Dans le monde de l'usinage de précision, où les microns comptent et où l'efficacité règne en maître, les enjeux sont considérables, 1 trou droit pour le liquide de refroidissement carbure cannes ont changé la donne. Ces merveilles d'ingénierie, dotées d'un trou de refroidissement percé avec précision en leur centre, délivrent un flux ciblé de liquide de refroidissement directement dans la zone de coupe, ouvrant la voie à une nouvelle ère d'opérations d'usinage plus froides, plus rapides et plus efficaces.
Ce guide complet se penche sur les complexités des tiges en carbure à trou de refroidissement 1 droit, en explorant leur conception, leurs avantages, leurs applications et les facteurs qui en font des outils indispensables dans le paysage manufacturier exigeant d'aujourd'hui.
Qu'est-ce qu'une tige en carbure à 1 trou de refroidissement droit ?
Les tiges de carbure à 1 trou d'arrosage droit sont des tiges de carbure spécialisées, conçues avec un seul trou d'arrosage percé avec précision et traversant axialement leur centre. Cette conception innovante permet d'acheminer le liquide de refroidissement à haute pression directement à l'interface de coupe, ce qui offre de nombreux avantages par rapport aux méthodes traditionnelles d'arrosage par inondation.
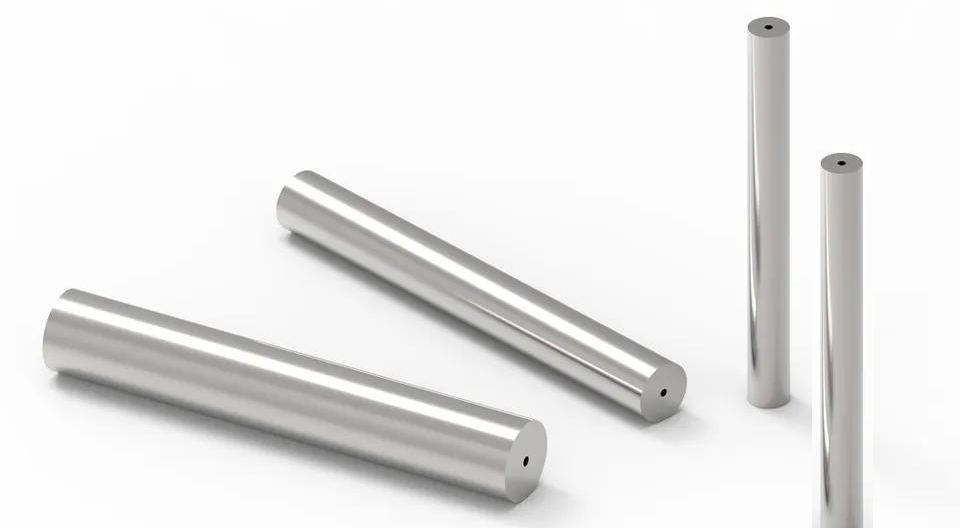
La science derrière le cool : comment ça marche
La magie des tiges en carbure à trou d'arrosage droit réside dans leur capacité à relever les défis de la génération de chaleur et de l'évacuation des copeaux pendant l'usinage :
- Distribution ciblée de liquide de refroidissement : Le trou d'arrosage interne dirige un flux concentré de liquide de refroidissement précisément là où il est le plus nécessaire, c'est-à-dire dans la zone de coupe. Cette approche ciblée maximise l'efficacité du refroidissement tout en minimisant la consommation de liquide de refroidissement par rapport aux méthodes d'arrosage par inondation.
- Évacuation améliorée des puces : Le jet de liquide de refroidissement à haute pression qui traverse la tige évacue efficacement les copeaux de la zone de coupe, évitant ainsi la recoupe des copeaux, améliorant l'état de surface et prolongeant la durée de vie de l'outil.
- Zone affectée par la chaleur réduite : En maintenant la zone de coupe plus froide, ces barres minimisent la zone affectée par la chaleur dans la pièce à usiner, réduisant ainsi le risque de déformation, de gauchissement et de changements métallurgiques.
Considérations relatives à la fabrication et aux matériaux
La production de tiges en carbure à trou de refroidissement droit nécessite des techniques de fabrication spécialisées et des qualités de carbure de haute qualité :
- Sélection des matériaux : Les tiges sont généralement fabriquées à partir de carbures à grains fins présentant une ténacité et une résistance à l'usure élevées, tels que les carbures K10 et K20, ou de carbures à micro-grains spécialisés pour les applications exigeantes.
- Perçage de précision : Le trou de refroidissement est percé à l'aide d'équipements spécialisés, tels que l'usinage par décharge électrique (EDM) ou le perçage au laser, afin d'obtenir le diamètre, la rectitude et l'état de surface requis.
