Plaquettes en carbure peuvent sembler faussement simples, mais sous leur apparence modeste se cache un monde de géométrie et de conception complexes, chaque élément étant méticuleusement conçu pour optimiser les performances de coupe. Comprendre comment ces caractéristiques géométriques influencent les résultats de l'usinage est essentiel pour sélectionner la plaquette en carbure adaptée à la tâche et obtenir des résultats exceptionnels.
Cet article de blog se penche sur la relation fascinante entre géométrie des plaquettes en carbure et la performance de coupe, en explorant 7 éléments clés de la conception et leur impact sur les résultats de l'usinage.
1. Angle de coupe : Influence sur l'écoulement des copeaux et les forces de coupe
L'angle de coupe, mesuré entre la face de coupe de la plaquette en carbure (la surface faisant face au copeau) et une ligne perpendiculaire à la pièce à usiner, joue un rôle crucial dans la formation des copeaux et les forces de coupe.
- Angles d'inclinaison positifs : Facilite l'écoulement des copeaux, réduit les efforts de coupe et nécessite moins de puissance. Idéal pour l'usinage de matériaux plus tendres ou pour obtenir des finitions de surface fines.
- Angles d'inclinaison négatifs : Fournissent une arête de coupe plus solide, mieux adaptée à l'usinage de matériaux durs ou aux coupes interrompues où la résistance aux chocs est cruciale. Cependant, les angles de coupe négatifs génèrent des efforts de coupe plus importants.
2. Angle de dégagement : Prévention des frottements et de l'accumulation de chaleur
L'angle de dépouille, formé entre la face latérale de la plaquette en carbure (la surface faisant face à la surface usinée) et la tangente à la pièce à usiner, assure un jeu adéquat entre l'outil et la pièce à usiner, évitant ainsi les frottements et la production excessive de chaleur.
- Angles de dégagement plus importants : Réduit le frottement et l'accumulation de chaleur, ce qui est particulièrement bénéfique pour l'usinage de matériaux tendres ou ductiles sujets au soudage par copeaux.
- Angles de dégagement plus petits : Ils assurent un meilleur soutien de l'arête de coupe, améliorant ainsi la durée de vie de l'outil lors de l'usinage de matériaux durs ou lors d'opérations de coupe lourdes.
3. Géométrie du brise-copeaux : Contrôle de la formation et de l'évacuation des jetons
Les brise-copeaux, les rainures ou les marches incorporées dans la face de coupe de la plaquette en carbure, sont essentiels pour contrôler la formation de copeaux et diriger le flux de copeaux loin de la zone de coupe.
- Casse-pieds larges et peu profonds : Favorise la formation de copeaux courts et courbés, idéal pour l'usinage de matériaux ductiles à des vitesses de coupe élevées.
- Des brise-glaces étroits et profonds : Génère des copeaux plus épais et plus étroits, adaptés à l'usinage de matériaux plus durs ou aux opérations d'ébauche où le contrôle des copeaux est essentiel.
4. Préparation des arêtes de coupe : Influence de la résistance des arêtes et de l'état de surface
L'arête de coupe d'une plaquette en carbure peut être préparée de différentes manières, chacune affectant la résistance de l'arête, l'état de surface et la durée de vie de l'outil.
- Bord adouci : Il permet d'obtenir un bord poli très tranchant, idéal pour réaliser des finitions de surface fines et des tolérances serrées. Cependant, les arêtes adoucies sont plus délicates et sujettes à l'écaillage.
- Bord chanfreiné : Renforce l'arête de coupe, réduisant le risque d'écaillage, en particulier lors de l'usinage de matériaux abrasifs ou lors de coupes interrompues.
- Bord arrondi : Offre un bon équilibre entre la résistance des arêtes et l'état de surface, convenant à une large gamme d'applications d'usinage.
5. Rayon d'angle : Équilibrer la force et la netteté
Le rayon de l'angle, l'arête arrondie à l'intersection des faces de dépouille et de flanc, influence la résistance de la plaquette, son tranchant et sa capacité à faire face à différentes conditions de coupe.
- Coins aigus (petit rayon) : Ils offrent le bord de coupe le plus tranchant, idéal pour obtenir des tolérances serrées et des géométries complexes. Cependant, les angles vifs sont plus susceptibles de s'écailler.
- Coins arrondis (grand rayon) : Ils offrent une solidité et une résistance à l'écaillage accrues, ce qui est particulièrement utile pour les opérations de coupe lourdes ou pour l'usinage de matériaux durs.
6. Épaisseur de la plaquette : Détermination de la rigidité et de la stabilité de l'outil
L'épaisseur d'une plaquette en carbure influe sur sa rigidité et sa résistance à la déformation sous l'effet des forces de coupe.
- Inserts plus épais : Ils offrent une rigidité et une stabilité accrues, essentielles pour les opérations de coupe lourdes ou lors de l'usinage de pièces de grande taille où la déviation peut avoir un impact sur la précision.
- Inserts plus minces : Ils offrent une moindre résistance à la coupe, ce qui réduit la consommation d'énergie et les rend adaptés à l'usinage de pièces délicates ou à l'utilisation de machines plus petites et moins puissantes.
