Introduction : Réplication de précision, une coupe à la fois
Imaginez un monde où il serait possible de reproduire facilement et sans faille les détails les plus complexes et les contours les plus délicats. C'est le domaine du fraisage par copiage, un processus d'usinage qui repose sur la précision et l'exactitude de l'usinage par copiage. Type E carbure pointes brasées pour créer des copies exactes de patrons ou de modèles.
Cet article se penche sur le monde des pointes brasées en carbure de type E, en explorant leurs attributs uniques, leurs avantages et les raisons pour lesquelles elles sont les championnes incontestées du fraisage par copiage et d'autres opérations d'usinage similaires de haute fidélité.
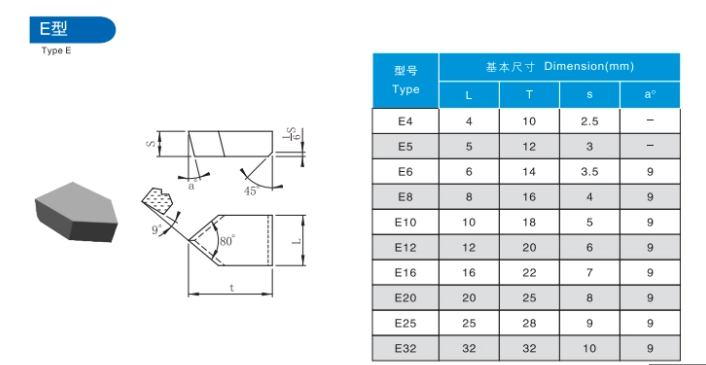
L'art du copiage : Quand la précision rencontre la réplication
Des chefs-d'œuvre en miroir grâce aux prouesses de l'usinage
Le fraisage par copiage, également appelé fraisage par duplication ou profilage, est un procédé d'usinage utilisé pour créer.. :
- Copies exactes : Produire des pièces qui correspondent précisément à la forme et aux dimensions d'un patron ou d'un modèle.
- Contours complexes : Usinage de courbes, de profils et de formes tridimensionnelles complexes qu'il serait difficile, voire impossible, de réaliser avec les méthodes d'usinage conventionnelles.
Ce processus repose sur :
- Modèles principaux ou modèles : Servant de gabarit pour la forme souhaitée, souvent créé en bois, en plastique ou en métal.
- Mécanismes de traçage : Suivre avec précision les contours du modèle principal et transmettre ce mouvement à l'outil de coupe.
- Outils de coupe de haute précision : Les pointes brasées en carbure de type E, avec leur capacité à produire des finitions de surface fines et à maintenir des tolérances serrées, sont essentielles pour obtenir une réplication précise.
Pointes brasées en carbure de type E : Les maîtres du mimétisme
Conçu pour la précision et la fidélité des surfaces
Les pointes brasées en carbure de type E sont spécialement conçues pour le fraisage par copiage et les opérations d'usinage de haute précision similaires, et se distinguent par leurs caractéristiques :
- Bords tranchants : Souvent dotées d'une combinaison d'angles de coupe positifs et négatifs, les pointes de type E privilégient les arêtes de coupe tranchantes afin de minimiser les forces de coupe et d'obtenir des coupes douces et précises qui reproduisent fidèlement les contours du modèle.
- Petits rayons de nez : Le faible rayon de courbure des pointes de type E permet :
- Reproduction des détails : Usinage précis des caractéristiques complexes et des rayons serrés présents dans le modèle principal.
- Festonnage réduit au minimum : Réduire les festons ou les crêtes visibles qui peuvent apparaître sur les surfaces profilées, en particulier lors de l'utilisation d'outils de plus grand diamètre.
- Grades de carbure à grain fin : Les pointes de type E utilisent généralement des nuances de carbure à grain fin présentant une dureté et une résistance à l'usure élevées. Ces nuances :
- Maintenir des bords de coupe aiguisés : Essentiel pour obtenir une précision et un état de surface constants tout au long du processus de fraisage par copiage.
- Minimiser l'usure des arêtes de coupe : Réduire la nécessité de changements fréquents d'outils et assurer une reproduction fidèle des détails du modèle principal.
5 raisons pour lesquelles les pointes brasées en carbure de type E règnent en maître dans le domaine du fraisage par copiage
1. Exactitude et précision inégalées : Les arêtes de coupe tranchantes et les petits rayons du nez des pointes de type E permettent de reproduire fidèlement les détails les plus fins et les tolérances les plus étroites présents dans le maître-modèle.
2. Finition de surface supérieure : Les nuances de carbure à grain fin et la géométrie de coupe tranchante minimisent les forces de coupe et les vibrations, ce qui permet d'obtenir des surfaces exceptionnellement lisses qui ne nécessitent souvent que peu ou pas d'opérations de finition ultérieures.
3. Polyvalence des contours : Les pointes de type E excellent dans l'usinage de courbes, de profils et de formes tridimensionnelles complexes, ce qui les rend idéales pour une large gamme d'applications de fraisage par copiage.
4. Durée de vie prolongée de l'outil : Bien qu'elles ne soient pas soumises aux mêmes efforts de coupe que les pointes d'ébauche, les pointes de type E bénéficient toujours de nuances de carbure résistantes à l'usure, ce qui prolonge la durée de vie de l'outil, en particulier dans les opérations de fraisage par copiage où les paramètres de coupe sont généralement modérés.
