Carbure Les bandes - ces rubans de matériau discrets mais puissants - sont les héros méconnus d'innombrables industries. Du travail du bois et du métal à la construction et à la fabrication, ces bandes polyvalentes nous permettent de couper, de façonner et de transformer les matériaux avec une précision et une efficacité remarquables. Rejoignez-nous pour plonger dans le monde fascinant des bandes de carbure, en explorant leurs propriétés, leurs applications et les facteurs clés à prendre en compte pour choisir la bande idéale pour vos besoins.
Qu'est-ce qu'une bande de carbure ?
Les bandes de carbure sont des pièces minces et plates en carbure cémenté, un matériau composite réputé pour sa dureté et sa résistance à l'usure exceptionnelles. Ces bandes sont généralement constituées de fines particules de carbure de tungstène, un composé connu pour son extrême dureté, noyées dans une matrice de cobalt, qui agit comme un liant.
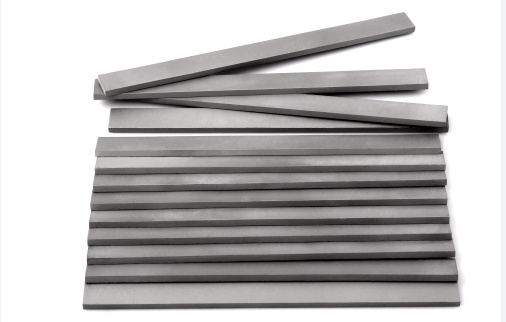
L'alchimie de la force : comment les bandes de carbure sont-elles fabriquées ?
La création de bandes de carbure est un témoignage de l'ingénierie de précision :
- Métallurgie des poudres : De fines poudres de carbure de tungstène et de cobalt sont mélangées avec précision dans des proportions spécifiques pour obtenir les propriétés souhaitées.
- Pressage et mise en forme : Le mélange de poudres est ensuite pressé dans la forme souhaitée à l'aide de moules spécialisés et sous haute pression.
- Frittage : Les bandes pressées subissent un processus de frittage à haute température dans une atmosphère contrôlée. Pendant le frittage, le liant de cobalt fond et fusionne les particules de carbure de tungstène, formant un matériau solide et dense.
- Finition : Après le frittage, les bandes de carbure peuvent subir d'autres traitements, tels que le meulage, le polissage ou le revêtement, afin d'obtenir la finition de surface, les dimensions et les propriétés souhaitées.
Un monde de variété : Types de bandes de carbure
Les bandes de carbure sont disponibles dans une large gamme de nuances, de tailles et de configurations afin de répondre aux divers besoins des différentes industries :
Aperçu des propriétés des bandes de carbure
Propriété | Description | Valeurs typiques |
---|---|---|
Dureté (HRA) | Résistance à l'indentation et à la rayure | 88-95 |
Résistance à la rupture transversale (TRS) | Capacité à résister aux forces de flexion | 1500-3000 N/mm² |
Densité | Masse par unité de volume | 13,5-15,0 g/cm³ |
Taille des grains | Taille des particules de carbure de tungstène | 0,5-10 µm |
Teneur en cobalt | Pourcentage de liant cobalt | 6-12% |
Tableau 1 : Principales propriétés des bandes de carbure
Remarque : Les valeurs des propriétés spécifiques peuvent varier en fonction de la nuance de carbure et du fabricant.
Applications dans toutes les industries : Où les bandes de carbure brillent
La polyvalence des bandes de carbure est évidente dans leur large gamme d'applications :
- Le travail du bois : Pointes de scie, mèches de toupie et outils de coupe pour le traitement des bois durs, du contreplaqué et des matériaux composites.
- Travail des métaux : Outils de coupe, pièces d'usure et matrices pour l'usinage, l'estampage et le formage des métaux.
- Construction : Arêtes de coupe pour les scies à béton, les outils de fraisage des routes et le matériel de forage.
- Fabrication : Composants, guides et outils résistants à l'usure pour divers procédés de fabrication.
- Autres secteurs : Les bandes de carbure trouvent des applications dans des industries allant de l'aérospatiale au secteur médical, où la dureté exceptionnelle, la résistance à l'usure et la précision sont primordiales.
