Lorsqu'il s'agit de précision, de durabilité et d'efficacité dans l'usinage, outils en carbure sont les héros méconnus du monde de la fabrication. Qu'il s'agisse de façonner le métal, de sculpter le bois ou de percer des matériaux résistants, les outils en carbure sont le choix de prédilection des professionnels qui exigent ce qu'il y a de mieux. Mais qu'est-ce qui les rend si spéciaux ? Pourquoi sont-ils préférés aux outils traditionnels en acier rapide ? Et comment pouvez-vous vous assurer que vous tirez le meilleur parti de vos outils en carbure ?
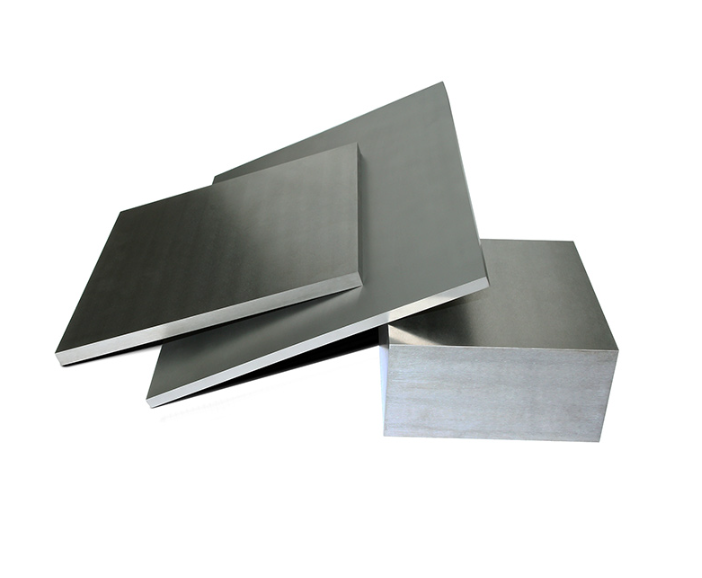
Scénarios d'application des outils de coupe en alliage dur
Les outils en carbure, également connus sous le nom d'outils de coupe en alliage dur, sont utilisés dans un large éventail d'industries. De la construction automobile à l'ingénierie aérospatiale, ces outils sont indispensables. Voyons les choses en détail :
- Industrie automobile: Pensez à la précision requise pour fabriquer des composants de moteur, des engrenages et des systèmes de freinage. Les outils en carbure sont utilisés pour fraiser, tourner et percer ces pièces avec une précision inégalée.
- Industrie aérospatiale: Lorsque vous travaillez avec des matériaux tels que le titane ou l'Inconel, vous avez besoin d'un outil capable de supporter une chaleur et une pression extrêmes. Les outils en carbure sont à la hauteur de la tâche, garantissant des finitions lisses et des tolérances serrées.
- Travail du bois: Oui, les outils en carbure ne sont pas réservés au métal ! Ils sont également utilisés dans le travail du bois pour couper, façonner et sculpter les bois durs.
- Industrie médicale: Les instruments chirurgicaux et les implants nécessitent un usinage de précision, ce que les outils en carbure permettent de réaliser.
- La construction: Percer le béton ou couper des barres d'armature ? Les outils à pointe carbure sont la meilleure solution.
En bref, s'il s'agit d'un travail difficile, précis et qui doit être bien fait, il est probable que des outils en carbure soient utilisés.
L'impact de la durée de vie des outils sur l'efficacité et le coût de la production
Avez-vous déjà entendu le dicton "Le temps, c'est de l'argent" ? Dans le secteur de la fabrication, la durée de vie des outils est de l'argent. Plus votre outils en carbure moins vous aurez d'interruptions dans votre chaîne de production. Voici pourquoi la durée de vie des outils est importante :
- Réduction des temps d'arrêt: Les changements fréquents d'outils impliquent un arrêt de la production, ce qui coûte du temps et de l'argent. Les outils en carbure durent beaucoup plus longtemps que les outils traditionnels en acier, ce qui permet à votre ligne de production de fonctionner sans heurts.
- Économies de coûts: Bien que les outils en carbure aient un coût initial plus élevé, leur durée de vie prolongée vous permet d'économiser de l'argent à long terme. Moins de remplacements = moins de coûts.
- Cohérence: L'usure des outils peut nuire à la qualité de votre travail. Les outils en carbure conservent leur tranchant plus longtemps, ce qui garantit des résultats constants tout au long de leur durée de vie.
