Dans le monde de l'usinage de haute précision, où les tolérances se mesurent en microns et où les performances sont primordiales, solide carbure cannes règnent en maîtres. Ces merveilles d'ingénierie, fabriquées à partir de carbure de tungstène incroyablement dur et résistant à l'usure, forment l'épine dorsale d'innombrables outils de coupe et pièces d'usure qui font fonctionner des industries allant de l'aérospatiale au secteur médical.
Mais toutes les tiges de carbure ne se valent pas. Ce guide complet examine les subtilités de quatre types de tiges en carbure essentiels. tige de carbure solide Chacun d'entre eux présente des caractéristiques et des avantages uniques adaptés à des défis d'usinage spécifiques :
- Tige droite en carbure à trou de refroidissement
- 2 trous de refroidissement droits Tige en carbure
- 2 trous de refroidissement hélicoïdaux Tige en carbure
- Tige en carbure rectifiée chanfreinée à l'extrémité
De la compréhension de leurs caractéristiques distinctes à l'exploration de leurs diverses applications, ce guide vous apporte les connaissances nécessaires pour naviguer dans le monde des barres en carbure monobloc et sélectionner le type idéal pour vos besoins d'usinage de précision.
Vue d'ensemble : La puissance de la précision entre vos mains
Contrairement à leurs homologues en acier, les tiges en carbure monobloc conservent leur dureté et leur résistance même à des températures extrêmes, ce qui les rend idéales pour les opérations d'usinage à grande vitesse où la production de chaleur est un problème. Leur résistance exceptionnelle à l'usure se traduit par une durée de vie plus longue de l'outil, une réduction des temps d'arrêt et, en fin de compte, une diminution des coûts de fabrication.
L'ajout de trous de refroidissement et d'autres caractéristiques améliore encore leurs performances, permettant une évacuation efficace des copeaux, une meilleure dissipation de la chaleur et des vitesses de coupe accrues, repoussant ainsi les limites de ce qui est possible en matière d'usinage de précision.
Introduction détaillée : Explorer le monde des barres en carbure monobloc
Qu'est-ce qu'une tige en carbure monobloc ?
Une barre en carbure monobloc, comme son nom l'indique, est une barre cylindrique entièrement constituée de carbure de tungstène, un matériau en carbure cémenté connu pour sa dureté et sa résistance à l'usure exceptionnelles. Ces barres servent de matériau de base pour la fabrication d'une large gamme d'outils de coupe et de pièces d'usure utilisés dans diverses industries.
Principe de fonctionnement des barres en carbure dans l'usinage
Les barres de carbure, lorsqu'elles sont transformées en outils de coupe, fonctionnent selon le principe suivant déformation par cisaillement. Les arêtes de coupe incroyablement dures des outils en carbure, formés à partir du matériau de la tige, sont capables de couper les pièces en dépassant la résistance au cisaillement du matériau. La géométrie de l'outil de coupe, ainsi que ses paramètres de coupe, déterminent l'efficacité et la qualité de la coupe.
Comment les barres en carbure monobloc sont-elles utilisées ?
Les tiges en carbure solide sont généralement usinées dans divers outils de coupe, notamment :
- Fraises en bout : Pour les opérations de façonnage et de profilage.
- Exercices : Pour créer des trous dans divers matériaux.
- Alésoirs : Pour l'agrandissement et la finition des trous existants.
- Outils personnalisés : Adapté aux exigences spécifiques de l'usinage.
Comment les tiges en carbure monobloc sont-elles usinées ?
L'usinage des tiges de carbure nécessite un équipement et des techniques spécialisés en raison de leur extrême dureté. Les meules diamantées sont couramment utilisées pour la mise en forme et la finition des tiges de carbure. Les rectifieuses de précision, souvent à commande numérique, sont utilisées pour obtenir les tolérances serrées et les géométries complexes requises pour les outils de coupe à haute performance.
