivent-ils être affûtés ? | Pas tous : certains sont conçus pour être jetés après avoir été portés. |