Par conséquent, si vous cherchez à améliorer votre efficacité et à réduire vos coûts, investir dans des outils en carbure de haute qualité est une évidence.
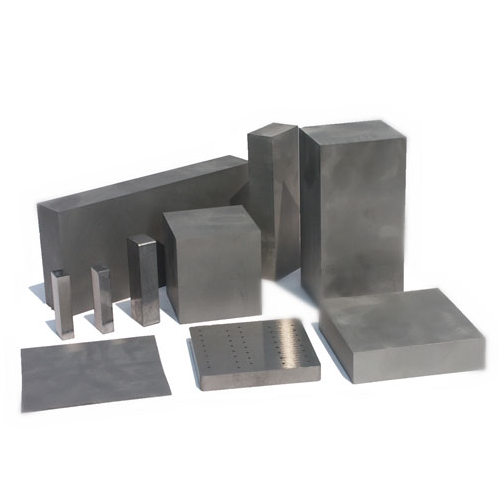
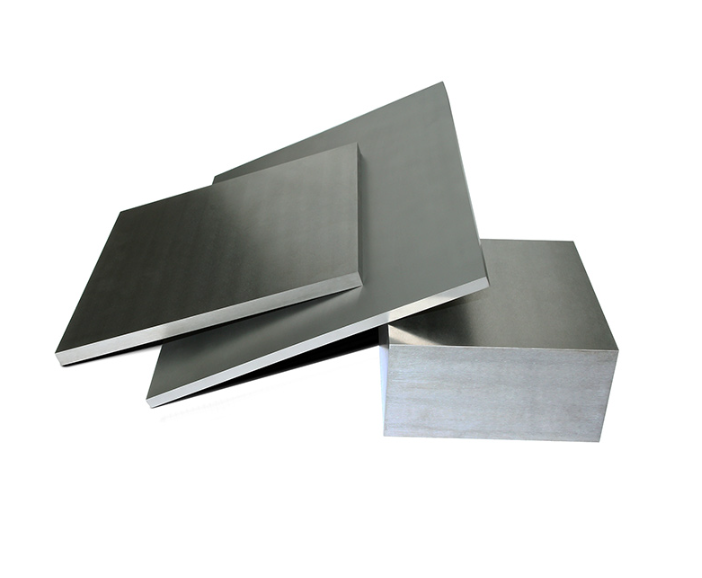
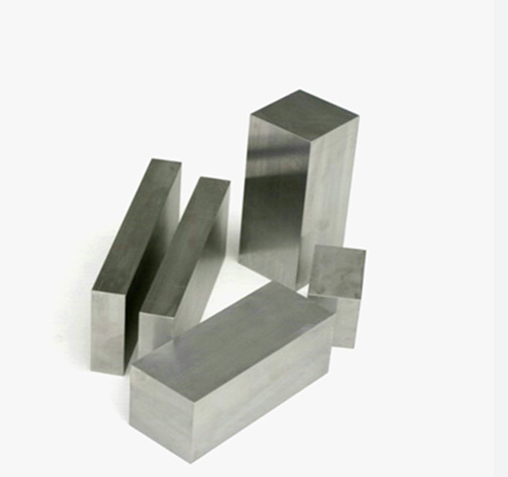
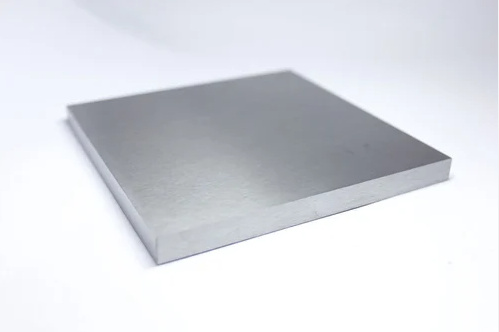
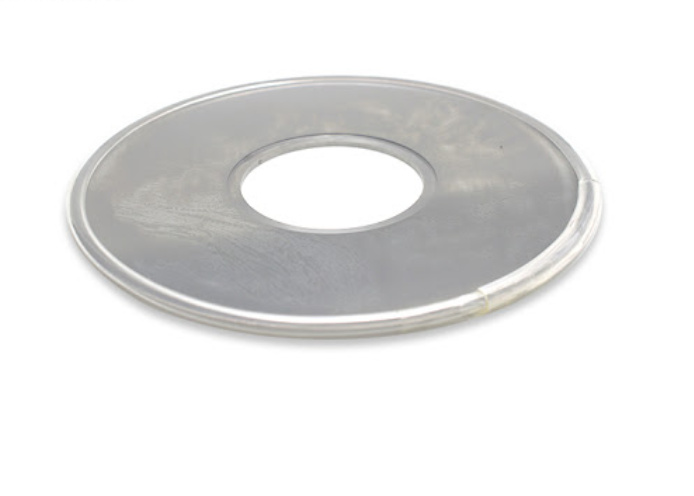
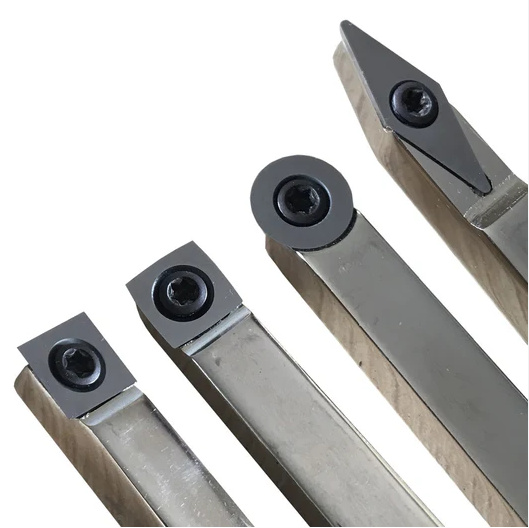
Facteurs influençant la durée de vie de l'enfant Outils en carbure
Tous les outils en carbure ne sont pas identiques et leur durée de vie peut varier en fonction de plusieurs facteurs. Voici ce qu'il faut savoir :
- Matériau usiné: Les matériaux plus durs comme l'acier inoxydable ou le titane usent les outils plus rapidement que les matériaux plus tendres comme l'aluminium.
- Vitesse de coupe et vitesse d'avance: Pousser vos outils trop fort peut entraîner une usure prématurée. Il est essentiel de trouver le bon équilibre.
- Utilisation du liquide de refroidissement: Un refroidissement adéquat peut considérablement prolonger la durée de vie de l'outil en réduisant l'accumulation de chaleur.
- Géométrie de l'outil: La conception de l'outil, y compris ses angles et ses revêtements, joue un rôle important dans sa durée de vie.
- Compétences de l'opérateur: Même les meilleurs outils peuvent être abîmés par une mauvaise utilisation. La formation de votre équipe est essentielle.
En comprenant ces facteurs, vous pouvez prendre des mesures pour maximiser la durée de vie de vos outils en carbure.
Comment prolonger la durée de vie des outils en carbure
Conseil | Explication |
---|---|
Utiliser les bons paramètres de coupe | Régler la vitesse, l'avance et la profondeur de coupe en fonction du matériau et du type d'outil. |