Classifications et types de barres en carbure monobloc
Les tiges en carbure monobloc sont classées en fonction de divers facteurs, notamment
- Qualité du carbure : Détermine la dureté, la ténacité et la résistance à l'usure de la tige.
- Diamètre et longueur : Disponible dans une large gamme de tailles standard et personnalisées.
- Configuration du trou de refroidissement : Trous de refroidissement droits, hélicoïdaux ou non.
- Finition de la surface : Rectifiés, polis ou revêtus.
Tendances du marché des barres en carbure monobloc
La demande mondiale de tiges en carbure monobloc est en hausse, en raison de l'adoption croissante de technologies de fabrication avancées, en particulier dans des secteurs tels que l'aérospatiale, l'automobile et la médecine. Le marché se caractérise par une concurrence intense, les fabricants innovant constamment pour développer de nouvelles qualités de carbure et de nouveaux outils offrant de meilleures performances et un meilleur rapport coût-efficacité.
Dévoiler les 4 types essentiels de barres en carbure monobloc : Analyse comparative
Fonctionnalité | Tige en carbure massif | 1 Trou de refroidissement droit | 2 trous droits pour le liquide de refroidissement | 2 trous de refroidissement hélicoïdaux | 1 Extrémité chanfreinée Masse |
---|---|---|---|---|---|
Image | |||||
Description | Une tige cylindrique solide en carbure de tungstène. | Une tige de carbure solide avec un seul trou de refroidissement droit en son centre. | Une tige en carbure solide avec deux trous de refroidissement parallèles et droits. | Une tige en carbure massif avec deux trous de refroidissement hélicoïdaux pour une meilleure évacuation des copeaux. | Une tige en carbure massif dont l'une des extrémités est chanfreinée et rectifiée avec précision pour un réglage précis de la longueur de l'outil. |
Débit du liquide de refroidissement | Aucun | Liquide de refroidissement de l'outil | Liquide de refroidissement de l'outil | Liquide de refroidissement de l'outil | Aucun |