- Contrôle de la qualité : Des mesures rigoureuses de contrôle de la qualité sont appliquées tout au long du processus de fabrication afin de garantir l'intégrité du trou de refroidissement, la précision des dimensions et la qualité globale de la tige.
Catégorisation des tiges en carbure pour trous de refroidissement
Bien que les tiges en carbure à trou d'arrosage droit soient largement utilisées, il existe des variantes pour répondre à des besoins d'usinage spécifiques :
- Nombre de trous pour le liquide de refroidissement : Des tiges avec 2, 3 ou même plus de trous de refroidissement sont disponibles, offrant différents modèles de flux de liquide de refroidissement et de caractéristiques d'évacuation des copeaux.
- Géométrie du trou de refroidissement : La forme et la taille du trou de refroidissement peuvent être adaptées pour optimiser le débit du liquide de refroidissement et la distribution de la pression pour des applications spécifiques.
- Qualité et revêtement du carbure : Le choix de la nuance de carbure et du revêtement dépend du matériau usiné, des paramètres de coupe et de la durée de vie souhaitée de l'outil.
Tableau 1 : Aperçu des variations des tiges de carbure à trou de refroidissement
Fonctionnalité | Description |
---|---|
Nombre de trous pour le liquide de refroidissement | 1, 2, 3, ou plus |
Géométrie du trou de refroidissement | Droite, hélicoïdale, en forme |
Qualité du carbure | K10, K20, Micro-grain, etc. |
Revêtement | TiN, TiAlN, DLC, etc. |
Applications : Où les tiges en carbure à trou de refroidissement excellent
1 trou d'arrosage droit Les tiges en carbure ont révolutionné diverses opérations d'usinage, en particulier celles qui impliquent.. :
Forage profond :
- Composants aérospatiaux : Perçage de trous profonds et précis dans des matériaux aérospatiaux tels que le titane et les alliages de nickel pour les conduites de carburant, les systèmes hydrauliques et les composants structurels.
- Fabrication de moules : Création de canaux de refroidissement complexes et de cavités profondes dans les moules pour le moulage par injection de plastique et le moulage sous pression.
Usinage à grande vitesse :
- Industrie automobile : Usinage de blocs moteurs, de culasses et de composants de transmission avec une grande précision et une grande efficacité.
- Fabrication de dispositifs médicaux : Production de petites pièces complexes pour les implants médicaux, les instruments chirurgicaux et d'autres dispositifs médicaux.
Matériaux difficiles à usiner :
- Titane et alliages de nickel : Les capacités accrues de refroidissement et d'évacuation des copeaux de ces tiges permettent un usinage efficace de ces alliages à haute température.
- Aciers trempés : Le maintien d'une zone de coupe plus froide est essentiel lors de l'usinage d'aciers trempés pour éviter l'usure de l'outil et l'endommagement de la pièce.
Comparaison des fournisseurs de barres en carbure : Aperçu du marché
Fournisseur | Localisation | Fourchette de prix (par pièce, approximatif) | Spécialités |
---|---|---|---|
TRUER | Chine | $15 – $600 | Liquide de refroidissement personnalisé tiges en carbure de tungstèneLarge gamme de qualités et de géométries, prix compétitifs |
Sandvik Coromant | Suède | $25 – $700 | Outils de coupe haute performance, systèmes d'outillage, expertise globale dans le domaine de la coupe des métaux |
Kennametal | ÉTATS-UNIS | $20 – $650 | Science des matériaux avancée, solutions d'outillage pour les applications exigeantes, priorité à l'innovation |
Kyocera | Japon | $22 – $680 | Outillage de précision, outils de coupe en céramique, engagement en faveur de la qualité et de la fiabilité |
Gühring | Allemagne | $28 – $750 | Outils de forage et de fraisage, expertise en matière de forage profond, solutions de haute précision |
Tableau 2 : Naviguer dans le paysage des fournisseurs de barres de carbure
A noter : Les prix sont approximatifs et peuvent varier de manière significative en fonction de facteurs tels que la qualité, les dimensions, les spécifications du trou de refroidissement, la quantité et les conditions du marché. Il est toujours recommandé de contacter directement les fournisseurs pour obtenir des informations précises et actualisées sur les prix.
Avantages et limites : Une vision équilibrée
Avantages :
- Efficacité de refroidissement améliorée : L'apport ciblé de liquide de refroidissement réduit considérablement l'accumulation de chaleur dans la zone de coupe, ce qui améliore la durée de vie de l'outil, la qualité de la pièce et l'efficacité globale de l'usinage.
- Amélioration de l'évacuation des puces : Le liquide de refroidissement à haute pression élimine efficacement les copeaux de la zone de coupe, ce qui évite la recoupe des copeaux, améliore l'état de surface et réduit l'usure de l'outil.