Comparaison des concurrents : Fournisseurs de bandes de carbure
Fournisseur | Localisation | Fourchette de prix (par pièce) | Spécialités |
---|---|---|---|
TRUER | Mondial | $5 – $50 | Sur mesure solutions en carburegrades de haute performance |
Kennametal | ÉTATS-UNIS | $10 – $75 | Large gamme de qualités standard et spécialisées |
Sandvik Coromant | Suède | $15 – $100 | Revêtements et géométries avancés pour les applications exigeantes |
Kyocera | Japon | $8 – $60 | Carbure de haute qualité pour les outils de coupe et les pièces d'usure |
Tableau 2 : Comparaison des fournisseurs de bandes de carbure
Remarque : Les prix sont approximatifs et peuvent varier en fonction de la qualité, de la taille, de la quantité et des conditions du marché.
Peser le pour et le contre : avantages et limites des bandes de carbure
Bandes de carbure : Les bons et les moins bons
Avantages | Limites |
---|---|
Dureté et résistance à l'usure exceptionnelles | Relativement fragile, susceptible de se fracturer sous l'effet d'un impact |
Efficacité et précision de coupe élevées | Peut être coûteux par rapport à d'autres matériaux |
Longue durée de vie de l'outil, réduisant les temps d'arrêt et les coûts | Nécessite un équipement spécialisé pour l'usinage et la transformation |
Polyvalence pour diverses applications et matériaux | Peut ne pas convenir à toutes les applications de coupe ou d'usure |
Tableau 3 : Avantages et limites des bandes de carbure
Au-delà de l'essentiel : Faits intéressants sur les bandes de carbure
- Le rival de Diamond : Le carbure de tungstène est l'un des matériaux les plus durs connus de l'homme, après le diamant.
- Des ampoules aux outils : Le tungstène, principal composant du carbure de tungstène, était initialement utilisé dans les filaments des ampoules à incandescence.
- Matériau Space-Age : En raison de leurs propriétés extrêmes, les matériaux en carbure sont utilisés dans les applications aérospatiales, notamment les tuyères de fusées et les outils de coupe pour l'exploration spatiale.
Pourquoi choisir TRUER pour vos besoins en bandes de carbure ?
Chez TRUER, nous sommes passionnés par la fourniture de solutions en carbure qui permettent à nos clients d'obtenir des résultats exceptionnels. Voici pourquoi TRUER se distingue :
- Une qualité sans compromis : Nous nous procurons des matériaux en carbure de la plus haute qualité et appliquons des mesures rigoureuses de contrôle de la qualité tout au long de notre processus de fabrication.
- Solutions personnalisées : Nous sommes spécialisés dans la fabrication de bandes de carbure sur mesure pour répondre à vos spécifications uniques, qu'il s'agisse de la nuance, de la géométrie, de la taille ou de la finition.
- Expertise technique : Notre équipe d'experts en carbure fournit des conseils et une assistance, vous aidant à sélectionner la solution de carbure optimale pour votre application.
- Une portée mondiale : Grâce à notre présence mondiale, nous assurons une livraison dans les délais et un service clientèle réactif, où que vous soyez dans le monde.
FAQs : Répondre à vos questions sur les bandes de carbure
1. Quelle est la différence entre la qualité du carbure et la taille des grains ?
La qualité du carbure fait référence à la formulation spécifique du carbure de tungstène, du cobalt et d'autres éléments, influençant les propriétés globales. La taille des grains fait référence à la taille des particules de carbure de tungstène dans la matrice de carbure, ce qui affecte la dureté et la résistance à l'usure.
2. Les bandes de carbure peuvent-elles être affûtées ?
Oui, les bandes de carbure peuvent être affûtées à l'aide de meules et d'équipements diamantés spécialisés. Toutefois, il est essentiel de maintenir des angles et des dégagements corrects pour obtenir des performances optimales.
3. Quelles sont les précautions à prendre pour travailler avec des bandes de carbure ?
Les bandes de carbure sont extrêmement dures et peuvent se briser en cas de chute ou de mauvaise manipulation. Portez toujours des lunettes de sécurité, des gants et des vêtements appropriés lorsque vous manipulez des bandes de carbure.
4. Comment choisir la bande de carbure adaptée à mon application ?
Tenez compte du matériau à couper, de la qualité de coupe souhaitée, de la vitesse de coupe, de la vitesse d'avance et de la durée de vie de l'outil. La consultation d'un expert en carbure peut vous aider à faire le meilleur choix.
5. Quelle est la durée de vie d'une bande de carbure ?
La durée de vie dépend de facteurs tels que la qualité du carbure, l'application, les paramètres de coupe et l'entretien. Avec une utilisation et un entretien appropriés, les bandes de carbure peuvent offrir une durée de vie exceptionnelle aux outils, réduisant ainsi de manière significative les temps d'arrêt et les coûts.