Évacuation des puces | Limitée | Améliorée | Amélioration supplémentaire | Supérieure | Limitée |
Applications | Usinage général, pièces d'usure | Perçage, alésage, fraisage | Perçage de trous profonds, usinage en grande série | Usinage haute performance, matériaux difficiles à usiner | Ébauches de mèches d'outils, fabrication d'outils sur mesure |
Avantages | Rentable et polyvalent | Meilleur enlèvement des copeaux, meilleur refroidissement | Flux équilibré du liquide de refroidissement, rigidité accrue | Élimination optimale des copeaux, vitesses de coupe plus élevées | Longueur d'outil précise, temps de réglage réduit |
Limites | L'évacuation des puces peut s'avérer difficile | Un seul trou de refroidissement peut limiter le débit du liquide de refroidissement | Les trous hélicoïdaux peuvent affaiblir la structure de la tige | Plus coûteux que les trous de refroidissement simples | Ne convient pas pour les applications de refroidissement à travers l'outil |
Tableau 1 : Analyse comparative des 4 principaux types de barres en carbure monobloc
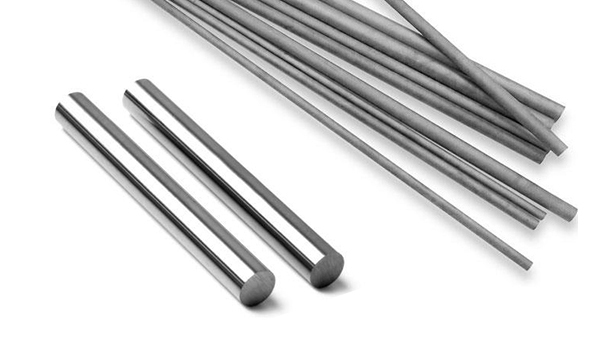
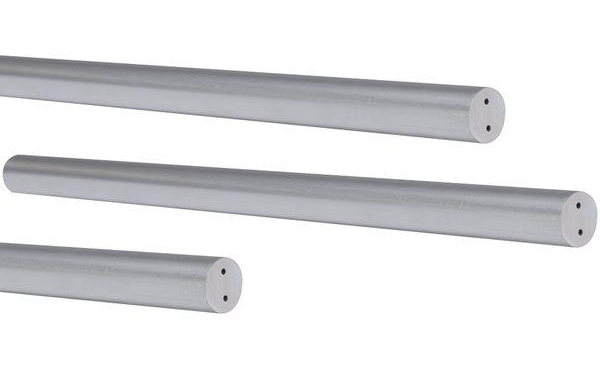
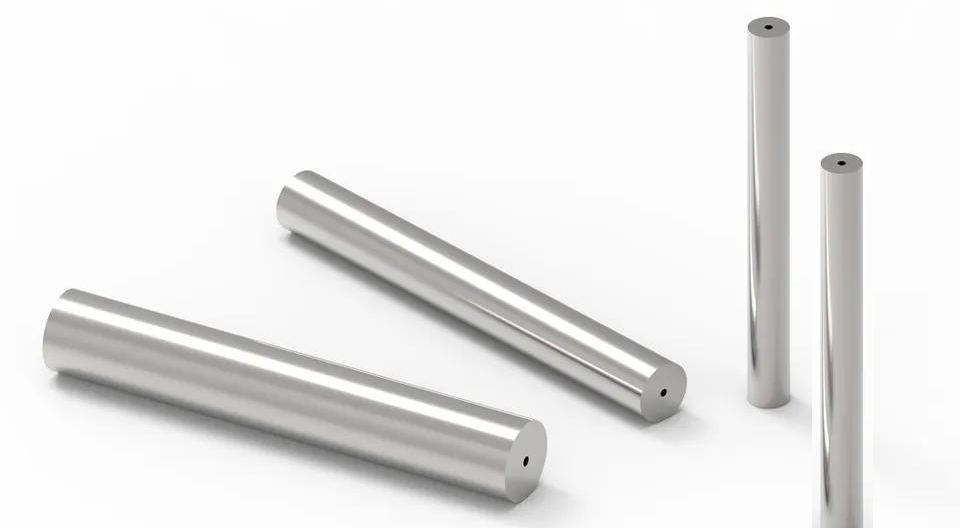
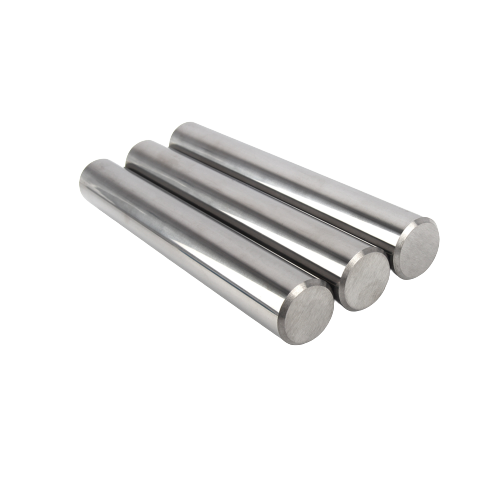
Applications : Là où la précision règne en maître
La polyvalence des tiges en carbure monobloc se reflète dans leurs diverses applications dans de nombreuses industries :
- Aérospatiale : Fabrication de composants de moteurs, d'aubes de turbines et de pièces structurelles.
- Automobile : Production de composants de moteurs, d'engrenages de transmission et de roulements.
- Médical : Création d'instruments chirurgicaux, d'implants et d'outils dentaires.
- Fabrication de moules : Fabrication de moules pour le moulage par injection de plastique, le moulage sous pression et d'autres procédés.
- L'énergie : Forage et usinage de composants pour l'exploration pétrolière et gazière et la production d'électricité.
- Électronique : Micro-usinage de composants électroniques et de cartes de circuits imprimés.