5. Le rapport coût-efficacité : La combinaison d'une grande précision, d'une finition de surface supérieure et d'une durée de vie prolongée de l'outil offerte par les pointes de type E contribue à une réduction globale des coûts en réduisant les taux de rebut, en minimisant les opérations de finition et en prolongeant la durée de vie de l'outil.
Applications des pointes brasées en carbure de type E
Au-delà du fraisage par copiage : Quand la réplication de précision est primordiale
Bien que largement reconnues pour leur domination dans le fraisage par copiage, les pointes brasées en carbure de type E excellent également dans d'autres opérations d'usinage exigeant une précision et une finition de surface exceptionnelles :
- Gravure : Création de lettres, de logos et de motifs décoratifs précis sur divers matériaux.
- Fabrication de matrices et de moules : Usinage de cavités et de détails complexes dans les matrices et les moules utilisés pour produire des pièces en plastique, des composants en caoutchouc ou des pièces métalliques moulées.
- Fabrication aérospatiale : Production de composants complexes avec des tolérances serrées et des surfaces lisses, essentielles pour les performances aérodynamiques et l'intégrité structurelle.
- Fabrication de dispositifs médicaux : Création de caractéristiques complexes et de finitions lisses sur les implants médicaux, les instruments chirurgicaux et d'autres dispositifs médicaux de précision.
Choisir la bonne pointe brasée en carbure de type E : Facteurs à prendre en compte
Sélection de l'outillage pour une réplication de précision
Le choix de la pointe brasée en carbure de type E optimale implique la prise en compte de plusieurs facteurs :
- Maîtriser la complexité des motifs : La complexité des détails du maître-modèle et la présence de rayons serrés influencent le choix de la géométrie de la pointe et du rayon du nez.
- Matériau de la pièce : La dureté, l'abrasivité et les propriétés thermiques du matériau guident le choix de la nuance de carbure et du revêtement.
- Exigences en matière de finition de surface : L'état de surface souhaité, souvent spécifié en termes de Ra (rugosité moyenne) ou de Rz (rugosité moyenne de la crête à la vallée), est un facteur primordial dans le choix de la pointe.
- Exigences de tolérance : Les tolérances dimensionnelles requises influencent le choix de la géométrie de la pointe et la préparation de l'arête de coupe.
- Capacité des machines-outils : La rigidité et la précision de la machine-outil peuvent avoir un impact sur la finition de surface et les tolérances réalisables.
Sélection des pointes brasées en carbure de type E : Un guide simplifié
Pour faciliter le processus de sélection, voici un tableau résumant les applications typiques et les considérations relatives aux différentes géométries de pointes de type E :
Type E Géométrie de l'embout | Applications typiques | Principales considérations |
---|---|---|
Plaquette ronde à petit rayon de courbure | Fraisage, contournage et gravure de copies à usage général | Offre un bon équilibre entre le tranchant et la résistance pour une large gamme d'applications |
Insert diamanté à pointe acérée | Gravure, usinage de précision, travaux de moulage complexes | Offre une netteté exceptionnelle pour les détails les plus fins et les rayons les plus étroits |
Insert à nez sphérique de petit diamètre | Contournement 3D, usinage de courbes et de mélanges complexes | Idéal pour créer des contours lisses et fluides sur des surfaces tridimensionnelles |
Questions fréquemment posées sur les pointes brasées en carbure de type E
Q1 : Peut-on Pointes brasées en carbure de type E pour les opérations d'ébauche ?
A1 : Les pointes de type E ne sont pas conçues pour l'ébauche et leur utilisation dans de telles applications n'est pas recommandée. Leurs arêtes de coupe tranchantes et leurs nuances de carbure à grain fin sont optimisées pour la finition et l'usinage de précision, et non pour l'enlèvement de matière important.
Q2 : Quels sont les signes d'usure d'une pointe brasée en carbure de type E ?
A2 : Les signes d'usure les plus courants sont l'arrondi de l'arête de coupe, l'usure de la face de dépouille ou du flanc et la formation d'une arête rapportée (BUE) sur l'arête de coupe. Dans le cas du fraisage de copies, l'usure peut se manifester par une perte de précision dans la reproduction des détails du modèle.
Q3 : Comment puis-je obtenir la meilleure finition de surface possible avec une pointe brasée en carbure de type E ?
A3 : Les facteurs clés comprennent la sélection de la géométrie et de la qualité de pointe appropriées à l'application, l'optimisation des paramètres de coupe (en utilisant des avances et des profondeurs de coupe plus faibles), l'application correcte du liquide de coupe et le maintien d'un réglage rigide de la machine.
Q4 : Quelle est la différence entre une pointe de type E à insert rond et une pointe de type E à insert diamant ?
A4 : Les plaquettes rondes avec de petits rayons de nez offrent un bon équilibre entre la netteté et la résistance pour le fraisage et le contournage de copies à usage général, tandis que les plaquettes diamantées avec des pointes acérées offrent une netteté exceptionnelle pour la gravure, l'usinage de détails fins et le travail complexe sur les moules.
Q5 : Quand devrais-je choisir un embout à nez sphérique de type E ?
A5 : Les plaquettes à nez sphérique de petit diamètre sont idéales pour le contournage 3D et l'usinage de courbes et de mélanges complexes, ce qui les rend bien adaptées à la création de contours lisses et fluides sur des surfaces tridimensionnelles.