Vue d'ensemble
Haute qualité ébauches en carbure de tungstène sont indispensables dans diverses industries en raison de leur dureté exceptionnelle, de leur durabilité et de leur polyvalence. En tant que fournisseur de premier ordre, nous proposons des ébauches en carbure de tungstène de qualité supérieure qui répondent à un large éventail d'applications, des outils de coupe aux pièces résistantes à l'usure. Ce guide complet explore les détails complexes des ébauches en carbure de tungstène, leur production, leur utilisation, les tendances du marché et les raisons pour lesquelles le choix d'un fournisseur fiable comme TRUER est crucial pour la réussite de votre entreprise.
Introduction détaillée
Que sont les ébauches en carbure de tungstène ?
Les ébauches en carbure de tungstène sont des outils préformés, non affûtés, fabriqués en carbure de tungstène, un matériau composite composé d'atomes de tungstène et de carbone. Cette combinaison donne un matériau extrêmement dur et dense, capable de résister à des températures et des pressions élevées. Ces ébauches servent de matière première pour divers outils de coupe, de forage et de résistance à l'usure.
Comment fonctionnent les ébauches en carbure de tungstène ?
Le carbure de tungstène fonctionne grâce à ses propriétés matérielles uniques. Le tungstène apporte une grande dureté et un point de fusion élevé, tandis que les atomes de carbone créent une forte liaison covalente qui améliore la durabilité. Le matériau est soumis à un processus de frittage, au cours duquel le carbure de tungstène en poudre est pressé et chauffé pour former des ébauches solides. Ce processus garantit une densité et une dureté uniformes sur l'ensemble de l'ébauche.
Comment utiliser les ébauches en carbure de tungstène
L'utilisation d'ébauches en carbure de tungstène implique de les usiner ou de les façonner dans la forme d'outil souhaitée. Cela peut inclure le meulage, la coupe et le polissage. En raison de la dureté du matériau, il est souvent nécessaire d'utiliser des équipements spécialisés, tels que des outils revêtus de diamant. Les produits finis sont ensuite utilisés dans diverses applications, telles que la fabrication d'outils de coupe, de pièces de machines industrielles et de composants résistants à l'usure.
Comment traiter les ébauches en carbure de tungstène
Le traitement des ébauches en carbure de tungstène comporte plusieurs étapes :
- Découpage : Utilisation d'outils diamantés ou en carbure pour découper les ébauches à la taille souhaitée.
- Broyage : Meulage de précision pour obtenir la forme et l'état de surface requis.
- Polissage : Lissage de la surface pour améliorer les performances et la longévité.
- Revêtement : Application de revêtements, tels que le nitrure de titane, pour améliorer la résistance à l'usure et réduire la friction.
Tendances du marché
Le marché des ébauches en carbure de tungstène se développe en raison de la demande croissante d'outils durables et fiables dans diverses industries. Les principaux facteurs de cette croissance sont les suivants
- Progrès dans la fabrication : L'amélioration des techniques et des technologies de fabrication permet d'accroître la qualité et les performances des ébauches en carbure de tungstène.
- La demande dans les marchés émergents : L'industrialisation rapide dans des régions telles que l'Asie-Pacifique stimule la demande d'outils et de composants de haute qualité.
- Tendances en matière de durabilité : La recyclabilité du carbure de tungstène en fait une option intéressante pour les industries soucieuses de l'environnement.
Spécifications des produits
Pour vous aider à comprendre les différentes options disponibles, voici un tableau détaillé des spécifications et des caractéristiques de nos ébauches en carbure de tungstène de haute qualité.
Type | Composition | Attributs | Caractéristiques | Spécifications | Gamme de tailles | Grade | Standard |
---|---|---|---|---|---|---|---|
Ébauches standard | WC + Co | Dureté élevée, résistance à l'usure | Densité uniforme | Certifié ISO | 10mm - 100mm | K10, K20, K30 | ISO 9001 |
Ébauches à micro-grains | WC + Co + Additifs | Grain ultra-fin, haute ténacité | Finition de surface améliorée | Personnalisable | 5mm - 50mm | K05, K15 | ASTM B777 |
Pièces d'usure ébauches | WC + Ni | Résistant à la corrosion, durable | Haute résistance aux chocs | Spécifique à l'industrie | 20mm - 200mm | W10, W20 | DIN 9001 |
Ébauches d'outils de coupe | WC + Co + TiC | Rétention supérieure de l'arête de coupe | Usinage de haute précision | OEM disponible | 2mm - 80mm | K40, K50 | ANSI B212 |
Applications
Les ébauches en carbure de tungstène sont indispensables dans de nombreuses industries. Voici quelques-unes des principales applications :
- Travail des métaux : Outils de coupe, forets et fraises.
