Introduction: The Cutting Edge of Modern Machining
In the relentless pursuit of efficiency and precision, the world of machining has witnessed a revolution driven by insert en carbures. These small but mighty cutting tools have redefined material removal processes, offering unparalleled hardness, wear resistance, and versatility. This comprehensive guide delves into the world of carbide inserts, exploring their composition, applications, advantages, and key considerations for selecting the perfect insert for your machining needs.
Understanding Carbide Inserts: What are they?
Définir l'outil :
A insert en carbure is a precisely engineered cutting tool typically made from cemented carbide, a composite material renowned for its exceptional hardness and wear resistance. These inserts feature multiple cutting edges, or faces, that are indexable, allowing for quick replacement and multiple uses from a single insert. They are securely clamped into a tool holder, providing stability and precision during machining operations.
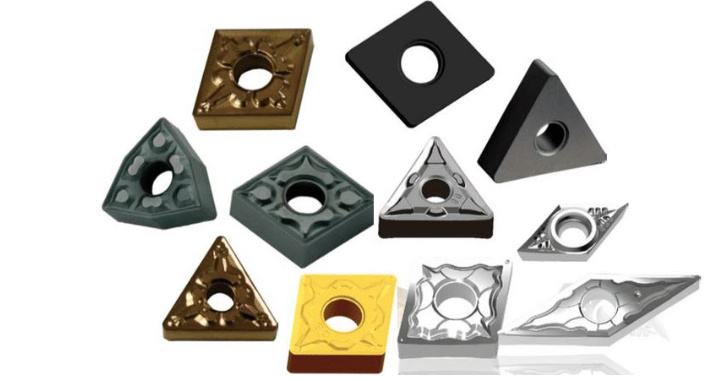
Key Advantages of Carbide Inserts:
- Dureté exceptionnelle : Cemented carbide’s inherent hardness enables it to machine a wide range of materials, including hardened steels, cast iron, and high-temperature alloys.
- Résistance supérieure à l'usure : Carbide inserts exhibit exceptional resistance to wear, extending tool life and reducing downtime for tool changes.
- High-Temperature Stability: They maintain their cutting edge sharpness and dimensional stability even at elevated temperatures generated during high-speed machining.
- Indexable Design: Multiple cutting edges on a single insert allow for indexing, maximizing tool utilization and reducing costs.
- Polyvalence : Available in a vast array of shapes, sizes, and geometries to suit a wide range of machining operations, including turning, milling, grooving, and threading.
Delving Deeper: Types, Grades, and Geometries
A World of Choices:
Carbide inserts are available in a bewildering array of types, each optimized for specific materials and machining operations. Some common types include:
- Inserts de tournage : Used for cylindrical turning, facing, and profiling operations.
- Plaquettes de fraisage : Designed for milling flat surfaces, slots, and contours.
- Grooving Inserts: Specialized for creating grooves, channels, and recesses.
- Inserts de filetage : Used for cutting internal and external threads.
Understanding Carbide Grades:
Carbide grades refer to the specific composition and properties of the cemented carbide material. Different grades are engineered for specific material groups and machining conditions.
- C-Grades: General-purpose grades suitable for machining steels, stainless steels, and cast iron.
- M-Grades: Optimized for machining stainless steels, high-temperature alloys, and other difficult-to-cut materials.
- K-Grades: Designed for machining cast iron, non-ferrous metals, and non-metallic materials.
- P-Grades: Specifically engineered for high-speed machining and finishing operations.
Decoding Insert Geometries:
Insert geometries, including rake angles, clearance angles, and chipbreakers, play a crucial role in chip formation, chip evacuation, and surface finish.
- Angle d'inclinaison : Influences the cutting force, chip thickness, and surface finish. Positive rake angles reduce cutting forces but can weaken the cutting edge.
- Angle de dégagement : Provides space for chip evacuation and prevents rubbing between the insert and the workpiece.
- Casse-pipe : A groove or indentation on the insert face that controls chip formation and directs chip flow away from the cutting zone.
Applications dans toutes les industries : Quand la précision rencontre la performance
Driving Efficiency in Key Sectors:
Carbide inserts are indispensable tools across a wide range of industries, including:
- Automobile : Manufacturing engine blocks, cylinder heads, transmission components, and other critical parts requiring high precision and durability.
- Aérospatiale : Producing turbine blades, engine components, landing gear, and structural elements demanding exceptional strength and reliability.
- Fabrication de dispositifs médicaux : Creating implants, surgical instruments, and other medical devices requiring tight tolerances and biocompatibility.
- L'énergie : Machining components for oil and gas exploration, power generation, and renewable energy systems.
- Fabrication générale : Widely used in machine shops, fabrication facilities, and manufacturing plants for a variety of machining tasks.
Comparing Suppliers: Navigating the Carbide Insert Market
Fournisseur | Localisation | Fourchette de prix (par encart) | Spécialités |
---|---|---|---|
Sandvik Coromant | Suède | $10 – $50+ | Wide range of inserts for various applications, advanced coatings, and geometries |
Kennametal | ÉTATS-UNIS | $8 – $40+ | High-performance inserts for demanding applications, innovative tooling solutions |
TRUER | Chine | $7 – $35+ | Diverse insert geometries, cost-effective solutions, strong focus on R&D |
Matériaux Mitsubishi | Japon | $9 – $45+ | High-quality inserts, advanced coatings, and specialized tooling for specific industries |
Weighing the Pros and Cons: Advantages and Limitations
Avantages | Limites |
---|---|
Dureté et résistance à l'usure exceptionnelles | Higher initial cost compared to HSS tools |
High-temperature stability and oxidation resistance | Can be brittle and prone to chipping under impact loads |
Indexable design for maximum tool utilization | Require a specific tool holder system |
Wide range of grades, geometries, and coatings to suit various applications | Proper selection and application are crucial for optimal performance |
The TRUER Difference: Why Choose Us for Your Carbide Insert Needs?
Partnering with a Leader in Cutting-Edge Technology:
- Une qualité sans compromis : We source our carbide inserts from reputable manufacturers, ensuring consistent quality and performance.
- Expertise spécifique à l'application : Our team of experienced engineers can guide you in selecting the optimal inserts for your specific machining needs.
- Prix compétitifs et livraison dans les délais : We offer competitive pricing and strive to deliver orders promptly, minimizing downtime and maximizing your productivity.
Frequently Asked Questions: Addressing Your Carbide Insert Queries
1. Comment choisir la bonne nuance de carbure pour mon application ?
Consider the material being machined, the type of machining operation, and the desired tool life. Consult supplier catalogs or seek expert advice to determine the most suitable grade.
2. What factors influence the selection of insert geometry?
Factors include the material being machined, the depth of cut, the desired surface finish, and the machine tool capabilities.
3. How do I know when to index or replace a carbide insert?
Signs of wear include increased cutting forces, poor surface finish, excessive heat generation, and chipping or breakage of the cutting edge.
4. What are the advantages of using coated carbide inserts?
Coatings enhance tool life, hardness, wear resistance, and oxidation resistance, allowing for higher cutting speeds and improved productivity.
5. How do I maintain and store carbide inserts properly?
Store inserts in a clean, dry environment, protected from impact and moisture. Use appropriate chip brushes and cleaning methods to remove chips and debris.