Appliquer correctement le liquide de refroidissement | Réduire la chaleur et la friction pour éviter l'usure des outils. |
Inspecter régulièrement les outils | Détecter rapidement les signes d'usure pour éviter une défaillance catastrophique. |
Ranger correctement les outils | Conservez les outils dans un environnement sec et organisé pour éviter qu'ils ne s'abîment. |
Utiliser des outils en carbure de haute qualité | Investissez dans des marques et des modèles réputés pour de meilleures performances et une plus grande longévité. |
Types courants d'usure des outils en carbure et mesures correspondantes
Type d'usure | Causes | Mesures préventives |
---|---|---|
Usure des flancs | Friction entre l'outil et la pièce | Utilisez le liquide de refroidissement approprié et réglez la vitesse de coupe. |
Usure du cratère | Températures élevées et réactions chimiques | Choisissez des outils dotés d'un revêtement résistant à la chaleur. |
Chipping | Impacts ou vibrations pendant l'usinage | Veillez à ce que l'installation soit stable et évitez d'exercer une force excessive. |
Bordure construite | Matière collant à l'outil | Augmenter la vitesse de coupe et utiliser des outils tranchants. |
Fissuration thermique | Cycles de chauffage et de refroidissement rapides | Maintenir un débit constant du liquide de refroidissement. |
Tendances futures du carbure dans l'industrie automobile
L'industrie automobile est en constante évolution et les outils en carbure évoluent avec elle. Voici ce qui se profile à l'horizon :
- Véhicules électriques (VE): La popularité croissante des véhicules électriques entraîne une augmentation de la demande de matériaux légers tels que l'aluminium et les matériaux composites. Les outils en carbure sont adaptés pour traiter efficacement ces matériaux.