- Exploitation minière : Pièces résistantes à l'usure pour les équipements de forage et d'excavation.
- Le travail du bois : Mèches de toupie, lames de scie et couteaux à raboter.
- Aérospatiale : Composants de précision soumis à de fortes contraintes et à l'usure.
- Automobile : Pièces de moteur, sièges de soupapes et composants d'injecteurs de carburant.
- Pétrole et gaz : Trépans, joints d'étanchéité résistants à l'usure et composants de contrôle du débit.
- Médical : Instruments chirurgicaux et outils dentaires.
- Construction : Outils de coupe et de forage du béton.
Analyse comparative des fournisseurs
Pour vous aider à prendre une décision, le tableau suivant compare différents fournisseurs d'ébauches en carbure de tungstène sur la base de critères clés.
Fournisseur | Localisation | Fourchette de prix (par pièce) | Spécialités |
---|---|---|---|
Kennametal | ÉTATS-UNIS | $20 – $100 | Dimensions sur mesure, livraison rapide |
Sandvik | Suède | $25 – $120 | Haute précision, certifié ISO |
Outils de coupe ZCC | Chine | $15 – $90 | Faible coût, commandes groupées |
Sumitomo Electric | Japon | $22 – $110 | Revêtements avancés, micro-grains |
Avantages et inconvénients
Voici une comparaison complète des avantages et des inconvénients de l'utilisation d'ébauches en carbure de tungstène.
Avantages | Inconvénients |
---|---|
Dureté exceptionnelle | Coût élevé |
Résistance à l'usure et à la corrosion | Difficile à usiner sans équipement spécialisé |
Tolérance aux températures élevées | Peut être fragile en cas d'impact important |
Longue durée de vie | Nécessite des techniques de fabrication précises |
Matériau recyclable | Peut être plus cher que d'autres matériaux |
Des performances constantes dans les applications exigeantes | Flexibilité limitée dans certaines applications |
Pourquoi choisir TRUER
Choisir TRUER en tant que fournisseur d'ébauches en carbure de tungstène de haute qualité, vous assure de recevoir les meilleurs produits, accompagnés d'un service clientèle exceptionnel. Notre engagement envers l'excellence se reflète dans nos processus rigoureux de contrôle de la qualité, nos prix compétitifs et notre capacité à personnaliser les produits pour répondre à vos besoins spécifiques. Avec TRUER, vous bénéficiez de :
- Matériaux de haute qualité : Nous n'utilisons que les matières premières les plus nobles pour garantir des performances et une durabilité supérieures.
- Fabrication avancée : Nos installations et technologies de pointe garantissent la précision et la cohérence.
- Vaste expérience : Des années d'expertise dans le secteur nous permettent de fournir des informations et des solutions précieuses.
- Soutien à la clientèle : Notre équipe dévouée est toujours disponible pour répondre à toute demande de renseignements ou d'assistance technique.