Avantages et limites : Peser le pour et le contre
Fonctionnalité | Avantages | Limites |
---|---|---|
Dureté et résistance à l'usure | Dureté et résistance à l'usure exceptionnelles, permettant d'allonger la durée de vie de l'outil et d'améliorer les performances de coupe. | Ils peuvent être fragiles et susceptibles de s'écailler en cas d'impact ou de vibrations importantes. |
Stabilité à haute température | Conserve sa dureté et sa résistance à des températures élevées, ce qui permet des opérations d'usinage à grande vitesse. | L'usinage du carbure nécessite un équipement et une expertise spécialisés en raison de son extrême dureté. |
Résistance à la corrosion | Très résistant à la corrosion et aux attaques chimiques, il convient à une utilisation dans des environnements difficiles. | Ils peuvent être plus chers que d'autres matériaux d'outils, tels que l'acier rapide. |
Tableau 2 : Avantages et limites des barres en carbure monobloc
Informations connexes : Élargir l'horizon du carbure
- L'importance de la sélection des nuances de carbure : Le choix de la bonne nuance de carbure est crucial pour optimiser les performances et la longévité de l'outil. Les facteurs à prendre en compte sont le matériau usiné, la vitesse de coupe, la vitesse d'avance et l'état de surface requis.
- Le rôle des revêtements dans la performance des outils en carbure : Les revêtements, tels que le TiN, le TiAlN et le carbone de type diamant (DLC), peuvent encore améliorer la résistance à l'usure, la lubrification et la résistance à l'oxydation des outils en carbure.
- Progrès dans la fabrication de barres de carbure : Les innovations dans le domaine de la métallurgie des poudres et des procédés de frittage permettent de développer de nouvelles qualités de carbure aux propriétés améliorées, telles que des structures de grains plus fines et une plus grande ténacité.
FAQs : Répondre à vos questions sur les baguettes en carbure
1. Quelle est la principale différence entre les tiges en carbure monobloc et les plaquettes en carbure ?
Les barres en carbure monobloc sont utilisées pour fabriquer des outils de coupe complets, tandis que les plaquettes en carbure sont des arêtes de coupe indexables fixées sur des porte-outils. Les outils en carbure monobloc offrent une plus grande rigidité et sont généralement utilisés pour des applications de haute précision, tandis que les plaquettes en carbure offrent polyvalence et rentabilité.
2. Comment choisir la bonne configuration de trou de refroidissement pour mon application ?
Le choix de la configuration du trou d'arrosage dépend de l'opération d'usinage, du matériau coupé et de l'évacuation des copeaux souhaitée. Les trous d'arrosage droits conviennent à l'usinage général, tandis que les trous hélicoïdaux excellent dans les applications à haute performance où l'évacuation des copeaux est essentielle.
3. Puis-je réaffûter les outils en carbure monobloc ?
Oui, les outils en carbure monobloc peuvent être réaffûtés plusieurs fois, ce qui prolonge leur durée de vie et réduit les coûts d'outillage. Toutefois, il est essentiel d'utiliser du matériel et des techniques d'affûtage spécialisés pour éviter d'endommager le carbure.
4. Quelles sont les précautions à prendre pour manipuler les barres et les outils en carbure monobloc ?
Le carbure est extrêmement dur et peut se briser en cas d'impact. Portez toujours des lunettes de sécurité, des gants et des vêtements appropriés lorsque vous manipulez du carbure. Soyez prudent lors de l'usinage du carbure, car les copeaux peuvent être extrêmement tranchants et chauds.
5. Où puis-je me procurer des barres de carbure solide de haute qualité ?
Les fabricants et fournisseurs réputés de tiges de carbure peuvent fournir des produits de haute qualité répondant à vos exigences spécifiques. Lors de la sélection d'un fournisseur, tenez compte de facteurs tels que l'expérience, les certifications de qualité et l'assistance à la clientèle.
Vous souhaitez acheter des tiges de carbure de tungstène à des prix avantageux ? ici.