Carbure inserts : ces petits outils discrets sont les héros méconnus d'innombrables industries, révolutionnant discrètement la façon dont nous façonnons et formons le monde qui nous entoure. Des courbes élégantes de votre smartphone aux puissants moteurs qui propulsent les avions, les plaquettes en carbure jouent un rôle essentiel dans la fabrication des produits dont nous dépendons quotidiennement.
Cet article de blog se penche sur le monde fascinant des applications des plaquettes en carburequi révèle comment ces petites centrales repoussent les limites de la précision, de l'efficacité et de l'innovation dans un large éventail d'industries.
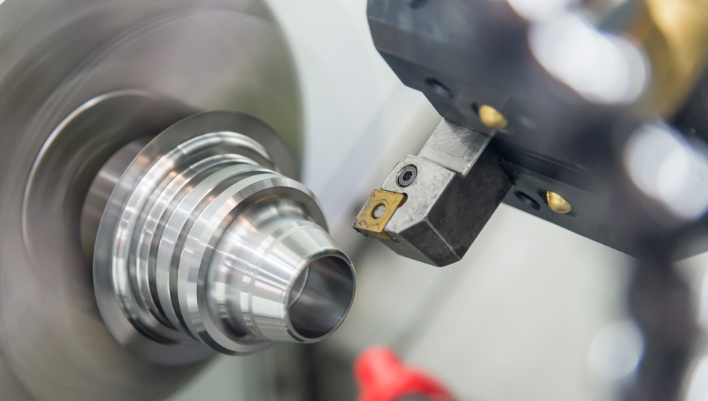
Pourquoi des plaquettes en carbure ? La science au service d'une performance supérieure
Avant de se pencher sur leurs applications, il convient de comprendre ce qui rend les plaquettes en carbure si particulières. Ces outils de coupe sont généralement composés de carbure de tungstène, un matériau remarquablement dur et résistant à l'usure, formé par le frittage de particules de carbure de tungstène avec un métal liant, généralement du cobalt.
Cette composition unique confère aux plaquettes en carbure des propriétés exceptionnelles :
- Dureté extrême : Les plaquettes en carbure peuvent résister à des températures et des pressions extrêmes, ce qui leur permet d'usiner facilement les matériaux les plus durs.
- Résistance exceptionnelle à l'usure : Ils conservent leurs arêtes de coupe aiguisées pendant de longues périodes, ce qui réduit les temps d'arrêt pour les changements d'outils et augmente la productivité globale.
- Usinage à grande vitesse : Les plaquettes en carbure excellent à des vitesses de coupe élevées, ce qui permet de réduire considérablement les temps d'usinage et d'augmenter la production.
Au-delà de l'arête de coupe : exploration de 10 applications remarquables des plaquettes en carbure
Les plaquettes en carbure sont incroyablement polyvalentes et trouvent des applications dans une multitude d'industries. Examinons dix exemples convaincants :
- Industrie automobile : Les plaquettes en carbure sont indispensables à la fabrication de blocs moteurs, de culasses, de composants de transmission et d'innombrables autres pièces automobiles. Leur capacité à maintenir des tolérances serrées et à produire des finitions lisses est cruciale pour garantir des performances optimales du moteur et la longévité du véhicule.
- Fabrication aérospatiale : La construction d'avions nécessite des matériaux légers mais incroyablement résistants, souvent difficiles à usiner. Les plaquettes en carbure, avec leur dureté et leur résistance à l'usure exceptionnelles, excellent dans l'usinage des alliages de qualité aérospatiale, des composites et d'autres matériaux avancés utilisés dans les composants aéronautiques, garantissant ainsi la précision et la fiabilité dans cette industrie exigeante.
- Fabrication de dispositifs médicaux : Lorsque des vies sont en jeu, la précision est primordiale. Les plaquettes en carbure jouent un rôle essentiel dans la production d'implants médicaux, d'instruments chirurgicaux et d'équipements de diagnostic. Leur capacité à créer des géométries complexes avec des tolérances serrées et des finitions de surface exceptionnelles est essentielle pour garantir la sécurité et l'efficacité de ces dispositifs qui sauvent des vies.