- Fabrication additive: L'impression 3D modifie la façon dont les pièces sont fabriquées, et les outils en carbure sont utilisés pour finir et affiner ces composants.
- Outils intelligents: Imaginez des outils capables de surveiller leur propre usure et de vous alerter lorsqu'ils ont besoin d'être entretenus. C'est l'avenir des outils en carbure, avec des capteurs intégrés et une connectivité IoT.
L'industrie automobile n'est qu'un exemple parmi d'autres de la manière dont les outils en carbure conservent une longueur d'avance.
Modèles de poudres métalliques spécifiques pour Outils en carbure
Lorsqu'il s'agit d'outils en carbure, les poudres métalliques utilisées pour leur fabrication sont cruciales. Voici 10 modèles spécifiques, chacun ayant des propriétés uniques :
- Carbure de tungstène (WC): Le plus courant, connu pour sa dureté et sa résistance à l'usure.
- Carbure de titane (TiC): Offre une excellente résistance à la chaleur, idéale pour l'usinage à grande vitesse.
- Carbure de tantale (TaC): Ajoute de la ténacité et est souvent utilisé en combinaison avec le WC.
- Carbure de niobium (NbC): Améliore la dureté et est utilisé dans les outils de coupe pour l'acier inoxydable.
- Carbure de vanadium (VC): Améliore la résistance à l'usure et est souvent utilisé dans les revêtements.
- Carbure de chrome (Cr3C2): Connu pour sa résistance à la corrosion, parfait pour les environnements difficiles.
- Carbure de molybdène (Mo2C): Ajoute de la résistance et est utilisé dans les applications soumises à de fortes contraintes.
- Carbure de hafnium (HfC): Extrêmement résistant à la chaleur, utilisé dans les applications aérospatiales.
- Carbure de zirconium (ZrC): Offre un équilibre entre dureté et ténacité.
- Carbure de silicium (SiC): Utilisé dans les matériaux composites pour une plus grande durabilité.
Chacune de ces poudres apporte quelque chose d'unique, ce qui permet aux fabricants d'adapter leurs outils en carbure à des besoins spécifiques.
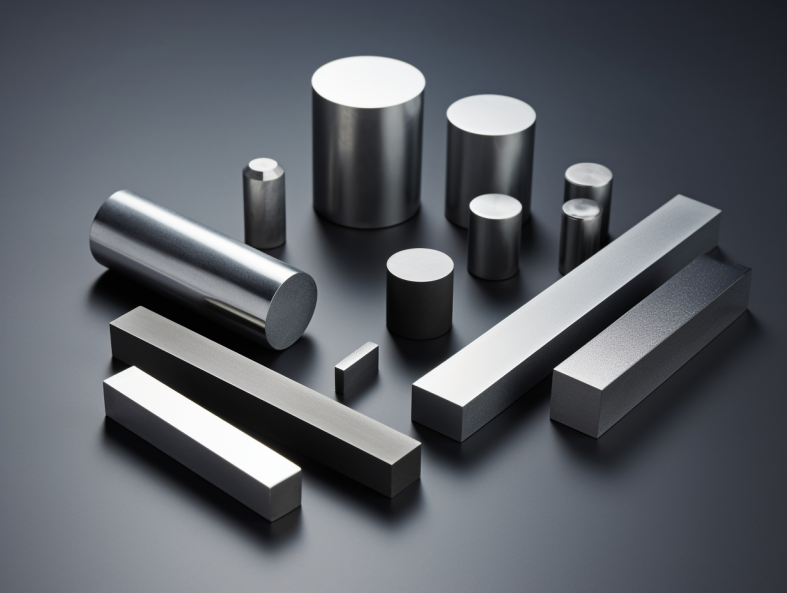
FAQ
Question | Réponse |
---|---|
De quoi sont faits les outils en carbure ? | Combinaison de carbure de tungstène et de cobalt, souvent avec d'autres additifs. |
Les outils en carbure sont-ils meilleurs que les outils en acier ? | Oui, ils sont plus durs, plus durables et conservent leur tranchant plus longtemps. |
Les outils en carbure peuvent-ils être affûtés ? | Oui, mais cela nécessite un équipement et une expertise spécialisés. |
Comment choisir le bon outil en carbure ? | Tenez compte de la matière à usiner, du type de coupe et de la géométrie de l'outil. |
Les outils en carbure sont-ils chers ? | Ils ont un coût initial plus élevé mais permettent d'économiser de l'argent à long terme. |