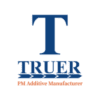
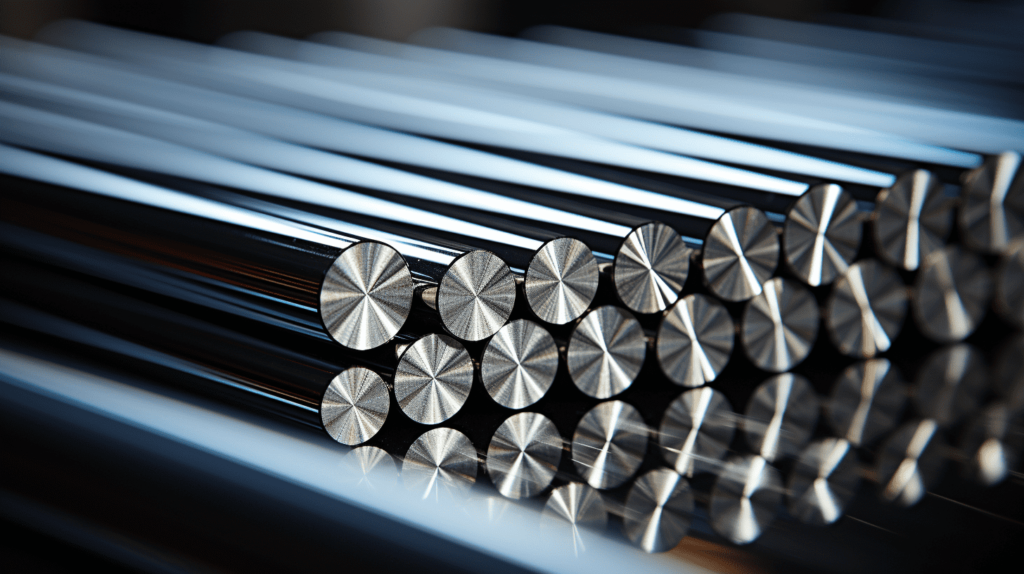
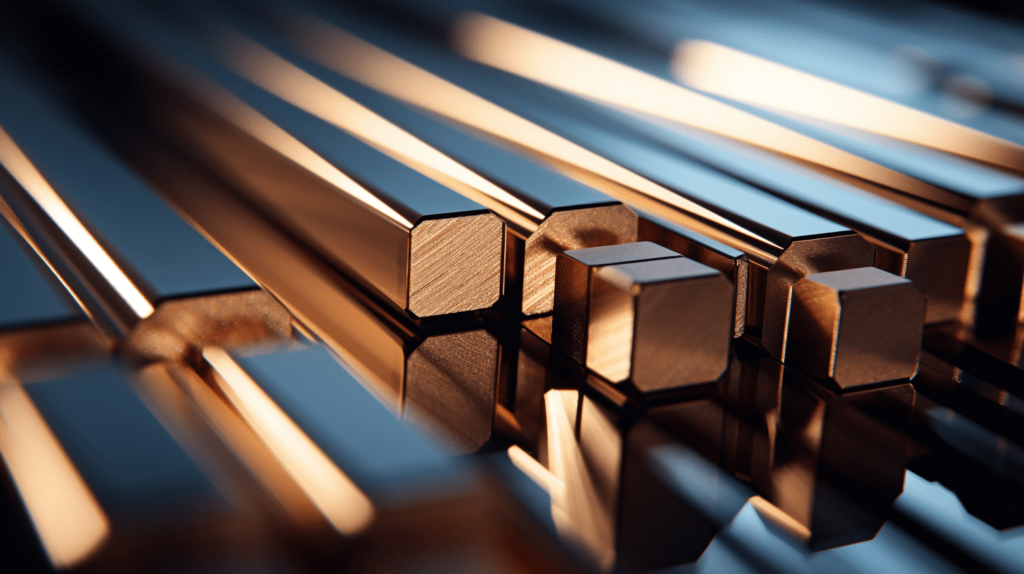
FAQ
Voici quelques questions fréquemment posées pour répondre aux préoccupations courantes et fournir de plus amples informations sur nos ébauches en carbure de tungstène.
Q1 : Quel est le délai de livraison des commandes ?
A1 : Le délai d'exécution varie en fonction de la taille de la commande et des exigences de personnalisation. En règle générale, les commandes standard sont traitées dans un délai de 2 à 4 semaines, tandis que les commandes personnalisées peuvent prendre plus de temps.
Q2 : Puis-je demander des tailles et des formes personnalisées ?
A2 : Oui, nous offrons des services de personnalisation pour répondre à vos besoins spécifiques. Contactez notre équipe de vente pour nous faire part de vos besoins et nous vous proposerons une solution sur mesure.
Q3 : Comment puis-je m'assurer de la qualité des ébauches ?
A3 : Nos ébauches en carbure de tungstène font l'objet de contrôles de qualité rigoureux à chaque étape de la production. Nous fournissons également des certifications de matériaux et des rapports d'essai sur demande.
Q4 : Quels modes de paiement acceptez-vous ?
A4 : Nous acceptons différents modes de paiement, notamment les virements bancaires, les cartes de crédit et PayPal. Veuillez contacter notre service de facturation pour plus de détails.
Q5 : Proposez-vous une assistance technique pour l'usinage d'ébauches en carbure de tungstène ?
A5 : Oui, notre équipe technique est disponible pour fournir des conseils et une assistance pour l'usinage et le traitement de nos ébauches en carbure de tungstène. Nous pouvons vous conseiller sur les outils, les techniques et les meilleures pratiques afin d'obtenir des résultats optimaux.