- Augmentation de la vitesse de coupe et de l'avance : Des températures de coupe plus froides et une évacuation efficace des copeaux permettent d'augmenter les vitesses de coupe et les vitesses d'avance, ce qui stimule la productivité.
- Réduction de l'usure des outils : Des températures de coupe plus basses et une meilleure évacuation des copeaux se traduisent par une durée de vie plus longue de l'outil, ce qui réduit les coûts d'outillage et les temps d'arrêt.
Limites :
- Coût : Les tiges en carbure à trou de refroidissement sont généralement plus chères que les tiges en carbure massif en raison des étapes de fabrication supplémentaires nécessaires au perçage du trou de refroidissement.
- Risque de colmatage : L'orifice du liquide de refroidissement peut être obstrué par des copeaux ou des débris, en particulier lors de l'usinage de matériaux produisant des copeaux filandreux. Il est donc essentiel de mettre en place des stratégies de contrôle des copeaux et de filtration du liquide de refroidissement.
- Pression du liquide de refroidissement requise : Ces barres nécessitent généralement des pressions de liquide de refroidissement plus élevées que les systèmes de refroidissement par inondation afin d'assurer une distribution efficace du liquide de refroidissement et l'évacuation des copeaux.
Tableau 3 : Peser le pour et le contre des tiges de carbure à trous de refroidissement
Pourquoi choisir TRUER comme partenaire pour les tiges en carbure pour trous de refroidissement ?
TRUER se distingue en tant que premier fournisseur de tiges en carbure de haute qualité pour trous de refroidissement, offrant une combinaison convaincante de.. :
- Expertise en matière de personnalisation : Nous sommes spécialisés dans la conception de solutions de tiges de carbure pour trous de refroidissement afin de répondre à vos spécifications précises, qu'il s'agisse du diamètre et de la géométrie des trous de refroidissement, de la qualité du carbure, du revêtement ou des tolérances dimensionnelles.
- Fabrication de précision : Nos capacités de forage avancées et nos mesures rigoureuses de contrôle de la qualité garantissent l'intégrité et la précision du trou de refroidissement, ce qui permet d'obtenir des performances et une fiabilité optimales.
- Prix compétitifs : Nous nous efforçons de fournir des solutions rentables sans compromettre la qualité, en proposant des prix compétitifs et des quantités de commande flexibles pour répondre à vos besoins spécifiques.
- L'engagement en faveur de la satisfaction du client : Notre équipe dévouée s'engage à fournir un service et une assistance exceptionnels tout au long de votre parcours, depuis la demande initiale et la consultation technique jusqu'à la livraison dans les délais et l'assistance après-vente.
FAQs : Réponses à vos questions sur les tiges en carbure à trous de refroidissement
1. Quel type de liquide de refroidissement est recommandé pour les tiges en carbure à trous ?
Les liquides de refroidissement synthétiques solubles dans l'eau, souvent additionnés d'agents lubrifiants et anticorrosion, sont couramment utilisés avec les tiges de carbure à trou de refroidissement. Le choix du liquide de refroidissement dépend du matériau usiné, des paramètres de coupe et de l'état de surface souhaité.
2. Comment éviter que le trou d'arrosage ne se bouche pendant l'usinage ?
L'utilisation d'un système de refroidissement à haute pression, la sélection de stratégies de contrôle des copeaux appropriées (telles que les brise-copeaux) et l'utilisation d'une filtration efficace du liquide de refroidissement sont essentielles pour prévenir le colmatage des trous de refroidissement.
3. Les tiges en carbure à trou de refroidissement peuvent-elles être utilisées à la fois pour les opérations d'ébauche et de finition ?
Bien qu'elles excellent dans les applications exigeantes telles que le perçage de trous profonds et l'usinage à grande vitesse, les tiges en carbure à trou de refroidissement peuvent être utilisées pour les opérations d'ébauche et de finition, en fonction de la géométrie spécifique de l'outil et des paramètres de coupe.
4. Quels sont les signes d'une obstruction de l'orifice du liquide de refroidissement et comment y remédier ?
Les signes d'obstruction comprennent la réduction du débit du liquide de refroidissement, l'augmentation des forces de coupe et la détérioration de la finition de la surface. En cas de blocage, retirez l'outil avec précaution et nettoyez l'orifice du liquide de refroidissement à l'aide d'air comprimé, d'une brosse métallique ou d'outils de nettoyage spécialisés.
5. Quelle est la durée de vie typique d'une tige de carbure à trou de refroidissement par rapport à une tige de carbure solide ?
Bien que cela dépende de divers facteurs, les tiges en carbure à trou d'arrosage ont souvent une durée de vie plus longue que les tiges en carbure massif dans des applications comparables, en raison de l'amélioration du refroidissement et de l'évacuation des copeaux qu'elles procurent. Cela se traduit par une réduction des coûts d'outillage et une augmentation de la productivité au fil du temps.