- Production d'énergie : Qu'il s'agisse d'énormes pales d'éoliennes exploitant les énergies renouvelables ou de composants complexes dans les centrales nucléaires, les plaquettes en carbure contribuent à façonner un avenir durable. Leur capacité à usiner des matériaux robustes et résistants à la chaleur les rend idéales pour la fabrication de composants utilisés dans la production et la distribution d'énergie.
- Exploration pétrolière et gazière : L'extraction du pétrole et du gaz dans les profondeurs de la terre nécessite des équipements robustes capables de résister à des pressions extrêmes et à des environnements corrosifs. Les plaquettes en carbure sont essentielles pour la fabrication des trépans, des vannes, des tuyaux et d'autres composants critiques utilisés dans l'exploration et la production de pétrole et de gaz.
- Construction et infrastructure : La construction du monde qui nous entoure nécessite des outils capables de réaliser les travaux les plus difficiles. Les plaquettes en carbure se trouvent dans les outils utilisés pour couper, percer et façonner le béton, l'acier et d'autres matériaux de construction, garantissant ainsi la solidité et la durabilité des bâtiments, des ponts et d'autres projets d'infrastructure.
- Travail du bois et fabrication de meubles : Souvent associées au travail des métaux, les plaquettes en carbure ont également révolutionné le travail du bois. Les lames de scie et les fraises au carbure permettent des coupes exceptionnellement lisses dans le bois, le contreplaqué et les matériaux composites, améliorant ainsi la qualité et l'efficacité de la fabrication de meubles et d'autres applications du travail du bois.
- Fabrication de moules et de matrices : La création de moules et de matrices pour la production de pièces en plastique, en métal et en matériaux composites exige la plus grande précision. Les plaquettes en carbure sont largement utilisées dans l'usinage de ces outils complexes, garantissant la précision et la répétabilité des pièces moulées ou coulées sous pression qu'ils produisent.
- Fabrication de produits électroniques : La miniaturisation des appareils électroniques nécessite l'usinage de caractéristiques incroyablement petites et précises. Les plaquettes en carbure sont utilisées dans les applications de micro-usinage, pour créer des circuits complexes, des connecteurs et d'autres composants que l'on trouve dans les smartphones, les ordinateurs et d'autres appareils électroniques.
- Fabrication de bijoux : Des gravures délicates aux sertissages complexes, les outils en carbure, y compris les fraises et les burins, permettent aux bijoutiers d'obtenir des détails et une précision exceptionnels dans leur travail, créant ainsi des pièces de joaillerie époustouflantes.
Propriétés des plaquettes en carbure : Un aperçu de leurs capacités
Propriété | Description |
---|---|
Dureté | Mesurées en dureté Vickers (HV), les plaquettes en carbure vont généralement de 1200 HV à 2400 HV, ce qui leur permet de couper même les matériaux les plus durs. |
Résistance à la rupture transversale (TRS) | Indique la résistance de la plaquette à la rupture sous contrainte de flexion, cruciale pour supporter les forces rencontrées lors de l'usinage. |
Revêtement | Différents revêtements, tels que le nitrure de titane (TiN), le carbonitrure de titane (TiCN) et l'oxyde d'aluminium (Al2O3), améliorent la résistance à l'usure, réduisent le frottement et augmentent la durée de vie de l'outil. |
Géométrie | La géométrie de la plaquette, y compris l'angle de coupe, l'angle de dépouille et la conception du brise-copeaux, influe considérablement sur la formation et l'évacuation des copeaux ainsi que sur l'état de surface. |
L'avenir de l'usinage : Les plaquettes en carbure à l'avant-garde
Les plaquettes en carbure continuent d'évoluer à mesure que la technologie progresse et que les exigences de fabrication deviennent de plus en plus strictes. De nouvelles nuances de carbure, des revêtements innovants et des géométries avancées sont constamment développés pour améliorer les performances de coupe, prolonger la durée de vie des outils et repousser les limites du possible en matière d'usinage.
Qu'il s'agisse de minimiser les déchets, de réduire la consommation d'énergie ou de permettre la création de produits plus légers, plus résistants et plus efficaces, les plaquettes en carbure jouent un rôle essentiel dans la construction d'un avenir plus durable et plus avancé sur le plan technologique.
Vous souhaitez acheter une plaquette en carbure de grande qualité au meilleur prix ? Cliquez ici ici.