7. Technologie des revêtements : Amélioration de la résistance à l'usure et des performances
Les plaquettes en carbure sont souvent revêtues de matériaux fins et durs afin d'améliorer la résistance à l'usure, de réduire le frottement et d'améliorer les performances globales de coupe.
- Nitrure de titane (TiN) : Revêtement polyvalent qui augmente la dureté, réduit le frottement et améliore la résistance à l'oxydation, convenant à une large gamme d'applications d'usinage.
- Carbonitrure de titane (TiCN) : Offre une dureté et une résistance à l'usure encore plus grandes que le TiN, particulièrement efficace pour l'usinage de matériaux abrasifs ou lors d'opérations à grande vitesse.
- Oxyde d'aluminium (Al2O3) : Offre une excellente résistance à la chaleur et à l'usure, idéale pour l'usinage d'alliages à haute température ou lors d'opérations d'usinage à sec.
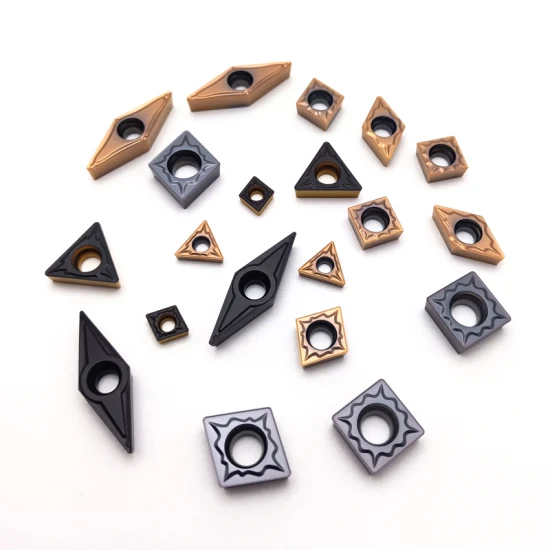
Géométrie des plaquettes en carbure : Guide de référence rapide
Fonctionnalité | Description | Influence sur les performances de coupe |
---|---|---|
Angle d'inclinaison | Angle entre la face du râteau et la ligne perpendiculaire | Affecte l'écoulement des copeaux, les forces de coupe et l'état de surface. |
Angle de dégagement | Angle entre la face du flanc et la tangente de la pièce | Empêche les frottements et contrôle l'accumulation de chaleur |
Brise-copeaux | Rainures ou marches sur la face du râteau | Contrôle la formation et l'évacuation des copeaux |
Préparation à la pointe de la technologie | Adouci, chanfreiné ou arrondi | Affecte la résistance des arêtes, l'état de surface et la durée de vie de l'outil. |
Rayon de l'angle | Bord arrondi à l'intersection du râteau et du flanc | Équilibre entre la force et le tranchant |
Épaisseur de l'insert | Epaisseur totale de l'insert | Détermine la rigidité et la stabilité de l'outil |
Revêtement | Matériau fin et dur appliqué à la surface | Améliore la résistance à l'usure, réduit le frottement, améliore les performances |
FAQs : Répondre à vos questions sur la géométrie des plaquettes en carbure
1. Comment choisir le bon angle d'inclinaison pour mon application ?
Le choix de l'angle de coupe approprié dépend du matériau usiné et des conditions de coupe souhaitées. Les matériaux plus tendres et les opérations de finition bénéficient généralement d'angles de coupe positifs, tandis que les matériaux plus durs et les opérations d'ébauche nécessitent souvent des angles de coupe négatifs.
2. Quelle est l'importance du contrôle des copeaux dans l'usinage ?
Un contrôle efficace des copeaux est essentiel pour maintenir des performances de coupe constantes, éviter l'accumulation de copeaux susceptibles d'endommager la pièce ou l'outil, et garantir la sécurité de l'opérateur. Des brise-copeaux bien conçus jouent un rôle essentiel en éloignant le flux de copeaux de la zone de coupe.
3. Quand dois-je utiliser un insert à angle vif plutôt qu'un insert à angle arrondi ?
Les plaquettes à angles vifs sont idéales pour obtenir des tolérances serrées et des géométries complexes, mais elles sont plus susceptibles de s'écailler. Les plaquettes à angle arrondi offrent une plus grande résistance et conviennent mieux aux opérations de coupe lourdes ou à l'usinage de matériaux durs.
4. Quels sont les avantages de l'utilisation de plaquettes en carbure revêtues ?
Enduit plaquettes en carbure offrent de nombreux avantages, notamment une résistance accrue à l'usure, une réduction du frottement, une meilleure résistance à la chaleur et de meilleures performances de coupe. Différents revêtements sont adaptés à des applications d'usinage et à des matériaux spécifiques.
5. Comment l'épaisseur de la plaquette affecte-t-elle la rigidité de l'outil ?
Les plaquettes plus épaisses offrent une plus grande rigidité et une meilleure résistance à la déformation sous l'effet des forces de coupe, tandis que les plaquettes plus fines offrent moins de résistance à la coupe. Le choix de l'épaisseur appropriée de la plaquette dépend de l'opération d'usinage, de la taille de la pièce et des capacités de la machine.